Rel8 Aps now launches a new standard in traceability, which will be known under the “imZERT” brand name. Rel8 is a recent start-up, launched by a strong group of investors to solve the problem of missing traceability in plastic products. Rel8 has proven its technology together with strong R&D partners in Denmark, including the Technical University of Denmark, the Technological Institute, Force and DFM.
Several production trials have been held with large Danish manufacturers, showing the technology is durable in production, and is compatible with in-line Vision and barcode scanning systems. Independent trials have confirmed that imZERT barcodes are compatible with all tested in-line Vision and barcode scanners, even at small sizes. Smartphone apps aimed for DPM can scan our barcodes, and in combination with a microscope it is possible to scan the very smallest barcodes. Handset scanners for now require larger barcodes, although developments are on-going.
Based on these strong results, Rel8 offers the exciting new imZERT technology, to meet with strong forces in manufacturing of plastic products, including Industry 4.0, the eternal demand for raising Quality, the need to reduce Waste and Resource Consumption within production, the desire for highest attainable level of Traceability, and the need to offer solutions for Recycling of materials. A rising challenge is posed by Fake Devices causing damage to patients and companies alike. The imZERT technology addresses all these challenges.
“World’s Smallest Barcodes” for injection moulding
imZERT lets you apply small, machine-readable 2D barcodes directly on your plastic components and products. The 2D barcodes can follow the GS-1 Datamatrix standard, the QR Code standard, or any other open or proprietary standard.
The barcodes can be exceedingly small – we have demonstrated barcodes down to 1x1 mm2. The bit module (pixel size in the barcode) can be less than 100x100 µm2, and eventually down to 10x10 µm2.
The barcode content can be anything specified – numbers, letters, symbols – as permitted by the chosen standard. The 10x10 Datamatrix encodes up to 6 digits, the 20x20 version up to 40. It is now possible to represent any information directly on the part, and we suggest to use combinations of “fixed” information (Product/Component ID, Manufacturer as examples), while the remaining part is a key, which can be updated and allocated in an independent data operation.
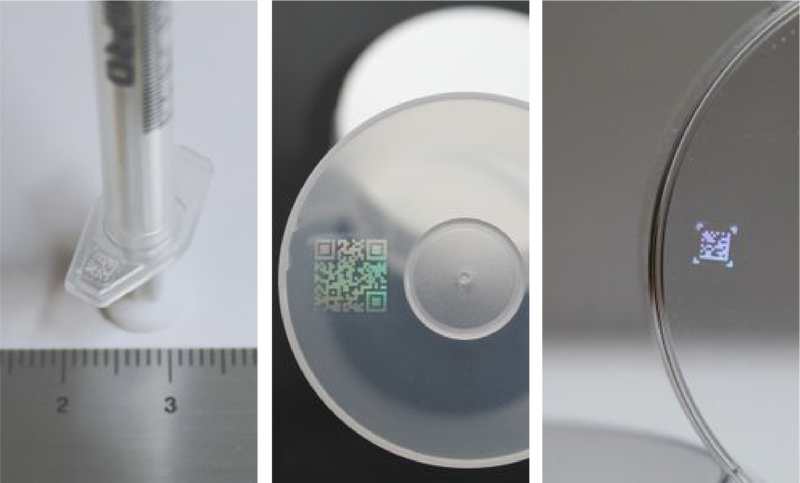
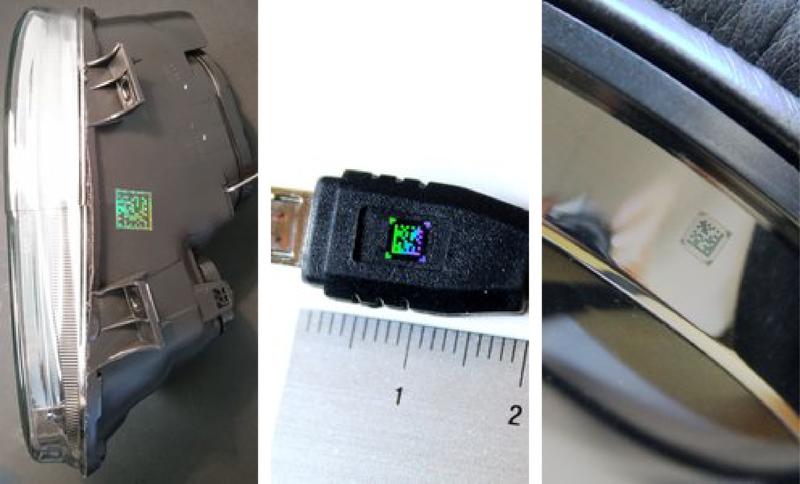
The 2D barcodes are applied directly to every single part DURING moulding. This is achieved by means of a nanostructured insert. The nanostructures are replicated in every single part, without any transfer of material. As the nanostructures are fully embedded in the plastic, there is absolutely no risk of contamination. The imZERT method is cleaner than any other Direct Part Marking method, including laser engraving, labelling, ink-jetting and dot-peening.
