COMPANY
INSIGHT
In between medical device issues and coatings lay the foundations of Formacoat LLC, a contract manufacturer that specializes in commercial-production application of liquid applied coatings to our customers’ medical devices as a custom service. We don’t make or sell coatings, but we know and work with many different coating suppliers. Part of our service is to be able to parse the diverse field of coatings to help find the right coating for you and your medical device challenge.
Welcome to the world of Formacoat LLC, an ISO 13485 certified company.
Our customers range from individual doctors, to small start-ups, all the way to large international medical device firms. Our most common customers are small to mid-sized medical device firms.
The most common devices we coat are catheters, but the range, shape and uses of devices we coat are continually expanding.
The coatings we use include thermal and UV cure coatings. We are in the process of adding a covalent bonded chemical grafting hydrophilic coating that will have capabilities for smaller ID’s that other chemistries cannot do.
OUR CUSTOMERS RANGE FROM INDIVIDUAL DOCTORS ALL THE WAY TO LARGE INTERNATIONAL MEDICAL DEVICE FIRMs
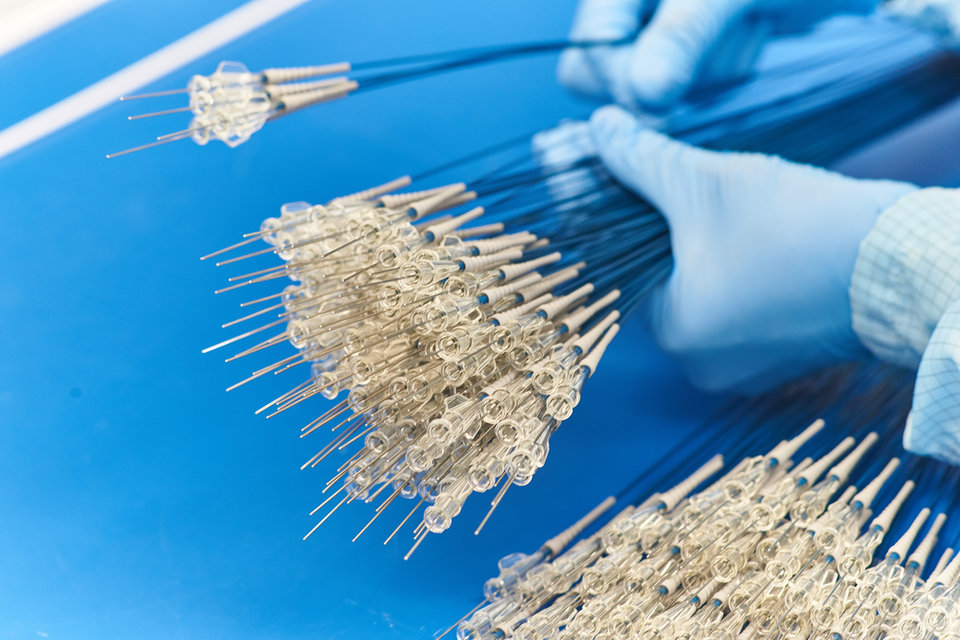
Our most common request is for devices to be coated with hydrophilic coatings as a way to reduce friction. Hydrophilic coatings require water to activate the lubricity, which in a typical surgical situation is very easy to do. In terms of friction, one may consider that Hydrophilic coatings are in general 1 order of magnitude less than typical Teflon® (or other types of fluorinated surfaces) and may be up to 2 orders of magnitude less friction than many common medical device materials. Formacoat has multiple vendors of hydrophilic coating technologies and chemistries. Our premise is that there are no bad coatings; it is just that one type of coating chemistry may work better for you than another. We use our knowledge and experience and testing to find the best coating for your needs. If you happen to be lucky (or skilled) enough in life to have, say, own both a Ferrari® and a pickup truck, would you use your Ferrari to go to the lumber yard to pick up plywood? Nope, though that does not mean that a Ferrari is a bad vehicle, just not the right vehicle for that transportation need. Coatings are like this. So when it occurs that a particular coating does not work, but, having already worked with your device, we can easily apply what we’ve learned in the first experiments to different types of coatings from other vendors. That means that the customer doesn’t need to teach someone about their device multiple times, as they might if they were going directly to coating vendors who are beholden to their own coatings and chemistries. This is fast and efficient for your time and project.
FORMACOAT HAS MULTIPLE VENDORS OF MEDICAL DEVICE COATING TECHOLOGIES AND CHEMISTRIES
We are also increasing the number and types of PTFE and other fluorinated coatings we offer, including several lower temperature types for some alternate needs.
