Cover Story
Managing the medtech supply chain – what to expect in 2024
After a difficult few years of turbulent supply-chain dynamics, will the industry rebound in 2024? We examine trends and challenges for the medtech supply chain. By Sally Turner.
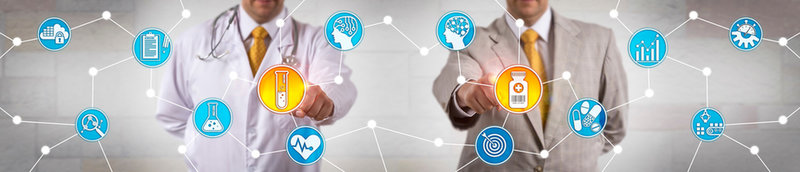
Credit: Shutterstock/LeoWolfert
Over the past 12 months, concerns about the impact of GLP-1 drugs, rising interest rates, and supply-chain issues have been at the forefront of medtech. Although inflation rates did come down, there are still lingering concerns about recession and labour shortages. Additionally, although the most significant impact of the COVID-19 pandemic was in 2020, we are only now seeing markets return to pre-pandemic levels.
However, industry players are cautiously optimistic, says April Chan-Tsui, a director on the Medtech Insights team at Clarivate, which provides data and insights for over 80 medical device markets globally.
“As 2023 progressed, many major medtech companies were seeing improvements in terms of the prior impact of supply chain disruptions,” she reports. “Examples include Stryker and GE Healthcare.”
Those improvements should likely continue going into 2024. However, companies are still strategically investing in supply chain improvements and other operational efficiencies to minimise impact for the future.
“Medtronic, for instance, recently announced its plan to reduce its number of suppliers (~200 suppliers) in efforts to improve its profitability,” she adds.
Supply-chain challenges
Supply chain challenges in the industry can be traced back to a lack of resiliency. Many supply chain organisations in their current state are unable to respond quickly to external pressures such as labour shortages, environmental disasters, geo-political issues, pandemics, or other factors.
“This stems from a longstanding trend of ‘lean’ management at every stage of the supply chain throughout the industry,” observes Brittni Straseske, a lead healthcare research and data analyst at Clarivate Healthcare Business Insights, specialising in the healthcare supply chain. “The COVID-19 pandemic shone a glaring light on this lack of resiliency and I believe, as pandemic-related pressures subside, we will see supply chain organisations rethink the lean approach and begin building elements of redundancy and diversification—for example, alternative suppliers of raw materials—back into their operations.”
Trends for 2024
In January, the UK NHS Supply Chain issued a £500 million contract notice for a Dynamic Purchasing System (DPS) Agreement to help bring medtech products to market.
“The overarching goals behind the creation of a DPS seem to align with what we’re seeing in supply chain trends in general,” comments Chan-Tsui. “Increased supply chain flexibility and expediting market access for medical technologies, with the ultimate goal of getting the best technologies to providers and patients.”
For example, although not directly related to supply chain management, the Clarivate team has seen regulatory changes elsewhere that have resulted in significant, impactful, technologies successfully brought to market faster than in the past. It makes sense that efficiencies also need to be made in terms of supplying and procuring of these technologies once approved. Chan-Tsui cites two examples in the US and China:
“The US Food and Drugs Administration (FDA) has its breakthrough devices programme, which is designed to expedite the approval process for innovative diagnosis or treatment devices based on specific eligibility criteria,” she explains.
This includes technologies for which no other alternatives exist, that clearly demonstrate benefits over existing alternatives, or that have the potential to significantly improve patient quality-of-life or other major advantages.
“China’s National Medical Products Administration (NMPA) has also implemented the Green Pathway to expedite medical device approvals in unique cases, with three fast-track paths— innovative medical device pathway, priority evaluation approval, and emergency use approval—that have criteria similar to the FDA’s breakthrough designation,” she adds.
What makes a ‘smart’ supply chain
Demand analysis and geographical diversification
Unlike in other industries, medtech supply chain processes – such as demand analysis – have traditionally been less digital/automated, making them vulnerable to sudden changes in demand or disruptions to global trade. During the pandemic, it was clear that healthcare systems and manufacturers were inadequately prepared for the magnitude and duration of the supply chain disruptions and shortages. Since then, many medtech manufacturers have reduced their supply chain risk through geographical diversification, decreasing their dependency on suppliers in specific countries/regions.
“For example, in the past, many medtech companies’ overreliance on single countries (typically China) or individual suppliers put them at significant risk for supply chain disruptions when a major event occurred,” says Chan-Tsui. “This doesn’t necessarily mean increasing the number of suppliers, but investing in suppliers more strategically, as evidenced by Medtronic’s recently announced push to reduce its volume of suppliers and greater focus on partnering with key strategic suppliers.
Straseske adds that we have seen a similar approach on the provider side by supply chain departments at hospitals and across health systems.
