Robotics
Get a grip: designing mechanical controllers for robotic surgery
Scientists at Tokyo Institute of Technology have designed a new type of controller for the robotic arms used in certain kinds of laparoscopic surgery. By combining the two distinct types of gripping used in commercially available robotic systems to leverage the advantages of both, they believe their technology will reduce physical strain on surgeons while providing good precision. Chloe Kent finds out more.
R
obotic surgery has come a long way since Intuitive Surgical’s da Vinci system was first approved by the US Food and Drug Administration (FDA) in 2000. Using console-operated robotic arms for keyhole procedures, rather than tools directly handled by a surgeon, has drastically advanced the field. Surgeons no longer need to train for years on end to perform laparoscopic surgeries, but could pick up the necessary techniques in a matter of weeks.
Engineers at the Tokyo Institute of Technology have now created a new type of controller designed to operate these robotic arms, which could make things even easier for surgeons. The new controller combines the two major types of gripping used in the robotic systems currently on the market, and the developers believe this could be a significant improvement on existing systems.
“The benefit of the mechanism is to provide the user with both capability of precise motion input and less fatigue [in] operation,” says Tokyo Institute of Technology associate professor Kotaro Tadano, who helped lead the development of the new controller. “The user can input the motion precisely by moving the pinching fingers even though he/she grips the power grip handle, which helps to reduce the load to thumb.”
So, how exactly does this mechanism work, and what makes it potentially better than existing systems?
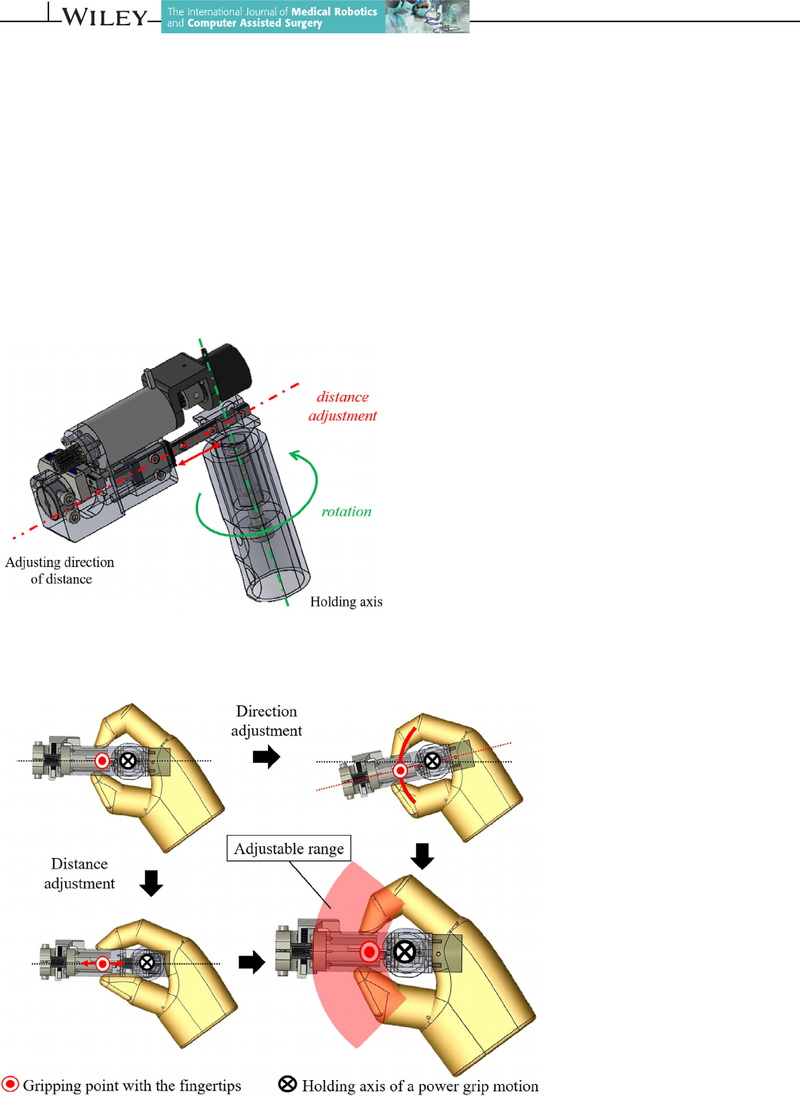
Pinch grip motion in the combined-grip-handle when the palm isfixed. Image: Kotaro Tadano
Pinch vs power vs control
Robotic surgery is known to be more physically comfortable for surgeons than laparoscopic surgery performed by handheld tools. Procedures are typically performed using a system with a master-slave configuration, in which the master controller device is manipulated by a surgeon to control a robotic arm. Using a system like da Vinci, or CMR Surgical’sVersius, a surgeon can sit or stand at a console as they see fit, rather than hunch over the patient, reducing strain on the back and shoulders.
These systems improve the dexterity and precision of surgeons by filtering out hand tremors and scaling hand motions into small movements. However, finger fatigue can still be common, with a surgeon’s grip on the master controller leading to eventual discomfort in the hand. This can impact the overall performance of their procedures.
Two types of grip are used to control surgical robots – the pinch grip and the power grip. The pinch grip involves using the thumb, middle and index fingers to achieve precise movements. Meanwhile, the power grip involves grabbing a handle with the entire hand and is used for more forceful work and larger movements. It’s pinch gripping which can lead to muscle fatigue in the hands, but a power grip alone won’t offer the precise control needed to perform high-precision surgeries.
The controller designed by the Japanese engineers is a modular master controller that can be adjusted to employ pinch, power and combined gripping.
Tadano says: “The developed mechanism consists of a motion input part and a power grip handle. The user pinches the input part with the forefinger and the thumb, and grips the power grip handle with the rest of the fingers and the palm. The point of the developed controller is that it allows the users to move the position of their pinching fingers against the power grip handle.”
What’s the point?
The system was tested through a pointing experiment. The 15 participants involved had to use a robotic arm to bring the tip of a needle into target holes as quickly as possible, without touching any obstacles.
Different conditions were tested for each variable, switching between numerous arm and palm rests, handles, gripping types and pinch grip motions. Overall, a combined grip yielded better performance in the pointing experiment on various fronts, including the number of failures to bring the needle into the target hole without touching other obstacles, time required to complete the task and overall length of movements performed to reach the targets.
Participants also reported that they preferred the combined gripping method over power or pinch grips alone, due to the ease and comfort involved. The results of the study have since been published in The International Journal of Medical Robotics and Computer Assisted Surgery.
Tadano says: “The mechanism has originally been developed to apply into a robot system for microsurgery with a magnified view of a microscope. But we consider the developed mechanism is also effective for other general endoscopic surgical robot systems.”
The research team is now working on improving the operability of the new controller. If further effectiveness can be confirmed in later testing, the control grip may be used in a product being developed by Tokyo Institute of Technology spinout Riverfield, which launched in 2014 to commercialise the university’s research outcomes.