COMPANY
INSIGHT
Laser welding of COVID-19 diagnostic cartridges
Sealing of micro- and macro-fluidic assemblies for medical diagnostic has been a topic since many years. In the past most application targeted to screening different types of disease in one cartridge. With the Corona crisis the focus shifted to detect a single virus in a short time and large quantities of tests available.
Why diagnostic cartridges for COVID-19?
We all hope to have an effective vaccine against COVID-19 one day. But up to then, the only solution to monitor and manage further outbreaks of the disease is testing, contact tracing, isolation and quarantine.
Providing large enough test capacities is absolutely crucial. Central labs can run very efficiently many tests in parallel with high quality standards at a moderate price level. However, with the logistics forth and back to the patient important time is lost and results are usually only available in 24-48 hours.
With decentralized point-of-care (POC) tests and results within 1 hour, the spreading of Corona virus can be better contained. However, the complete process carried out in central lab as e.g. the DNA amplification by PCR, has to be integrated on a simple to use cartridge, which can be inserted in a local analysis device.
With large enough capacities of cartridges and analysis devices people could be tested on a regular periodic schedule or at critical points as e.g. before boarding an airplane or ship or upon arrival at immigration.
What are the advantages of laser welding?
Diagnostic cartridges typically consist of multiple plastic parts, which need to be joined leak-tight. Traditionally, adhesive or thermo-bonding have been used. Both have long cycle times for joining and adhesive the additional disadvantage of potential contamination by the adhesive. For smaller layouts also ultra-sonic welding has been employed, but with the risk of particles from the process contaminating or even blocking fluid channels.
Laser plastic welding allows for a very clean, precise, and fast joining process. The laser beam is incident through the transparent part or foil and is absorbed by the laser-absorbing part underneath, which starts to melt on the surface. As the parts are pressed together during the process, also the upper part melts on the surface by heat conduction and the polymer melts of both side mix, providing a firm and leak-tight bond after cooling down and solidifying. Nearby areas are not heated and affected at all (e.g. with reagents for the diagnostic test).
The technique can be applied to very small channels of some hundred micrometer size or to more macro-fluidic layouts, with typical welding times of some seconds.
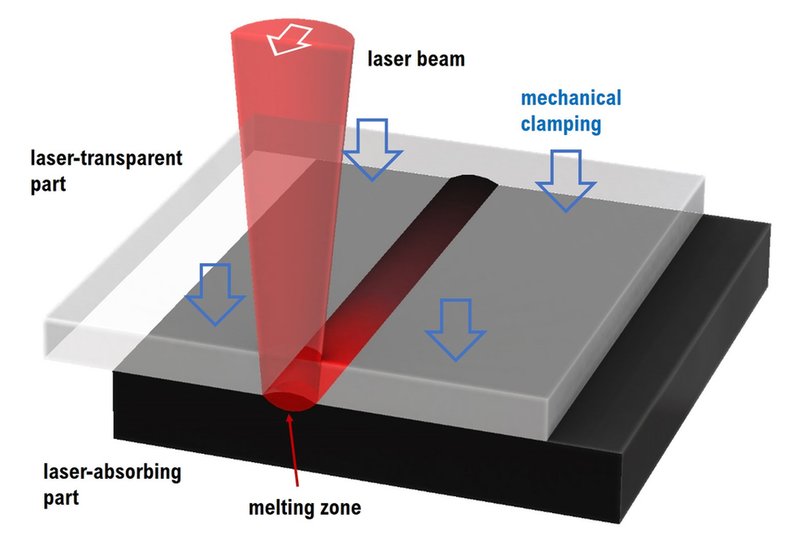
Basic principle of laser plastic welding
Which process types are best applied?
For welding diagnostic cartridges either contour or mask process are applied best.
In contour process the laser beam is moved along the seam to weld locally in a sequential scheme. Instead of normal servo-axes a scanner optics, steering the beam by two pivoting mirrors, is recommended to move the beam faster. Also complex channel layouts can be welded within seconds.
In the mask process a glass plate with the desired weld seam structure is placed above the cartridge. A line-shaped laser sweeps over the mask and welds in parallel all areas, where the mask lets the beam go through. In order to have no distortion from the mask to the welding plane a collimated line laser should be employed with the laser rays parallel to one another.
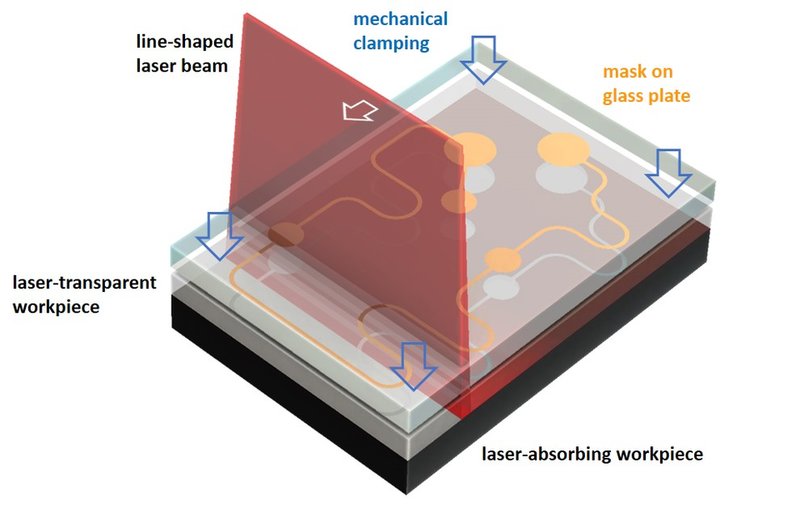
Mask welding with a line-shaped laser beam
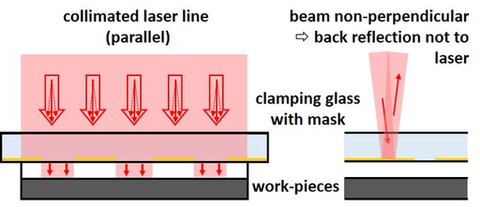
With a collimated line beam the rays are parallel and no distortion between the mask and the welding plane.
