COMPANY
INSIGHT
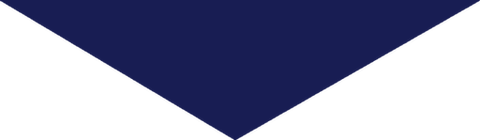
The art of metal processing
Medical technology solutions from the Klingel medical metal group offer maximum precision and quality made in Germany and Switzerland. We use state-of-the-art machinery for processing high-grade metal and plastic parts for renamed compani
es in the medical industry, made of difficult to machine materials, such as titanium and stainless steel.The following are a few of the key medical applications where ElectroCraft motors empower medical motion control.
In our four plants, located in the “hot spot” precision engineering areas in Southern Germany and Switzerland, we produce implants, tools and instruments for the dental and orthopaedic technology as well as components for minimally invasive and robotic surgery, cardiovascular systems and medical devices. With 600 employees, the Klingel medical metal group is one of the leading companies in its field today with well-known customers all over the world.
A sound knowledge of the specific properties of the material used and taking these properties into account in the manufacturing process are the most important prerequisites for the production of high-end components in different dimensions, shapes, tolerances, and complex geometries. The Klingel medical metal group manufactures on 21,000 square meters shop floor space utilizing over 300 CNC-machines in up to three shifts. Additionally, several wire and sink eroding machines as well as special testing/measuring machines and laser systems for welding and marking are in use and we continually invest in technical upgrades and automation.
From small and mid-size series up to six-digit mass production quantities, Klingel produces high-precision mechanical CNC turned and milled parts, wire-eroded, ready-to-install and 3-D free-form components for a wide variety of industries – even at short notice if required, and with packaging and logistics included. Since the inception of Klingel medical metal in Pforzheim in 1986, the full contract manufacturer has consistently grown organicly but also through acquisitions both in Germany and Switzerland.
