Product Development’s plastic nightmares
- and how to avoid them
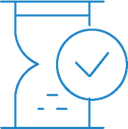
Launch on time
Developing new components for the medico industry is often a challenge. By knowing the entire value chain, design can be optimized for reliable manufacturing.
This can reduce time-to-market by a factor of three
and gets your product on the market on time.
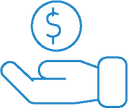
Too expensive
Deep insight into and experience in technical injection moulding, inclusive 1, 2, and 3K moulding help to simplify and improve processes.
We help customers to reduce both investments and costs by up to 40%.
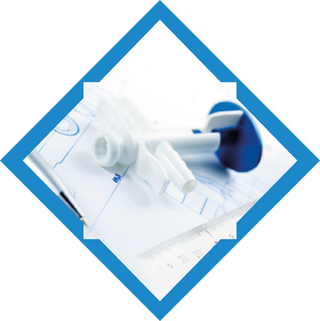
Plastic components for medical devices
The unsolvable problem
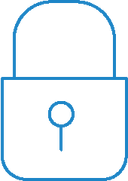
With more than 60 years ‘ experience - and the availability of best competences within the industry - it’s possible to solve otherwise unsolvable problems –
e.g. delivering components below 1 CFU (bioburden) while eliminating the need of sterilisation.
Too complex
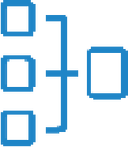
By innovative “design thinking” and inline processes combined with new technologies,
your production processes can be reduced from e.g. 4 to 1 step. This will improve quality, component robustness, and prevent e.g. leakage
Curious to know more about Carmo?
Launch on time
We are build to suit demanding global medico companies and have helped customers
shortening the time-to-market radically – in some cases by a factor of three.
This is possible because we have:
- An understanding of the iterative process of ideation and product development – because we also develop and maintain our own product range
- Agile production setup - from prototyping to advanced high volume production
- Competencies to build advanced automation cells in-house
- Development and production under one roof - igniting innovation and creativity.
Less expensive
We have a world class team of in-house technical experts within injection moulding, automation, and robotics. They help our customers to consolidate the manufacturing processes. This reduces risk of failure and contamination –
customers have also experienced an increase in production efficiency of 20%.
- ISO 13485
- Clean Room class 8
- Medical Components class 1 + 2
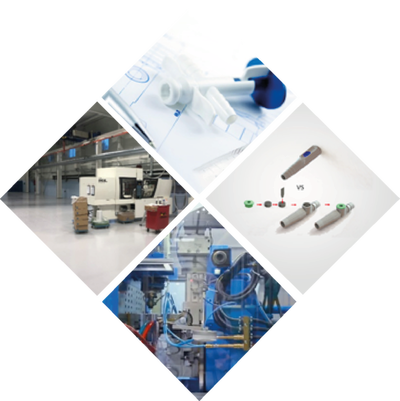
The Unsolved Problem
During the past 60 years, Carmo has designed and produced components for critical and challenging applications.
Our know-how and experience combined with a hunger
for challenging problems, have resulted in innovative,
yet robust solutions.
Like eliminating the need of sterilisation or moulding
leakage proof valves, in one process
This is possible because we:
- Have solved problems within the moulding of medical components for global customers for the past 60 years
- Optimize for the extended supply chain, by understanding the product and manufacturing processes of our customers and suppliers
- Take pride in challenging technical conventions and ideas, yet adhering to regulations and customer and end-user requirements.
- Have a committed management (average 15+ years) and workforce (average 10+ years) with experience in manufacturing within Medico and Pharma technologies.
Less complex
Within particularly the medical device industry, less complexity and fewer components can increase quality and safety, whilst reducing the risk of end-product contamination. We help our customers to design and produce medical components that are less complex.
We have successfully simplified medical components from 3 parts to 1 piece.
Challenge us – give us a call!
+45 4912 2100 denmark@carmo.dk
Product Development Services
The Carmo Advantage
With high-volume production continuously moving to low-cost geographies, more and more product developers are losing the know-how, experience and feel for production, so crucial to designs that can be efficiently produced.
Carmo continues to be amongst the few Danish companies with a fully functional production setup and the competencies, know-how and experience from daily production and hands-on problem solving.
We have it … and we are eager to share that with our development partners.
Too expensive
Computers and simulations can bring you a long way, but never all the way: The last bit will be based on experience, experimentation and innovative thinking.
Successful injection molding development projects are a constant compromise and interaction between Industrial and mechanical designers, tool makers and production. Only by effectively bridging the world of sketches and 3D modeling – where almost everything is possible, and the world of the toolmaker where nothing is possible can you realize innovative AND cost effective solutions.
Through the years we have established a network of Industrial and mechanical designers and toolmakers that we have a successful track record with, however we are always open to cooperate with new partners.
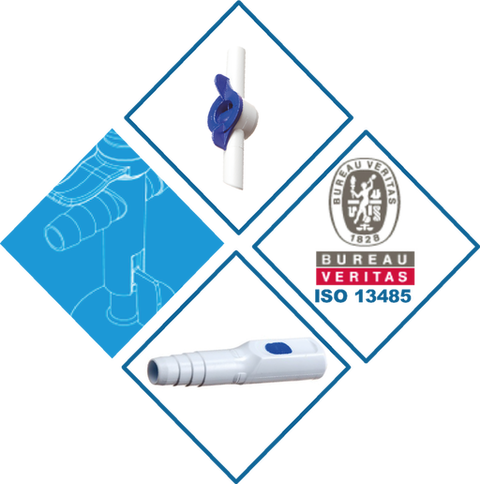
Advanced Design
One thing is to find a technical solution. Another is to find a commercially feasible solution and yet another is to find solutions that will integrate smoothly and ensure that the processing down the line will run effectively.
We use all of our know-how and experience to ensure that components can be readily integrated into the production processes e.g. assembly, printing, packaging and sterilization. In many cases we have even been able to leverage our abilities in robotics and 2K moulding to totally eliminate difficult or expensive post processing and assembly tasks.
Carmo’s Experience
We know by experience that plastic processing can be challenging: That the process and material will never perform exactly the same way as last time and that materials behave differently during and after the injection moulding process.
Components will change properties depending on storage conditions, time, assembly processes and sterilization. And change properties over time in harsh environment, e.g. marine and arctic usage scenarios.
We know how to fine-tune the material recipe and compensate for these changes already in the design and geometry setting stages, ensuring end products with the functionality, surfaces and quality desired.