TECHNICAL SPECIFICATIONS OF MICRO-EROSION
Surface roughness up to Ra 0.05 / N2 when eroding
Achievable tolerances of up to +/- 0.001mm when eroding
Radii up to min. 0.02mm
eroding of small, precise holes
eroding bores in preparation for wire erosion
Processing of special materials such as ceramics or hard metals.
Other workable materials: hardened steels, steel, etc. alloyed steels, stainless steels (INOX), non-ferrous metals
Machining in an oil bath especially for hard metals, ceramics and materials susceptible to corrosion
Manufacture of micro clamping devices to fix micro parts for processing
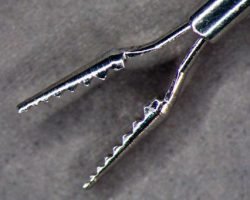
MICRO-EROSION
In the area of micro-erosion, parts with the smallest wire diameters of 0.02 - 0.10mm, as well as micro-bores with the smallest hard metal electrodes from 0.10mm and larger are eroded.
START HOLE ERODING / STARTING HOLE SHOOTING
Maximum travel distances: X = 300, Y = 200, Z = 300mm
Minimum starting hole diameter: 0.10mm / 0.15mm
Possible starting hole diameter: 0.10mm - 3.00mm in 0.10mm steps
Existing collets:
0.10mm-1.00mm
2.00mm-3.00mm
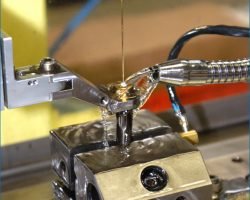
Starting hole bores serve on the one hand as preparation for the fine wire or wire EDM work and on the other hand precision bores in the smallest area can be made with a minimum starting hole diameter of only 0.10mm.
Holes can be made in hardened materials, hard metal and other electrically conductive materials.
PRECISION LASER CUTTING
4-axis precision laser cutting
Our precision laser system significantly increases productivity in the areas of sheet thicknesses from 0.02mm to 3mm
Surface quality up to Ra 0.80 / N6 can be achieved
Tube processing up to Ø 80mm is possible thanks to the controlled 4-axes
Processable materials: titanium, stainless steels, steel and alloy steels, non-ferrous metals, various plastics
Material thickness: 0.02mm foils up to 3.00mm sheets
Dimensional and form accuracies of +/- 0.01mm to +/- 0.02mm for sheet thicknesses up to 1.5mm
up to 3.0mm sheet thickness = +/- 0.03mm
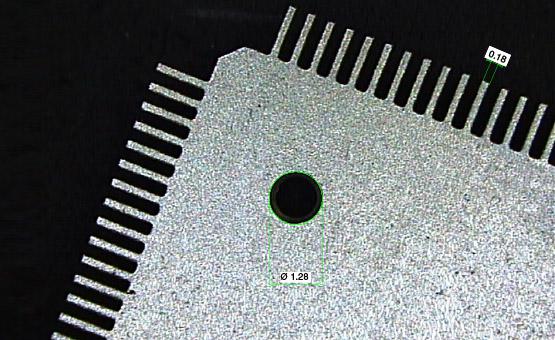
DIE SINKING
Surface roughness up to Ra 0.08
High level of detail of required shapes
Exceptional surface quality
Smallest corner radii even with deep depressions of less than 0.02mm
Processing of special materials such as ceramics or hard metals.
Other workable materials such as hardened steels, steel u. alloyed steels, stainless steels (INOX), non-ferrous metals
3DS surfaces offer the following advantages:
In terms of appearance and quality = adjustable degree of gloss of the plastic part and improvement of the anti-scratch characteristics
Special advantages are shown by the reduced adhesion of the plastic part in the injection mold, thus enabling increased demolding speeds.