Formacoat has the equipment, coatings, knowhow and expertise and, if we have not done it yet, wide experience and creativity to solve new coating challenges. We coat all manner of OD, ID’s, flat films, foils and mesh, and complex shapes with a wide array of biomedical materials. Newest developments: we are getting increasing interest and work in our range of non-thrombogenic coatings from different vendors, which include different heparin, silk, and phosphorylcholine coatings. New customer work is also ongoing in the realm to bioresorbable materials and drug containing coatings are further expanding our range of capabilities and services for the diverse medical device industry.
Formacoat has grown into an increasingly recognized player in the world’s market for medical-coating manufacturing services
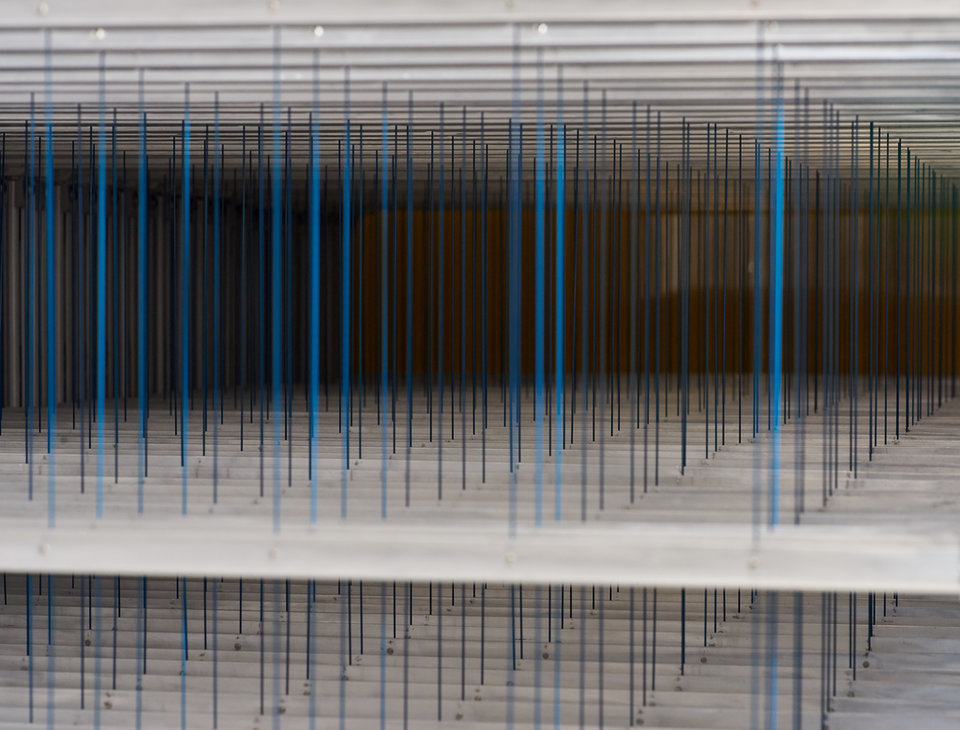
Since its foundation in 2002, the Formacoat has grown into an increasingly recognized player in the world’s market for medical-coating manufacturing services, offering a wide range of medical uses for existing hydrophilic, hydrophobic, non-thrombogenic and other speciality biomedical coatings and a range of different nano coatings and ultrahydrophilic and ultrahydrophobic coatings that with special testing may work for some different, non-lubricious needs.
Formacoat’s objective is to provide an effective one-stop shop for small to large-scale commercial coating applications for a range of uses, including in vascular, cardiovascular and implant delivery, as well as catheters, guide wires and roll-to-roll applications.
The increasing range of products coated and coatings means the firm is outgrowing its current facility and equipment. Its new facility will allow expanding in its core catheter processes four fold, including a new coating system that work well for both small volume R&D runs at less cost, and for some products, “unlimited” lot sizes (larger than its batching production lines can do); film / mesh coating by two fold; six fold increase in ISO Class 7 cleanroom; and space for other work by increasing by three times the square feet of its current facility.
The company has also begun to work on making a controlled timing, super swelling hydrophilic material for a specific customer need, by modifying an existing technology. By bringing other coating technologies in-house, we can find or work to adapt new technology types to unique needs. In the past year we worked to find ways to use a grafting technology on metals that were previously only working on some polymers.
Formacoat’s work in these kinds of areas is symbolic of a much larger commitment to innovation.