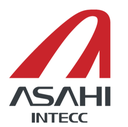
Medical Components
CONTACT US
Office address:
Asahi Intecc Europe B.V.
Strawinskylaan 527
1077XX Amsterdam
The Netherlands
Asahi Intecc Flexible, Torqueable shaft components for minimally invasive devices
A typical issue seen in catheter- or shaft-based minimally invasive device design is that improving the mechanical properties in one area results in a deterioration of mechanical properties in another area.
For example, increasing the bending flexibility of the device shaft may be required to traverse a particularly tortuous anatomy. It may be required to prevent plastic deformation from occurring when the device needs to get around an acutely angled segment. Doing so however can also results in a marked loss of torque transmission—angulation at the proximal end of the shaft will not be transmitted to the distal end, but rather the distal end will stall, ‘jump’ or even buckle and kink. Adjustments in the shaft’s bending flexibility can also lead to an increase in the shaft’s longitudinal flexibility, negatively affecting elongation or compression resistance, potentially making control of the shaft or device delivery extremely difficult.
Asahi Intecc Co., Ltd. is an ISO13485- and ISO9001-certified Japanese medical device components manufacturer that has specialized itself in solving these types of trade-offs.
Asahi Intecc Core Technologies
Asahi Intecc Co., Ltd. is an ISO13485- and ISO9001-certified Japanese medical device manufacturer.
We are specialized in custom-made flexible ultra-fine wire ropes and tubing with high torsional rigidity, such as the single layer ACT-ONE cable tube and the multi-layer Torque Coil. We also offer in-house coating and parts laser-weld or crimp assembly services to our micro rope and tube components.
Drawing from our vast experience in the medical device field (e.g. vascular, structural heart, endoscopic, minimally invasive and other devices), our in-house wiredrawing, wire-forming, coating, torque and assembly technologies provide a broad range of options for your device. Asahi Intecc’s four core technologies form the foundation of our original materials processing technologies.
Over more than a 40-year span, these technologies were developed by us while responding to the sophisticated requirements of our clients, combining them to create many custom high-performance medical components.
Inner tubing assembly
The ‘inner tube’ is a custom-made two-layer extruded tube designed to act as an inner liner for Asahi Intecc’s cable tubes. The lower layer is a fluoropolymer—e.g PTFE, PFA, FEP, ETFE—to provide decreased friction, sealing or chemical isolation in the inner lumen, while the upper layer is from PEBAX to facilitate proper adhesion to the stainless steel-based cable tube it is assembled in. The inner tube’s minimum wall thickness is 0.03 mm, although in the end this depends on the actual size of the cable tube’s inner diameter.
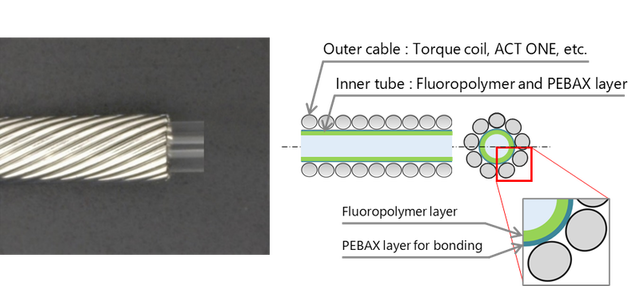
Cable tube/Torque Coil
A ‘cable tube’ is a stainless steel or nitinol shaft or catheter structure that can allow for a combination of adequate bending flexibility, torque transmission and elongation resistance. It is very similar to a rope or strand as it is also formed by helically twisting wires over a core wire, but with the core wire removed to create a lumen inside said structure.
As the cable tube’s constituent wires are helically twisted, angulation of the cable tube in its twist direction will result into its separate wires pressing onto each other, consequently resulting in a high degree of torque transmission. The actual length of the cable tube’s separate wires can be customized by changing the amount of wires the cable tube consists of.
Doing so directly affects the maximum torque, the bending flexibility and the elongation resistance. This makes the cable tube a highly customizable shaft component, where the best balance for the application can be found. The more flexible variant with two or three layers instead of one is often called a ‘torque coil’.
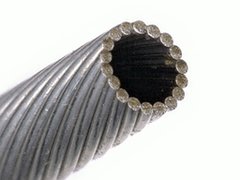
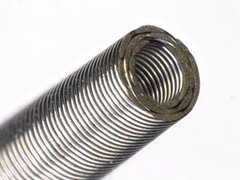
Outer coating
It is possible to coat our cables, cable tubes and coils inhouse by way of spraying (PTFE), dipping (PTFE), extrusion (PE, PA, PEBAX, TPU, different fluoropolymers besides PTFE) or heat shrink(PTFE and other fluoropolymers, PEBAX). The coating material is defined based on requirements for lubricity, sealing, electrical insulation, and others. Minimum wall thickness is 7 micrometre for spraying, 20 micrometre for extrusion, and 30 – 50 micrometre for heat shrinks pending material, application and component size.
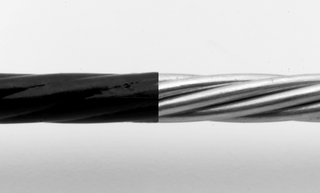
Laser weld assembly
It is possible to combine different mechanical properties (e.g. different bending flexibility) into one shaft by laser welding discrete components of our cable, coil and rigid tube/hypotube-based components. As an additional service we offer laser weld assembly of screw threads, drivers and other bespoke components to our cable and coil-based products inhouse.
It is possible to supply Asahi Intecc the components that need to be assembled, or we can source the components from our own suppliers. An important condition is that the supplied component is compatible with stainless steel (mainly 304 or 316).
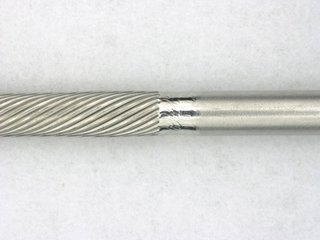
Torque hypotube
The Torque hypotube incorporates two of Asahi Intecc’s core technologies – wire drawing and torque transmission augmentation. Ideal for minimally invasive medical devices that require excellent stretch and compression resistance, kink resistance, shape recovery, and remarkable 1:1 torque characteristics.
Typical applications are endoscopic fine-needle aspiration (FNA) and other minimally invasive devices used in diagnostic and therapeutic interventions. It is also often combined with our other, more flexible cable and tube components for improved proximal pushability and maximum torque.
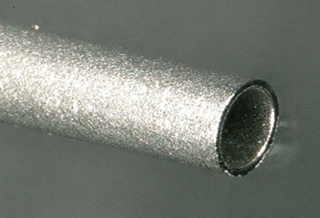