This has lead to close and long lasting engineering and development partnerships with customers that require high-quality precision medical products, traceable quality processes and reliable services. The Klingel medical metal group makes the most of its cutting-edge production technologies and long years of experience with products for all kind of medical applications to develop innovations and optimize existing techniques in collaboration with their customers.
We can establish your individual needs with our one stop shop as a modular or complete/fulll-service package offer
- Design to manufacture
- Metal laser sintering
- Machining (turning/milling/erosion/laser welding)
- Washing
- Surface finish (electropolishing, anodizing, coating, grinding)
- Laser engraving
- Assembly, 100% inspection,
- Cleaning and sterilizing (with partner)
- Labeling and pack aging
- Logistics
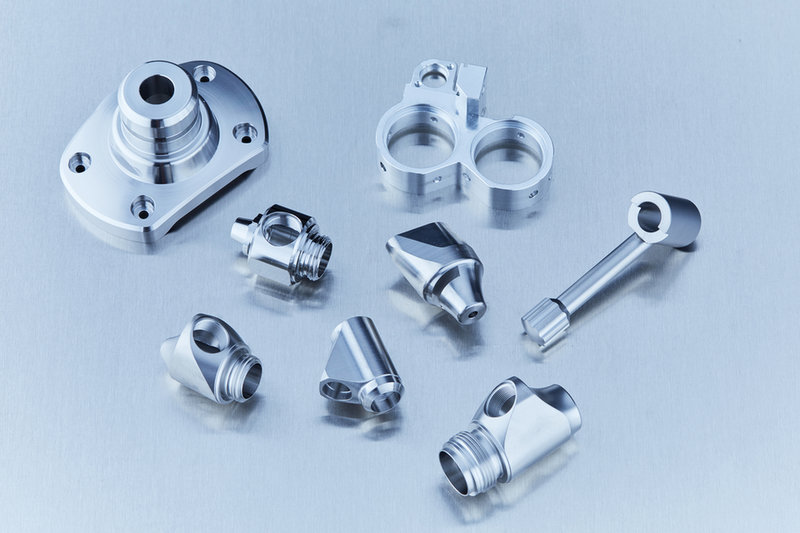
Your benefits while working with one of the leaders in metal processing are:
- Simplification of your supply chain through Klingel’s medical metal group one stop shop strategy
- Reduction of lead time through your product development cycle and faster time to market for your solution
- Reduction of quality audit workload for you as a customer
- Full service partner
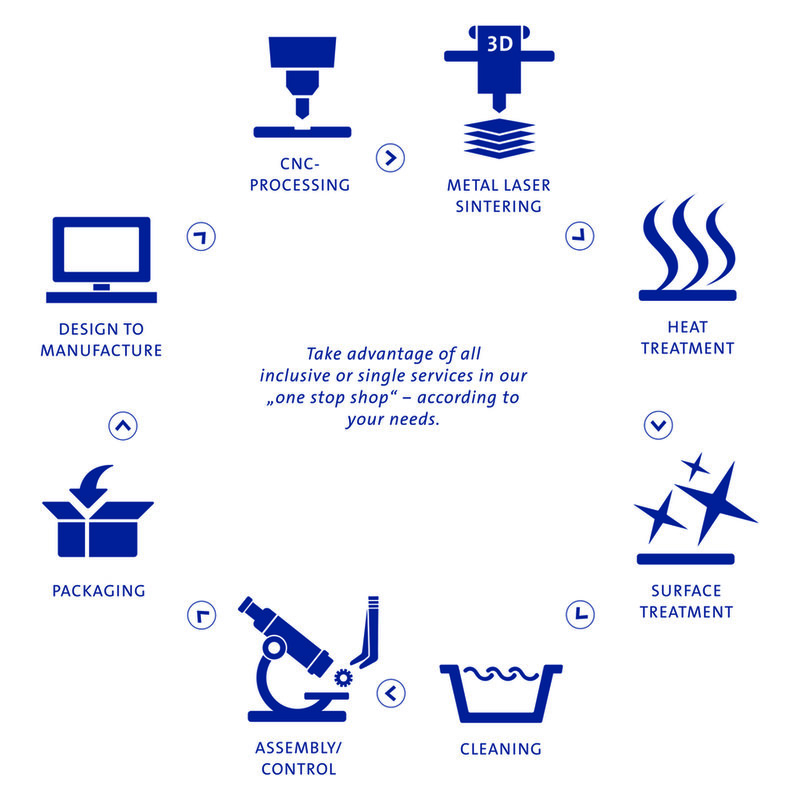
We guarantee highest quality certification standards coupled with extensive, in-house quality management expertise to meet increasing customer, audit and regulatory requirements. All Klingel medical metal group companies are accredited for all processes by ISO13485 certification, have an FDA registered site and are compliant with new Medical Device Regulation (MDR) 13485:2016. The Klingel medical metal group, with its outstanding know how and capabilities, is well positioned for upcoming regulatory changes as its size allows it to cope with increasing regulatory requirements.
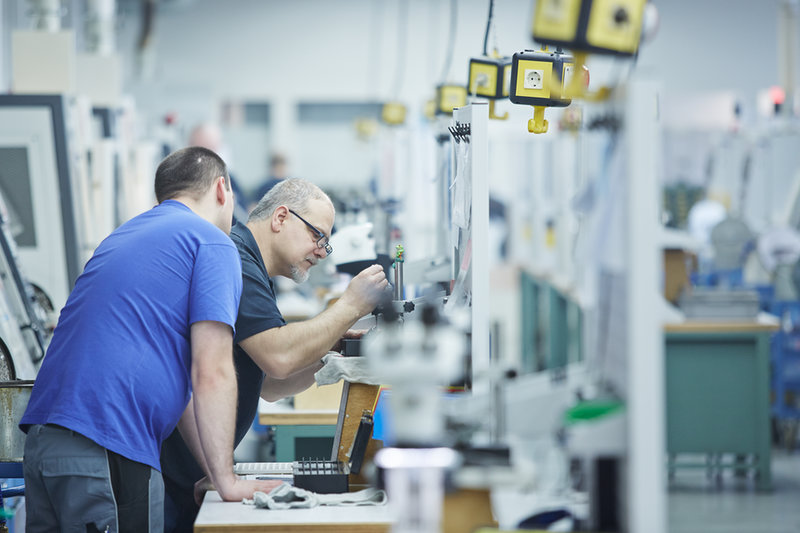