COMPANY INSIGHT
Sponsored by Senstech
Innovative Sensor Solutions Thanks to Laser-Based Manufacturing
Senstech was among the pioneers of thin film sensor technology in the 1980s. In recent years, the manufacturing process has been gradually automated and complex photolithography processes have been replaced by femtosecond laser ablation. These changes have allowed the Swiss small business to remain competitive and to shorten the time frame of prototype developments.
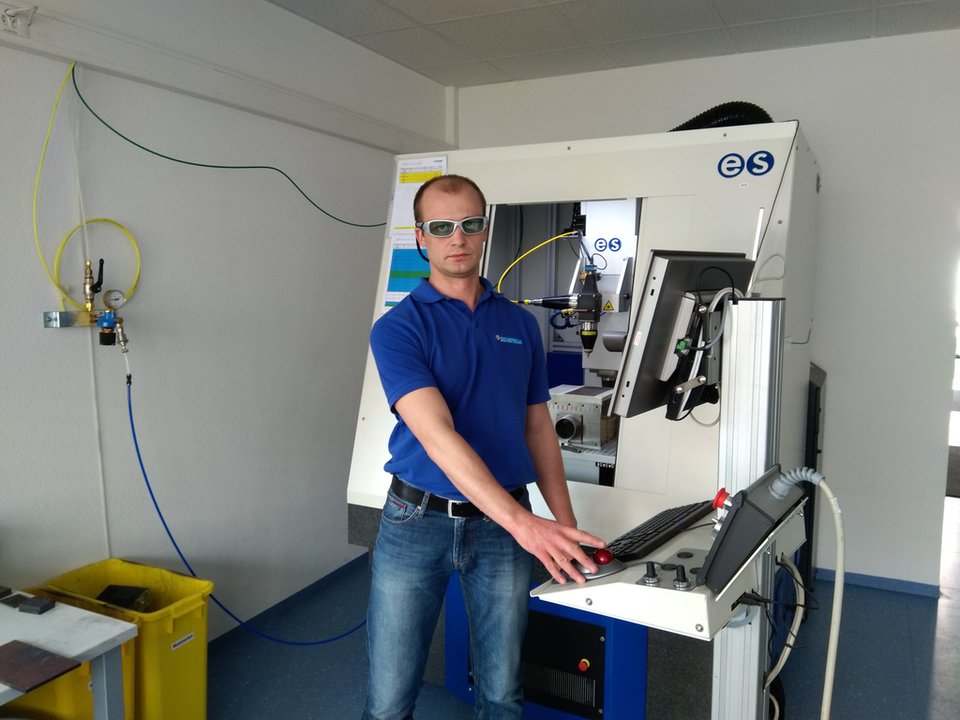
Substrates Cut by Fiber Laser
Senstech's thin-film sensors are based on metal substrates that are manufactured from various spring materials. For many types of sensors, we cut the substrates from sheet metal with our fiber laser. They are then finished using a brush polishing machine and an ultrasonic cleaner. During the manufacturing process, up to 36 sensors remain together in one panel, connected by narrow bars. A measuring projector automatically checks the dimensions of the finished substrates.
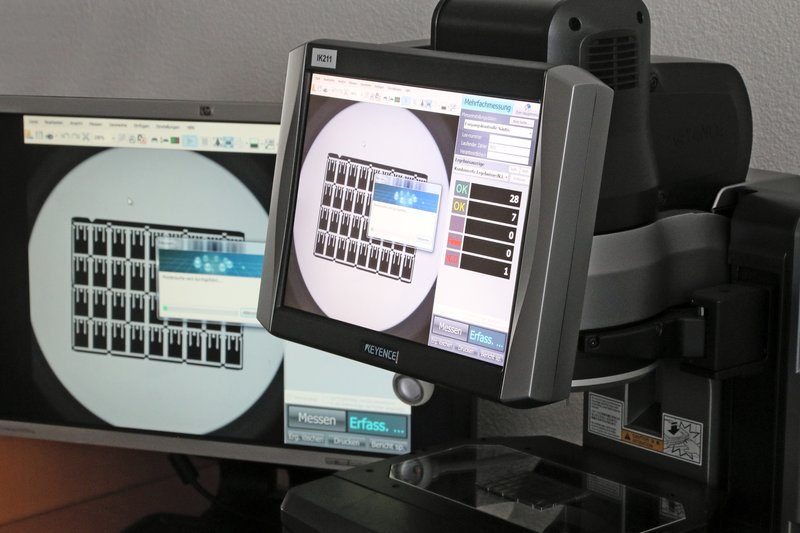
A measurement projector is used to assure the quality of sensor substrates
Thin Film Build-up using Sputtering Systems
The thin-film structure is created on the sensor substrate in several steps: First an insulation layer of quartz is applied, then several metal layers are added.This is done with sputtering systems, which bombard the coating material with ions in a vacuum and thereby transfer its atoms to the sensors. All layers are applied over the entire surface, except for the supply lines and solder pads, which are created by a photolithography process.
