3D printing as an integrated technology
Metal Additive Manufacturing (AM)—also known as metal AM or 3D metal printing—is becoming a driving force in the production of many medical devices. In fact, orthopedic implants with porous surfaces and lattice structures mimicking the behavior of normal bone have led to significant improvements in patient outcomes—and implants with these features cannot be made without AM.
Moreover, it is not just implants that have new designs; surgical tools and instruments also benefit from simplified manufacturing processes, weight savings and ergonomic features that can only be made with AM. Not surprisingly, it is estimated that as much as 10% of all orthopedic implants being introduced have at least one component made by AM.
However, starting a new department for AM carries many challenges. As metal AM grows in importance, original equipment manufacturers (OEMs) and contract manufacturing organizations (CMOs) of all sizes are investigating how to best integrate this technology in order to better meet their customers’ needs.
With a complete "end-to-end" solution that brings customers best-in-class quality together with lowest running costs, GF Machining Solutions and 3D Systems recently launched the DMP Flex 350 help ensure success when adopting this new technology.
The technology
Achieve distinct competitive advantages with Laser-based 3D printing
There are various technologies for printing metals, but the dominant approach today creates solid material through the targeted melting of very fine metal powder. DMP Factory and Flex systems from GF Machining Solutions and 3D Systems use a laser-based process (selective laser melting) which can produce high-quality surface finishes and small features (down to 0.1 mm).
A key consideration when investigating metal AM technologies is the range of materials the respective systems can print, as well as the ability to change—or not change—materials if necessary. For example, surgical instruments are most often made of stainless steel, while surgical implants usually require titanium. If your target is to fully load your printer with different types of jobs, a flexible system allowing efficient material changes will be your natural choice. The DMP Flex 350 has been engineered to allow a user to change the metal being printed in only a few hours. On the other hand, the DMP Factory series is designed for use with only a single metal. With the DMP Factory and a DMP Flex versions of the system, manufacturers can invest in the technology that is right for their operating environment.
Innovation
Only our DMP build chamber permits mastery of the metal 3D printing environment
When it comes to 3D metal printing, oxygen is the enemy. When metals such as titanium are in its presence, they degrade through oxygen uptake. Our system’s unique design makes use of a sealed build chamber to create the optimal printing environment by evacuating all air from the chamber and replacing it with argon. This cycle is repeated three times before the build begins, removing both oxygen and any trace of humidity from both the chamber and the powder reservoir.
With this unique approach, the oxygen level present during operations is around 25 ppm, compared to 300 to 700 ppm of oxygen in other systems’ build chambers (which most often have a continuous flow of argon entering the chamber). The results with our system are better and more consistent product quality—build after build—and lower operating costs through both reduced argon consumption and a longer useful life for the metal powder.
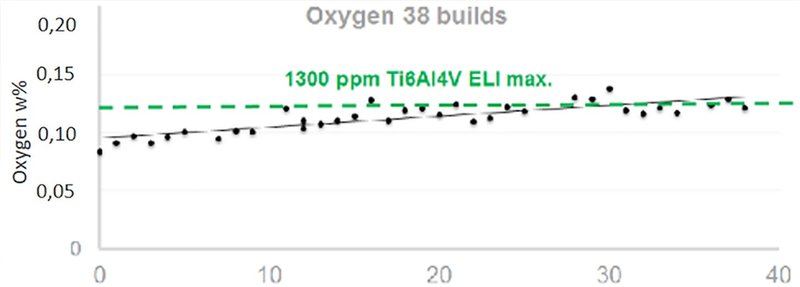
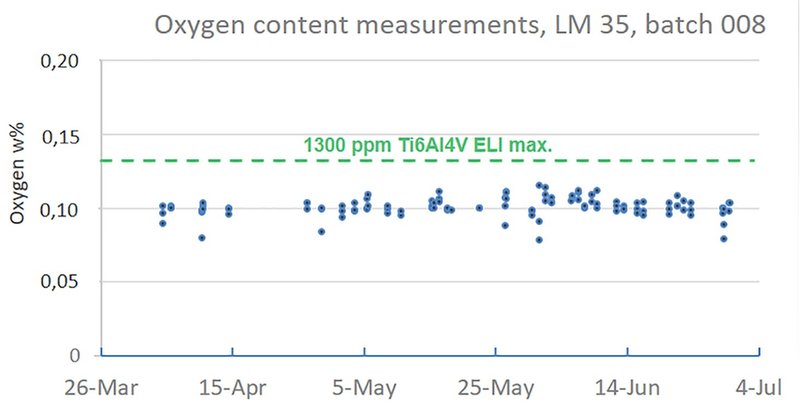
Traditional printer : Oxygen degrades the material, which must be scrapped after about 30 build cycles
DMP Flex 350 : Material quality stays stable, even after dozens of build cycles
A complete solution
Achieve high quality and reduced costs with a solution covering the complete process, from design to finished part
Even with its many advantages, the DMP Flex 350 is just one part of the metal AM printing puzzle. Success also requires a product design adapted for 3D printing, a validated process, and the ability to integrate downstream operations. GF Machining Solutions and 3D Systems provide a full range of technologies, including both machines and Automation for downstream processing. One of the keys to our approach is the use of System 3R pallets as a base within the DMP Flex 350.
