WEB: components.asahi-intecc.com
EMAIL: emea-oem@asahi-intecc.com
TEL: +31(0)20-794-0643
Asahi Intecc Co., Ltd. is an ISO13485- and ISO9001-certified Japanese medical device manufacturer. We are specialized in custom-made flexible ultra-fine wire ropes and tubing with high torsional rigidity, such as the single layer ACT-ONE cable tube and the multi-layer Torque Coil.
We also offer in-house coating and parts laser-weld or crimp assembly services to our micro rope and tube components. Drawing from our vast experience in the medical device field (e.g. vascular, structural heart, endoscopic, minimally invasive and other devices), our in-house wiredrawing, wire-forming, coating, torque and assembly technologies provide a broad range of options for your device.
Four Core Technologies
Product Development Flow
EMEA Sales (Netherlands)
- Sales & Customer service
In order to meet the growing demand of medical device components and (sub-)assemblies in Europe, the Asahi Intecc Components/OEM Sales and Marketing office was opened in July 2015. Conveniently located near Amsterdam Schiphol airport, our staff can easily travel Europe, Middle-East and Africa.
R&D Centers (Japan)
- Prototyping (<500 units)
Medical devices require expertise in different types of materials. Asahi Intecc has established R&D bases for several different fields.
Seto factory: The Seto base specializes in R&D for medical products. Feedback from clinicians is translated to product development and prototype production with rapid and detailed response capabilities for trial production.
Osaka R&D Center: The Osaka base specializes in R&D of metal materials. It develops and customizes different metal-based rope, coil and cable tubing.
GMA R&D Center: This R&D center was opened in Fukuroi, Shizuoka in 2013. Its main focus is R&D on resin products, tubing and coating.
Production sites (Thailand, Vietnam, Philippines)
- Production (>500 units)
Thailand: This is the first production base that Asahi Intecc established outside Japan. Japanese and local staff work together to create structures to perform all the processes from development and prototype production to production and shipping.
Vietnam: This factory manufactures PTCA guide wires and catheter guide wires using the material and components produced at the Thailand site.
Philippines: The Toyoflex Cebu factory is our third largest manufacturing base. It produces high quality products based on the high-level mass production technology developed in our Thailand and Hanoi sites.
Office address:
Asahi Intecc Co., Ltd. Europe Office
Strawinskylaan 527
1077XX Amsterdam
The Netherlands
Wire drawing
Asahi Intecc’s high-precision wire drawing technology lies at the core of our medical device components. A key part of the wire drawing technology is maintaining the precision of the ‘die’. In order to maintain the precision of the shape of the die, Asahi Intecc has introduced a high-precision die shape inspection device to measure the center hole of the die at an accuracy of a few microns. Through rigorous management of the wire drawing process, high-precision parts can be achieved.
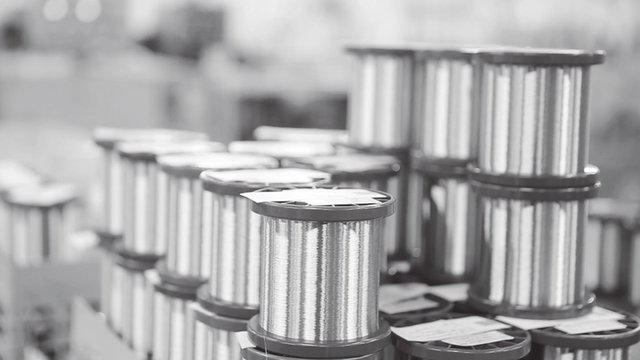
Wire forming
Asahi Intecc’s wire forming technology is applied to produce different types of micro ropes, cable tubes and coils. The technology is also used for different types of (micro-)catheters, in the form of wire braiding. This braiding increases the strength and torsional rigidity of catheters by weaving wires with a diameter of 30 to 60 micron and embedding them into polymer-based catheters).
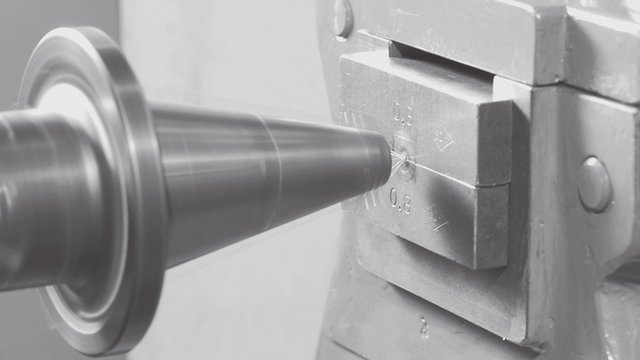
Coating
Asahi Intecc Co., Ltd. has a large portfolio of polymer coatings available for medical devices in a wide range of applications. These are supplied both as coatings for our stainless-steel products, as well as stand-alone polymer tubing. We offer extruded tubing at high accuracy according to the needs of customers.
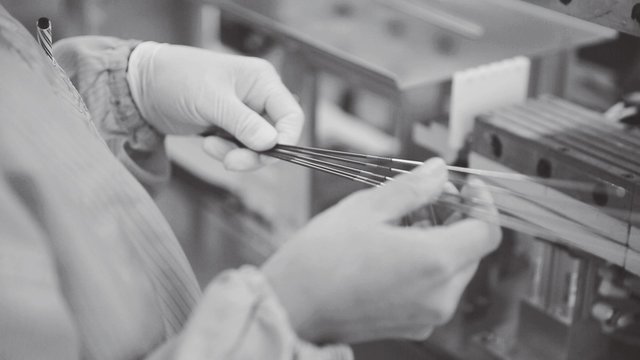
Torque technologies
Asahi Intecc’s medical devices are highly evaluated in the market due to their excellent torsional rotation capabilities. This is made possible by Asahi Intecc’s own processing equipment and propietary torque technologies. We apply these technologies onto our guide wires, catheters and many other component products to realize advanced operability.
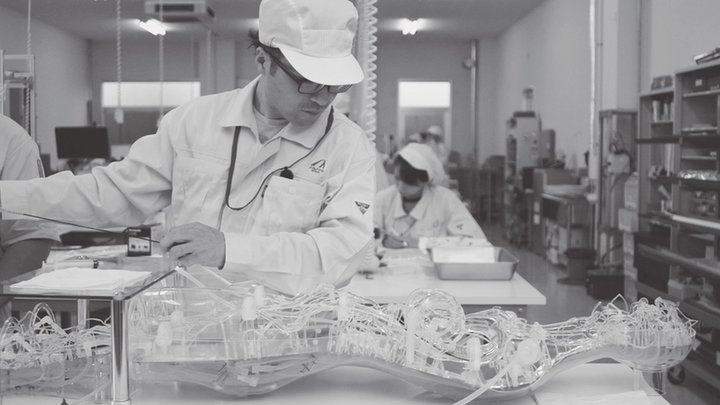