Which type of machine?
The best type of machine depends on the layout of the diagnostic cartridge and the production concept. ProByLas AG offers several different possibilities.
Turnkey S is a compact ready-to-use table-top system. It can weld cartridges up to 150x100 mm with mask process and 100x100 with scanner in contour process. A rotary table is optionally available to increase productivity.
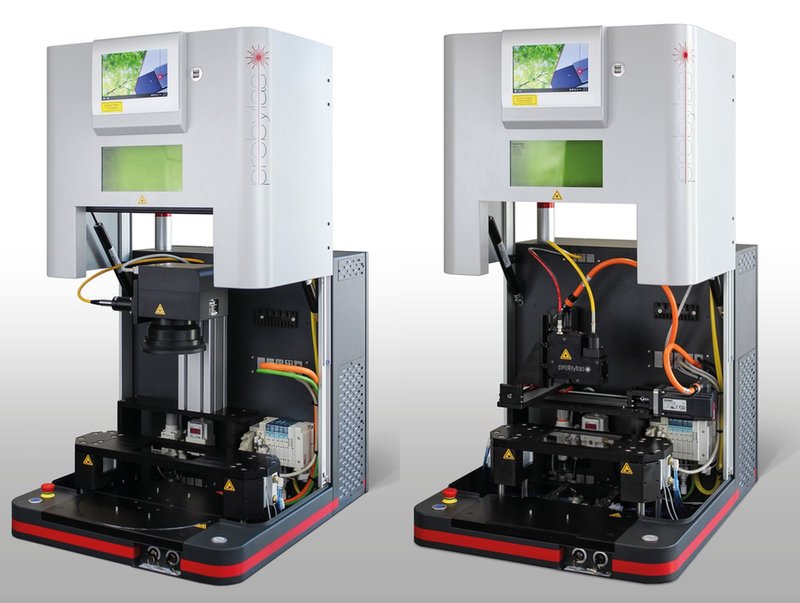
Compact and modular ready-to-use Turnkey S in different configurations
Modula laser units and optics are for integration by a special machine builder in a production line. The key components are the laser with the controller inside and the scanner optics focusing and moving the beam at the same time. Additionally, also the clamping unit or its key components can be supplied by ProByLas AG.
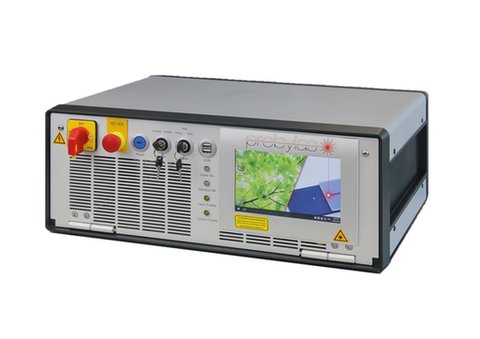
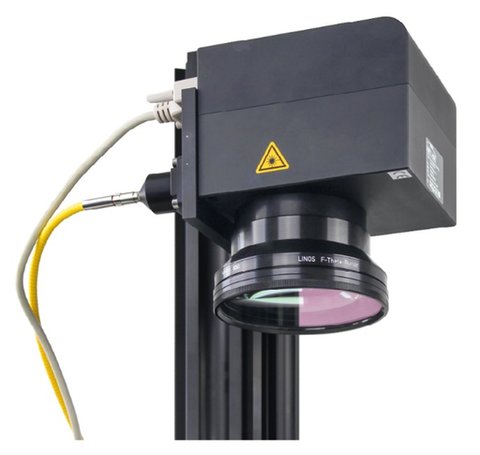
Modula laser unit and scanner optics for integration in a production line.
An intermediate step between the ready-to-use Turnkey S and the Modula components is the Modula Assembly Inline. Besides the Modula laser unit, it has a process unit, which already contains the scanner optics and the clamping so that it can be easily integrated over a transfer belt or a large rotary table.
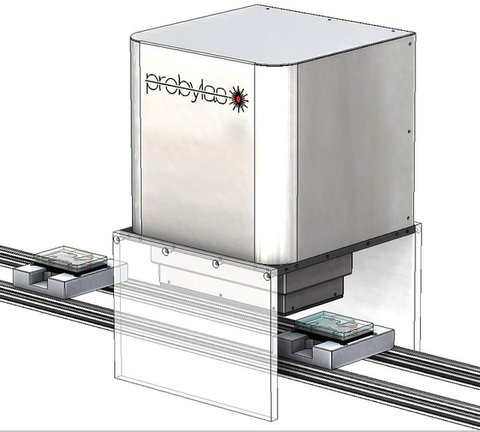
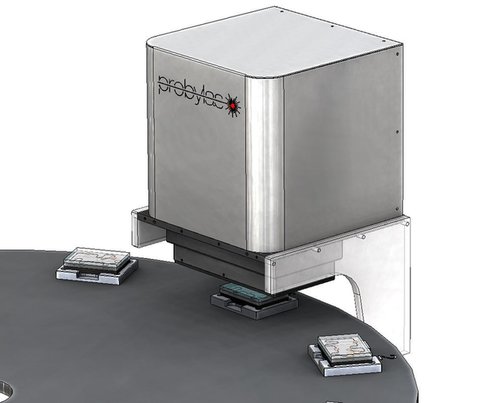
Modula Assembly Inline with process cell for easy integration on a transfer system or a large rotary table.