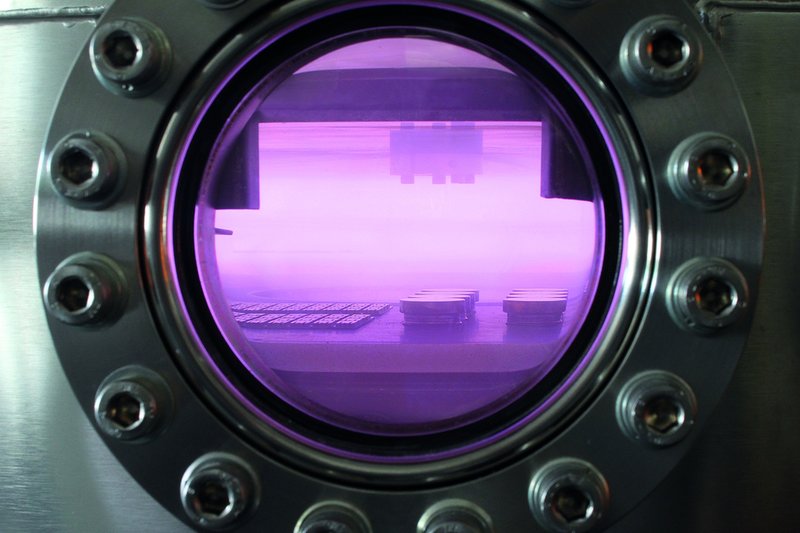
View into a sputtering system while depositing a thin film
Structuring with Femtosecond Laser
The meanders, trim surfaces and other fine structures of the sensor are created with the femtosecond laser. It can ablate the metal layers without damaging the underlying insulation layer. Thanks to the integrated measuring system, the laser can also trim the sensors automatically.
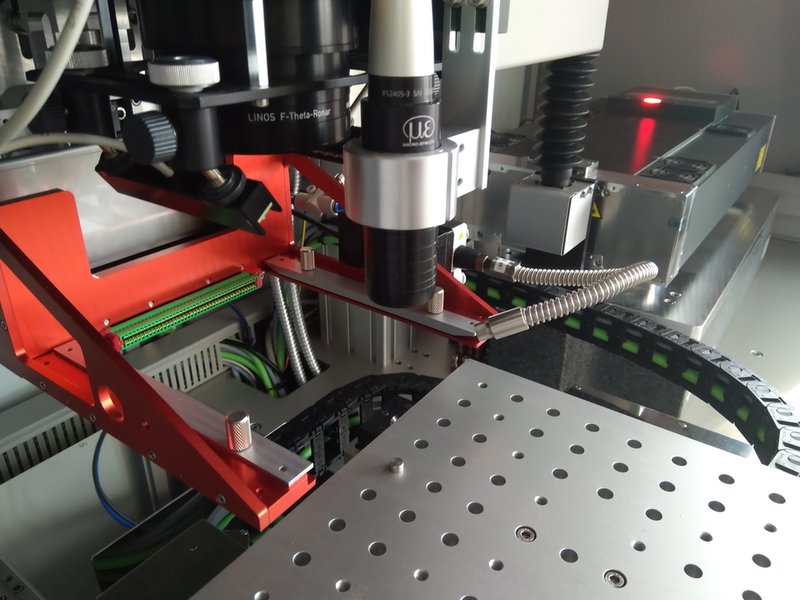
Inside view of a femtosecond laser trimming system
Vapor Phase Soldering
Many of our sensor elements are contacted with flex connectors. In the vapor phase soldering system these can be soldered directly onto the sensor. It is also possible to place signal amplifiers onto the metal substrate.
