COMPANY
INSIGHT
Controlling Speed Can Be Crucial
Precise speed control is crucial for reliable results in a variety of medical processes. Knowing your speed is set and regulated, within a tolerance of +/- 0.1 RPM for extended periods of time, assures consistent results in a liquid mixing or pumping application.
Controlling Speed
The speed control loop on the drive consists of a circuit to monitor and control the motor’s torque using a speed command as the input target value. In this control loop process, the speed of the motor shaft is measured on a periodic time-base and compared to the input target value. Any difference between the two values is applied as a correction to the torque control that is needed to accelerate or decelerate the motor shaft back to the desired speed. The shaft speed stays constant, within a small tolerance, due to the quick reaction time of the correction applied to the torque control loop.

What Causes Speed Changes
External forces that can affect the shaft speed are a result of torque on the motor shaft due to friction, inertia, and variations in fluid viscosity.
Friction develops torque on a shaft in proportion to its speed.
- Inertia develops torque during changes in speed.
- Viscosity develops torque from an object mounted to the motor shaft as it moves through a fluid medium.
- An object’s shape and size, such as a propeller, moves through the medium acting as a moment arm developing torque.
- The amount of torque needed to keep a constant speed depends on the viscosity of fluid medium.
- Viscosity of a fluid can also vary as its temperature changes.
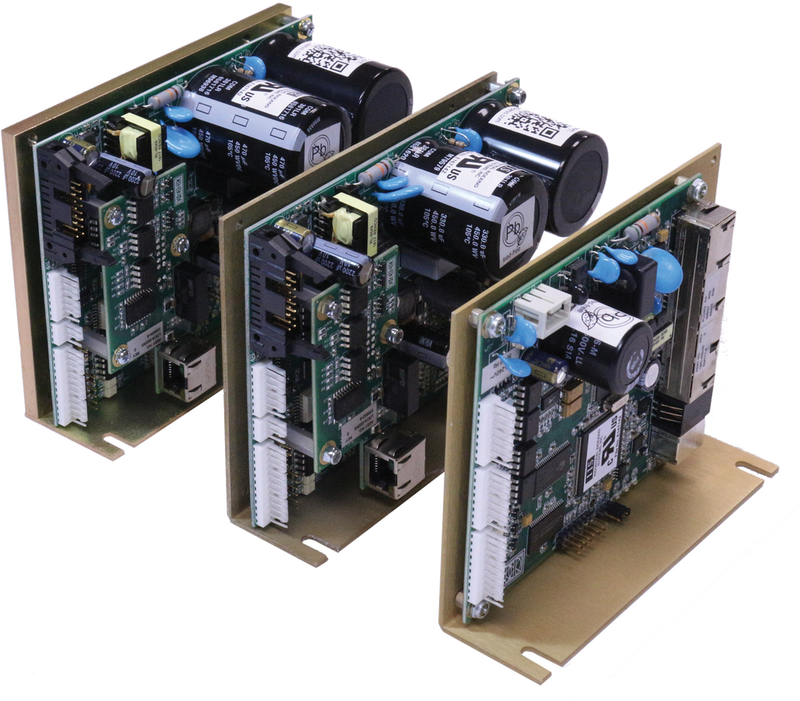
Best Motor Size
The size of the motor will depend on the volume of the medium, the viscosity at its lowest temperature and the speed the fluid required. If the need arises, customized motors that meet your specifications, are available on request.
System Overview
The IIS Luminary Digital Drive and motor combinations range from 50 watts to 3500 watts with speeds to 4000 RPM. Each drive is setup to provide the full capacity of the motor it is matched with, before shipment.
Using servo drive technology by Industrial Indexing Systems (IIS), the Luminary Servo Drive Series is easily configured for a variety of applications using the digital drive interface option. The digital drive interface option bypasses the normal analog circuit path to allow access to the digital registers which control the operation of the speed control loop. Using the universal Rs485 device bus with Modbus RTU as its connectivity scheme, the digital drive is reachable from a variety of HMI, PLC and PC type controllers. The Rs485 multi-drive configuration permits drive networks of up to 16 units.
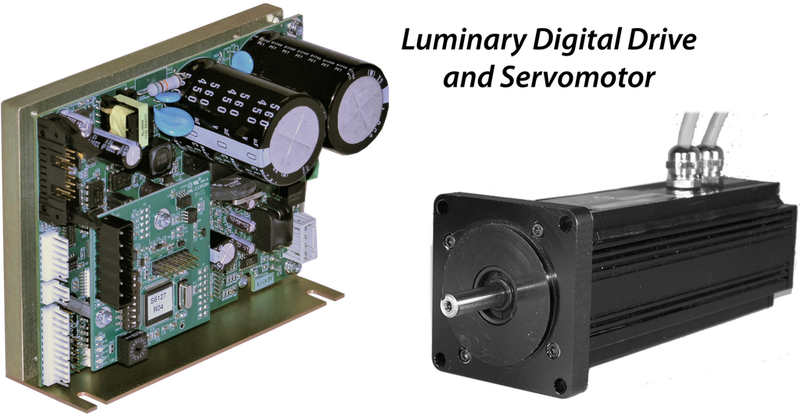
Results
Engineers at IIS are ready for requests to design features into the Luminary drive that reach beyond the standard features we offer. Modified acceleration profiles, variable speed selections, inputs and outputs with special sequencing are just a few of the possibilities without additional hardware costs. Functionality specific to handling your process can be built into the drive firmware. This results in a faster reaction time compared to handling it over the Rs485 network.
Electronic motion control is at the heart of the business activity at IIS and has been for over 40 years. Our focus continues to be dedication to what our customers require, delivering results and providing unparalleled support.