The technology is implemented in every single mould cavity, by means of steel inserts having standardized geometries. This allows for marking to indicate which specific cavity and mould a given part came from, as well as many other technical or logistical details. imZERT also supplies a rapid exchange framework, allowing for batch or lot identification, directly on the part. It is important to note that a single insert replicates the same information every single time – however, individual cavities and batches can be provided with unique identity.
imZERT is provided by Rel8 according to customer specification – the customer or sub-supplier specifies the content, size and insert geometry, which is then delivered. It is also possible to add customer specific details, preferably in collaboration with the mould maker or technical lead.
imZERT adds the missing piece, allowing for traceability systems to include the plastic components. Vice versa, it also becomes possible to use the traceability on the plastic to create “virtual assembly lines” through a factory, or to transfer traceability from the plastic to other components or contents.

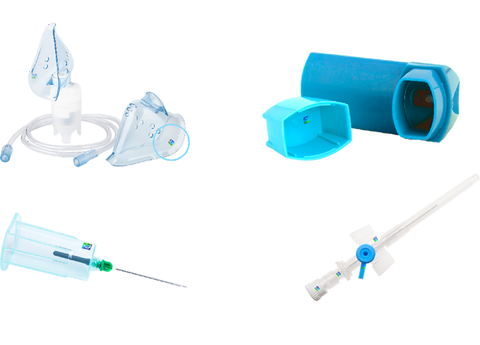
Embed the Information on the Part!
- Unfalsifiable Anti-Counterfeit protection
- Track and control sub-supplier Quality
- Component verification at all critical steps
- Intelligent sorting of process flows
- Improved Lean, less waste, higher efficiency
- Strongly reduced error rates in all processes
- Automation of all Quality Processes
- No mix-ups during assembly and packaging
- Reliable product identification with Part Revision
- Simplified compliance
- Track R&D development steps
- Supply Chain Management and transparence
- Industry 4.0 at lower cost
- Improved recycling
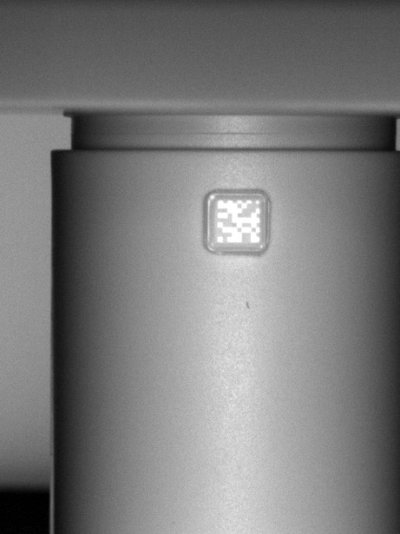
Customer Trial
A full production trial was performed with large Danish medical device manufacturer
- Drug delivery device component
- Providing assembly mix-up check
- Compatible with existing in-line Vision system
Trial features:
- 2.4 x 2.4 mm2 barcode
- White Polypropylene
- Standard Vision
- Mould insert
imZERT is a unique technology, combining several novel features:
Smallest and most accurate DPM technology
DPM applied during moulding, linking back to moulding cavity
imZERT nanostructures have highest contrast of any moulded DPM on plastic
No need for any automation equipment or maintenance
No risk of breakdowns in production
No contamination of the product
No need to modify validated moulding parameters
Compatible with all polymers and elastomers, of any colour
mZERT traceability can help to solve a range of problems. A few use cases include:
Assembly check: are the correct parts and part revisions being assembled? These checks can be automated to remove risks of mix-up and to avoid manual interactions.
Packaging check: are the correct parts being packed? Today, confirmation checks are near impossible, and provided typically in the form of line bills or container box markings.
Cavity failure mitigation: Which cavity in the tool is failing? Multi-cavity tools often experience failure, creating the need to remove non-compliant parts. Automated scanning enables ejection of affected parts and assemblies only, while hot-runner technology allows shutting down only failing cavity.
