COMPANY
INSIGHT
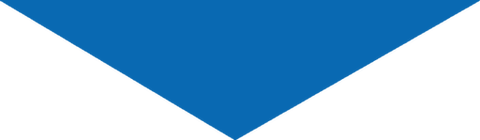
Autoclavable protection for electronics in medical technology
Electronics used in medical technology close to or inside the body must be particularly well protected. The devices are either single-use or are reprocessed before the next use. Reprocessing through e.g. cleaning and then sterilizing can save costs compared to disposable products.
The following are a few of the key medical applications where ElectroCraft motors empower medical motion control.
Reprocessable electronics are cleaned e.g. by washing in an alkaline solution followed by sterilisation in an autoclave. These processes place high demands on protection with regard to impermeability to liquids and steam as well as chemical and thermal resistance. Deposits or infiltrations of liquids can lead to short circuits and complete failure of the electronics. Especially interfaces of different materials are at risk due to the different coefficients of thermal expansion. The materials used, which are in direct physical contact, must also be biocompatible.
The protection methods used must be very reliable so that the electronics remain fully functional throughout their entire planned service life. Although a long-term effectiveness of the protection can be simulated in the laboratory under practical conditions, a high and constant quality of the protection process is essential to avoid subsequent failures during operation.
Autoclavable di
rect overmouldingDirect overmoulding is a reliably repeatable process for the protection of electronic assemblies. It complements the well-known potting, foaming, varnishing or coating processes that are also proposed by Turck duotec. Through direct overmoulding, the material is wrapped around the electronics as a homogeneous body.
A degree of protection of at least IP68 (corresponding to 1 week under 1 m of water) is achieved for cables and even for metallic pins in connectors.
Turck duotec has now developed an autoclavable direct overmoulding specifically for medical technology. Tests have shown that low pressure materials commonly used in overmoulding do not yield satisfactory performances. Therefore, Turck duotec also uses thermoplastic or thermosetting compounds in connection with the direct overmoulding of electronic assemblies.
The polymer is processed with standard injection moulding machines and can be processed under controlled conditions in a clean room environment. The injection parameters play an important role for successful overmoulding, but the moulds and layouts used are just as important. That’s why the entire process is done in-house, including material selection, simulation and layouting.
Miniaturized, comprehensive protection
During the reprocessing cycles in steam sterilization in autoclaves, the electronic assembly is exposed to very large temperature fluctuations of more than 130°C. Differences in the thermal expansion coefficients between the electronic assembly and the encapsulated plastic housing cause stresses in the solder joints and components. These can lead to breakage and functional failure of the module. A very stable behaviour of the electronic function can be guaranteed by material-selection and adjusting the expansion coefficients.
At the same time, the housing must effectively protect the electronic assembly from moisture, wetness and aggressive cleaning agents. This protection must be guaranteed over the entire life cycle. Suitable barrier values for water vapour and cleaning agents are necessary.
By means of infrared spectroscopy analysis of the housing material in new (not yet autoclaved) condition and after several autoclave cycles (Universal 134 B, up to 2500 autoclave cycles) it was determined that the wave maxima do not change in position and amplitude. The material must also be resistant to hydrolysis and all common cleaning agents and disinfectants. Material samples were immersed in various media for 21 days. Changes in mass were less than 0.3%.
These results show that the investigated material is very stable against hydrolysis and other ageing effects caused by the washing and autoclave cycles.
lnorganic extractables are detected and quantified by inductively coupled plasma - mass spectrometry (|CP-MS). Organic extractables are detected and quantified by gas chromatography combined with mass spectrometry (GC-MS). Both ICP-MS and GC-MS are suggested for inorganic and organic analysis in ISO 10993-18 and ASTM F2847.
The amounts of ions released from three medical devices during the 3-day extraction at 50°C are typically at least three orders of magnitude lower than the permitted parenteral daily doses. No organic substances were detected in the extraction solutions. Thus, the barrier effects, limiting ions from the body from entering into contact with the electronics and vice-versa, are sufficiently high for the targeted applications in medical devices up to class 2B.
In laboratory tests, complemented by test protocols at customer locations, different electronic assemblies could be autoclaved up to 2,500 times and continued to function.
Conclusion
The combination of precision, miniaturization by wall thicknesses of a few tenths of a millimetre and the shape that is matched to the assembly with the resulting weight savings make autoclavable direct overmoulding particularly suitable for applications in medical technology.
Typical applications include sensors and electronics used in e.g. surgical power tools, surgical robots and endoscopes. Differentiation to existing protection methods is a higher degree of miniaturization and less weight with respect to potting and higher mechanical protection and robustness with respect to coatings.