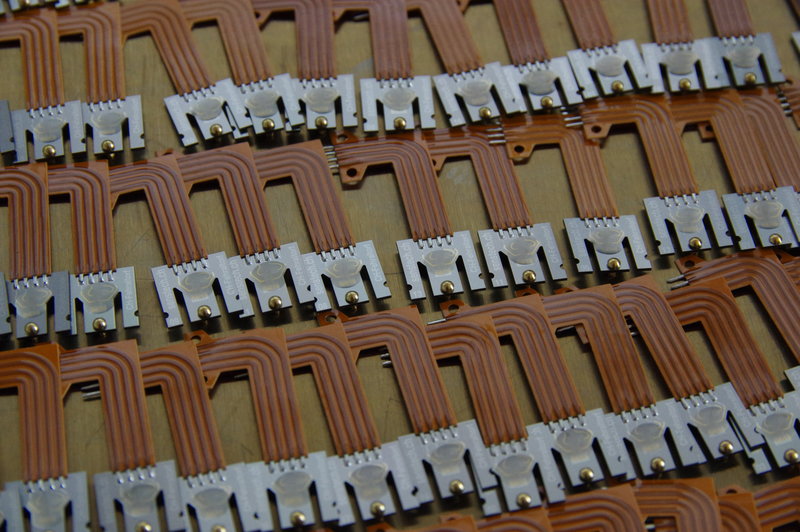
Small force sensors with flex connectors
Superior Sensor Properties Thanks to Thin-film Technology
Due to the direct application of thin metal layers there are no creeping effects between substrate and strain gauge. This favorably affects the achievable sensor properties:
- Best long-term stability with drifts < 0.03%/year
- Very good temperature stability, typically < 0.01 %/°C without compensation
- Very good linearity
The good signal quality means that no complex signal processing is required for most applications.
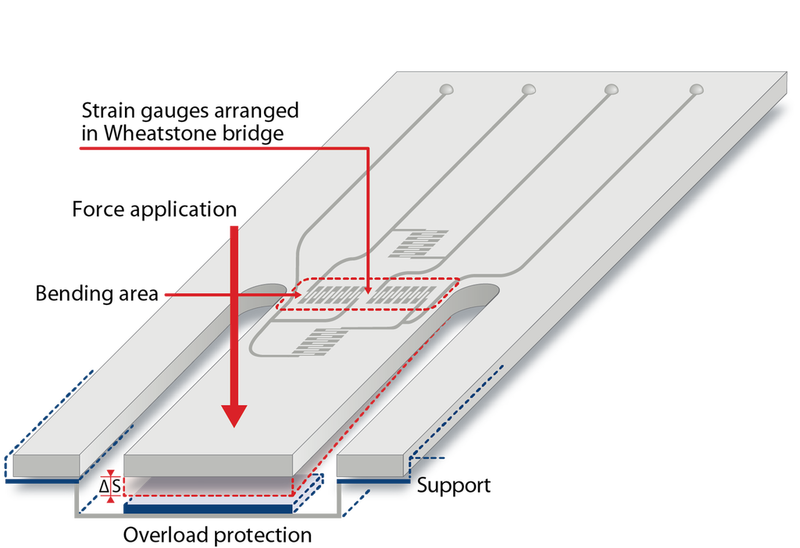
Design of a typical force sensor
Rapid Prototyping Thanks to a Large In-house Production Depth
Senstech can perform all steps in the production of thin-film sensors in-house. Parameters such as geometry, material, measuring range or electrical interfaces can be adapted to customer requirements. Thanks to Laser Technology, the effort involved is kept within limits even for small batch sizes. We are therefore a good partner for the development of OEM sensors for medical technology applications. Measuring elements for force, pressure, displacement, torque and other variables can be realized with our technology.
Reliable and Reproducible Fabrication for Years
For more than 30 years Senstech has proven itself as a reliable manufacturer of thin-film based sensors. The basis for this success is the well-trained and motivated staff, the proven production facilities and the processes certified according to ISO 13485 and ISO 9001. Do you need a reliable and affordable sensor for your medical device? We will be happy to advise you.