Printed products can be transferred to secondary processing (such as milling) without the need for re-clamping or re-referencing, and with product manufacturing data secured via System 3R's radio frequency identification (RFID) chip. GF Machining Solutions and 3D Systems have also introduced a wire-cutting Electrical Discharge Machining (EDM) system designed specifically for AM: The AgieCharmilles CUT AM 500 is unique in that it allows removal of product from the build plate cleanly and without cutting forces.
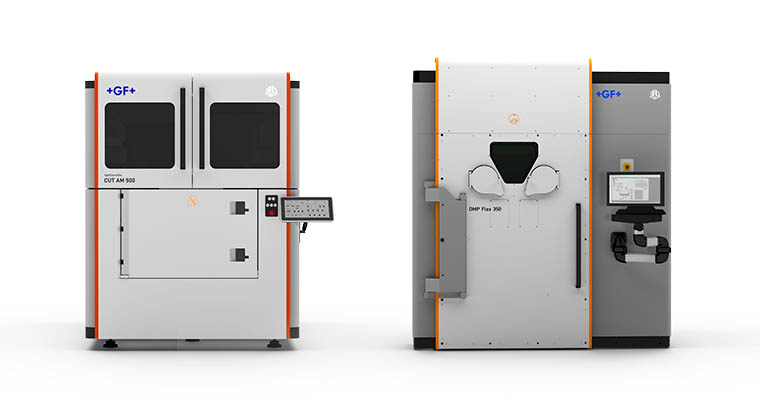
All-in-one parametric software solution
Taking a product from idea to design to print requires both experience and the appropriate software. Three-dimensional printing is a vertical process: The powder present in the bed cannot support the weight of the printed metal, so designs must be adapted to include support structures which can also prevent deformation due to thermal stress arising during the melting process. Build simulation software allows for the verification of the size and geometry of support structures; at the same time, training and design experience are valuable assets.
Our 3DXpert® software offers simulation tools that consider wall thicknesses, weight and powder behavior to ensure that supports are minimized but still of sufficient size and strength to do their job.
As an advanced software package, 3DXpert® also links the printer design, its Laser, and its powder characteristics. The result is a printing process that optimizes the Laser path and build strategy to ensure that the desired mechanical properties of the product can be achieved.
3DXpert® is the key to both product design and defining the optimal printing strategy; it is a complete solution from CAD to finished product and is adapted specifically to optimize manufacturing.
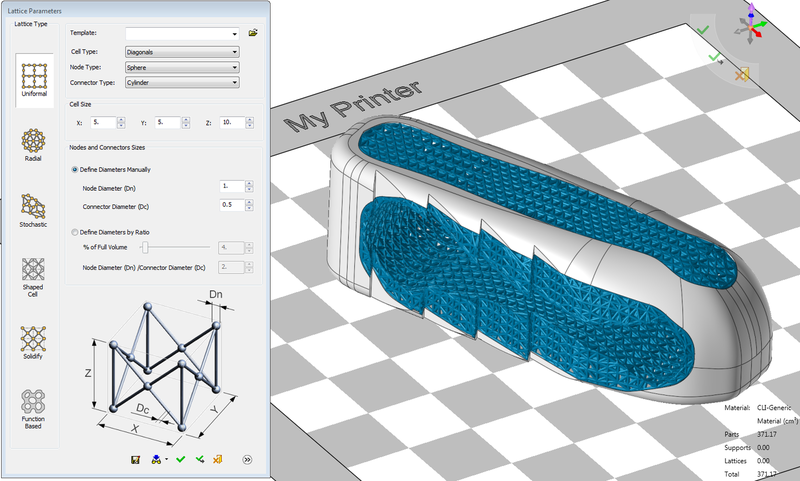
Qualification and validation
Overcome these hurdles with expert partners who understand your goals and your needs
In highly regulated, risk-averse sectors like medical device manufacturing, qualification and validation can represent big hurdles for a manufacturer. A validated AM process includes the entire ecosystem, from quality control processes for incoming powder to software, post-processing, and process controls on finished products.
Companies looking to bring AM into their production portfolio should carefully consider working with a partner—such as GF Machining Solutions and 3D Systems—that has the necessary level of experience and expertise to support an AM project through validation. As experts in metal AM as well as a broad range of other manufacturing technologies and with expert customer training and a continuum of Customer Services, GF Machining Solutions and 3D Systems are uniquely qualified to help manufacturers integrate AM into a factory and master every step, from machine installation to manufacturing of AM devices—with no surprises.
Bringing it all together
Master the many facets of 3D printing technology
The products you plan to make will inform your choice of printing technology and the make and model of your printer will increase—or limit—your flexibility in terms of materials and the products that can be made with those materials. The technology you use and the printer design you select will also drive your running costs—up or down—and influence the quality of the products you make. In the final analysis, oxygen management in the system you choose will likely be the single biggest driver of both your running costs and your product quality, and it should be high on list of priorities when you are deciding which system to purchase.
Managing the changes metal AM brings to product design and understanding validation of the complete value chain—including post-processing steps—are also key. Training your staff or hiring people with relevant experience and adapting your internal processes are also important starting points. As 3D printing continues to cement its place in medical device manufacturing, GF Machining Solutions and 3D Systems bring together the elements essential to your streamlined integration of the technology while delivering not only the system with the lowest running costs but an end-to-end solution that includes powder, software, expert application support, operator training, and Customer Services.