Less residue accumulation in the injection mold = reduction of the cleaning and maintenance times and costs of the injection molds and thus longer spraying autonomy
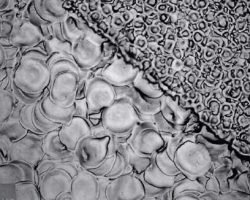
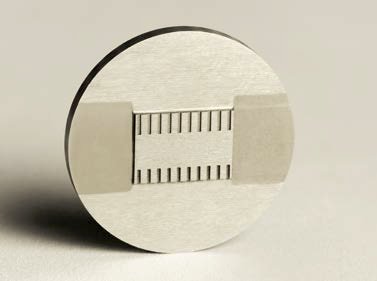
With our new high-precision die sinking EDM machine for the micro range, we are able to erode the smallest, fine cavities, slots and contours of all kinds. The big advantage over conventional die-sinking EDM processes is that we can achieve the smallest corner radii of less than 0.02mm with a smaller number of electrodes. This enables us to reduce production costs and are therefore more productive.
The extremely high repeatability provides the perfect machining accuracy that is required. Due to the exceptional surface quality and the highest level of detail, even when using microelectrodes, parts with the highest demands can be eroded. By producing 3DS surfaces, an improvement in the anti-scratch characteristics of the plastic parts to be injected can be achieved, an adjustable degree of gloss of the finished plastic part. Furthermore, the 3DS surface process offers a reduction in the adhesion of the plastic part during the injection process in the tool and thus an increase in the demolding speed during injection. Due to the reduced adhesion behavior, the accumulation of residue in the mold during the spraying process can also be reduced, which reduces maintenance times and costs and increases productivity.
EDM GRINDING
High profile accuracy in the µm range
High concentricity (0.002mm)
Filigree contours can be realized
Deep, fine grooves on round parts with slot widths in the centimeter range can be produced
Finest inner radii for grooves on round parts of r = 0.05mm
Surface qualities of Ra 0.1
Different surfaces / wrench sizes at different angles can be set and eroded
No breakout of the binding matrix components when dressing profile grinding wheels
Processing of special materials such as ceramics or hard metals.
Machining or dressing of CBN or diamond grinding wheels (the binding material and the carrier must be electrically conductive)
Other workable materials such as hardened steels, steel and alloy steels, stainless steels (INOX), non-ferrous metals.
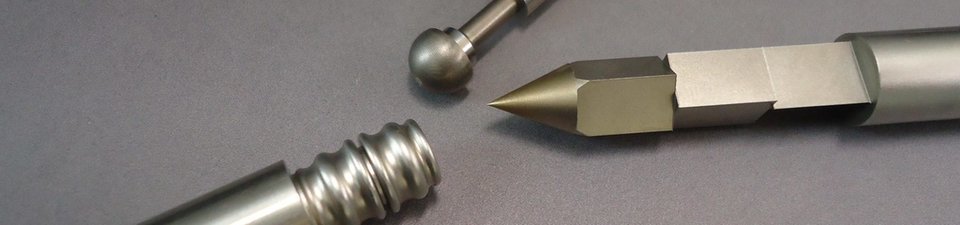
With our new rotation axis, a wide variety of shapes, the finest grooves, filigree profiles and small radii or surfaces on round parts can be made contactless, i.e. without any force being applied to the workpiece. The axis of rotation is always used when deep, fine grooves or small corner radii on round parts can no longer be produced by turning or cylindrical grinding.
The axis of rotation offers great advantages, especially in the area of grinding wheel dressing, in that required profiles with fine inner radii of, for example, r = 0.05mm can be created. With this process, profile accuracy in the µm range can be achieved with high concentricity. The prerequisite for this is always that the workpiece to be processed is electrically conductive. Another advantage of EDM grinding is that there is no heat input into the workpiece during the work process, which means that there are no structural changes in the material, such as those that can occur during turning or cylindrical grinding, for example.
KEEP IN TOUCH
You are welcome to call us, reach us via live chat or write us an email. We are happy to hear from them!
Stadtweg 24
Postfach 34
CH-8245 Feuerthalen
Tel: +41 52 659 59 52
Fax: +41 52 659 59 52
Mo – Fr: 07:00-17:30