Zero-variation lots: All mouldings originating from a single cavity can be sorted into single lot, minimizing any variations between parts.
Storage automation: Accurate information on part reduces the risk of selecting wrong parts from any parked or stored position.
Quality comparison: When multiple moulds and/or sub-suppliers make comparable or identical products, DPM can help to compare Quality across operations.
New product R&D: Prototyping of new products requires accurate Revision control and identification. Full clarity is achieved with DPM Traceability during any developments and pilots.
Revision ID: When products undergo timely updates, small changes can be difficult to see with naked eye. Automated DPM checks ensure complete line clearance of old revisions.
Anti-counterfeit: Overt and covert imZERT DPM provides plastic products withnanostructured markings that are near impossible to fake. Geometrical details can be included with 200 nm accuracy, which can only be detected with Scanning Electron Microscopy. DPM with careful coding schemes can support investigations and strengthen any legal case.
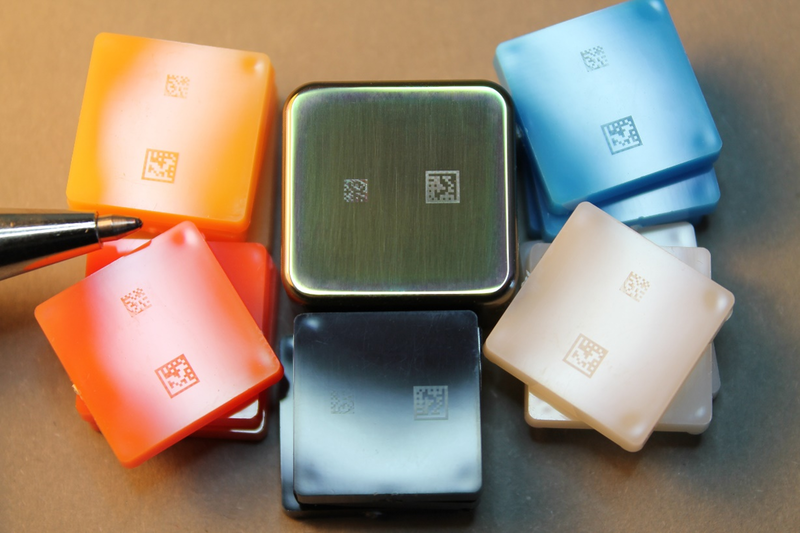
Features
High-quality Direct Part Marking
High-contrast Nanostructures
Microwriting for additional protection
Inseparable from part
Falsification near impossible
2D barcodes down to 1x1 mm2
ID can include:
Part/Product + Mold/Cavity
Batch/Lot
Assembly/Content
Supplier/Distributor/Customer
R&D Prototype stage
Revision Update
Distribution Region/Country
Technical Advantages
1 work-cycle – marking without manual labor or equipment
Traceability starts at moulding
No impact on molding process
No contamination
No marking equipment
No maintenance – no breakdown
No labels. No RFIDs
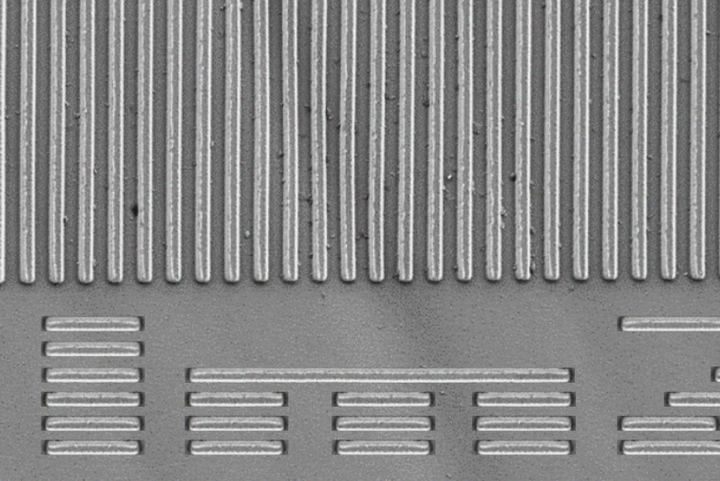
Contact us now!
Email: info@rel8.dk
Phone: +44 45-51974724
rel8 Aps
Savsvinget 4A
2970 Hørsholm
Denmark
- Receive your free moulding samples
- Get information about moulding trials in your equipment
- Try out our Development Kits