COMPANY
INSIGHT
Watlow
Watlow provides clinical diagnostic equipment OEMs with proven solutions which enable exceptional thermal control. We accomplish that with rapid prototypes and leading thermal technologies that meet the most demanding product specifications.
Global supplier of medical heating components
Watlow is the world’s largest electric heater, sensor and temperature controller manufacturer. As a global company, we support international design guidelines and agency approvals. Watlow produces thermal products that meet agency approvals, including RoHS, W.E.E.E, CE and UL®.
Engineers in medical devices and analytical instruments
We are experienced engineers in the field of thermal components and heaters for medical devices and analytical instruments. Watlow is a reliable life science partner, providing support to meet your specific application requirements.
By partnering with Watlow, you can take advantage of our extensive expertise, as well as our vast selection of efficient thermal components.
Cartridge Heaters Warming Premature Infants
Summary:
- Watlow’s engineering and manufacturing expertise can be a differentiator with customers.
- Laser blackening of a cartridge heater is a good example of being innovative with a well-established product.
- Years of testing may be required for life science applications.
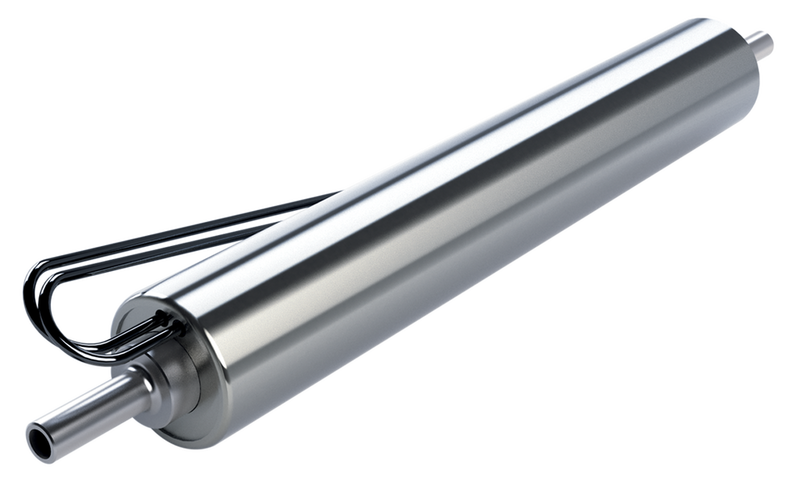
It is critical for premature infants to maintain a constant temperature. Premature babies normally have little body fat and can struggle to regulate their own temperature. Infants can lose body heat four times faster than adults, and if a baby’s skin temperature drops just one degree, the baby’s oxygen use can increase by 10 percent.
In neonatal intensive care units, keeping an infant’s temperature stable is a challenge when doctors and nurses are treating these small patients. A company based in Germany has been working closely with Watlow for about four years to develop a new line of infant incubators that provides the constant temperature these small babies require.
The enterprise manufactures medical devices for hospitals as well as safety products for emergency services, law enforcement, mining and industry. The company’s incubator brings new technology to improve care for premature infants.
“In a former device, they used a ceramic heater in the reflector,” said Torsten Roth, key account manager in Germany. “The infant beds are rolled around a lot and when they hit doorways, it would shake the bed and break the ceramic heater. Obviously, they don’t want pieces of the heater to fall on the babies.”
The new incubator provides multiple sources of heat to keep each baby’s temperature constant. The customer approached Watlow’s former site in Kronau, Germany to provide a pair of FIREROD® cartridge heaters for each reflector over the infant to provide heat when the lid of the incubator is opened for access to the baby. The work was eventually shifted to Watlow in St. Louis where development has continued during several rounds of testing.
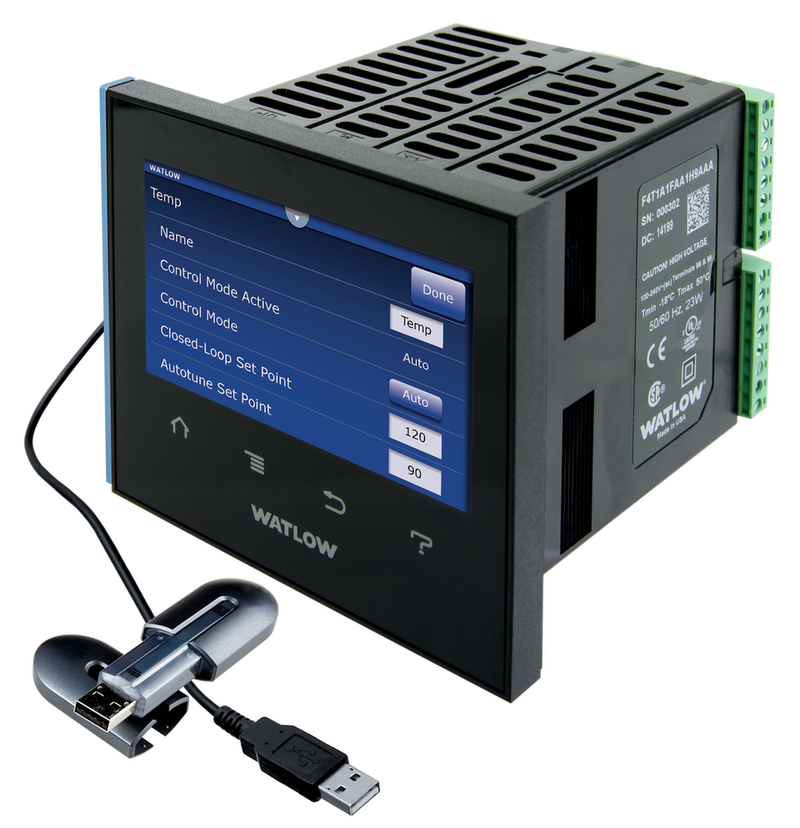
The reflector uses radiant heat to provide a constant 37 degrees Celsius temperature for the infant. In the warmup stage of the device, the heaters ramp up to 600°C. To ensure efficient heat transfer to the infant, the surface of the FIREROD heaters are blackened by lasers to improve the emissivity of the heaters. There is better radiant heat transfer from a black surface compared to a shiny metal one.
A St. Louis company does the blackening of the heaters with a laser, meaning there is no paint or covering to flake off above the baby over time. Additionally, parts are only shipped to Germany once after all the work on the heaters is completed in St. Louis. During reliability testing, engineers changed the pin wire inside the cartridge heaters to prolong the life of the product.
The company also had a requirement for the heaters to have low leakage current. The FIRERODS have an 8 mm core inside a 10 mm sheath. By reducing the diameter of the ceramic wind core, the distance between the element wire and the metal sheath increased. That’s important because it allows more ceramic fill material which increases the thickness of the dielectric layer. That in turn reduces the leakage current.
“Testing is very crucial in this application because the equipment is all about helping small babies,” Torsten said. “Our client has other suppliers for cartridge heaters, but none of them could meet this high-performance application. Watlow has shown through the testing and development that we have the engineering team and the manufacturing capability to make it happen.”