“For years, there was a concerted effort at provider organisations to reduce variation, or ‘standardise’ products and vendors as a cost-savings measure,” she says. “That inserted a lot of potential risk into the supply chain. Since the widespread shortages seen at the onset of the pandemic, providers have focused on identifying which products are most at risk for disruption and building out lists of secondary suppliers or alternative products that can be procured if the preferred choice is unavailable for any reason.”
Supply chain management technologies and resource sharing
For major healthcare providers, the implementation of supply chain management technologies, such as enterprise resource planning (ERP) and material management systems, is allowing for more effective inventory management. Contingency plans for resource sharing among healthcare facilities are also in place in the event of future global disasters.
Analysts have noted a collaborative effort between manufacturers/suppliers, healthcare providers, and other industry players like group purchasing organisations to address the lack of visibility and transparency throughout the end-to-end chain.
“For instance, during the pandemic two GPOs, Premier and Intalere (since acquired by Vizient GPO), were able to work with manufacturers to provide product availability and shortage information to hospitals in real time,” observes Straseske. “Historically, there has been very little by way of information sharing in this vein. Moving forward, true resiliency will require similar data and information sharing between all vested parties.”
AI, additive manufacturing, 3-D printing
AI is transforming supply chains by helping suppliers more accurately forecast demand and reliably source products.
“While inventory management was often periodic, the use of AI tools makes it possible to do so on a real-time basis because inventory management is simplified and more efficient,” says Chan-Tsui, “especially because it eliminates some of the aspects of the process that are more manual or prone to human error.
She points out that AI tools can also be used to analyse large volumes of purchasing and procurement data to understand trends and tie them to objectives (like spend against budget) and to accurately forecast demand and requirements for future purchasing and procurement.
Additive manufacturing and 3-D printing are also likely to play a key role in supply chain improvements. Although there will always be a need to produce certain devices in high volumes, there will also be demand for the cost-effective production of small batches of parts for more customised solutions.
The speed of production offered by 3D-printing mean that parts can be made-to-order, observes Chan-Tsui, with reasonable turnaround time, and it also reduces the need for costly storage of inventory. As was seen during the pandemic, 3-D printing offered the flexibility to produce some devices or components in-house.
Crucial investments
The question is, are medtech companies and their funding stakeholders willing to make the investments necessary to build the necessary resilience into supply chains, when short-term returns on investment are still key?
Chan Tsui believes companies are recognising the need to invest in the supply chain, which is a critical component of their overall business.
“For example, Medtronic had noted a significant impact from supply chain disruptions in 2022, an area the company continues to invest in strategically to improve profitability and set the organisation up for success going forward,” she explains.
However, it will definitely be an exercise of cost-benefit analysis for companies when implementing supply chain improvements.
“For example,” she continues, “while in-house manufacturing or nearshoring of manufacturing are potential solutions to minimise the risk of potential supply chain disruptions (such as significant global events, changes global trade policies, currency fluctuations, etc.) the level of restructuring required can be complicated and costly, and the ROI may not be immediate.”
So it is likely that the level of investment and the improvements implemented – whether it be small changes vs. a major overhaul – will certainly differ by organisation.
Future outlook
Undoubtedly, a more resilient supply chain is required, end-to-end, to ensure the industry is better prepared to handle future widespread disruptions.
“This means more transparency into product availability and potential shortages,” observes Straseske, “and diversification and redundancy throughout the supply chain from raw materials to vendors; a collaborative, data-driven approach to inventory optimisation and demand planning, and a more even assumption of risk via risk-sharing agreements/contracts between hospitals and their business partners.”
In the US, President Biden has announced 30 initiatives aimed at strengthening supply chains that are critical to the US economy and national security, in efforts to address the impact of supply chain disruptions and inflation.
“The CEO of AdvaMed, one of the largest medtech trade associations, called on the Biden Administration to ensure the medtech perspective is considered as part of that plan,” says Chan-Tsui, “such prioritising medtech needs in the CHIPS Incentives Program—specifically, ensuring that critical components are available for medical technologies—and further expansion of supply chain diversification.”
This is a specific US example, but it points toward the growing recognition that a resilient supply chain is crucial to the global medtech industry.

Caption: The US Pentagon is seeking to reduce carbon emissions through a range of programmes, but will it go far enough? Credit: US DoD
Australia could be one of the main beneficiaries of this dramatic increase in demand, where private companies and local governments alike are eager to expand the country’s nascent rare earths production. In 2021, Australia produced the fourth-most rare earths in the world. It’s total annual production of 19,958 tonnes remains significantly less than the mammoth 152,407 tonnes produced by China, but a dramatic improvement over the 1,995 tonnes produced domestically in 2011.
The dominance of China in the rare earths space has also encouraged other countries, notably the US, to look further afield for rare earth deposits to diversify their supply of the increasingly vital minerals. With the US eager to ringfence rare earth production within its allies as part of the Inflation Reduction Act, including potentially allowing the Department of Defense to invest in Australian rare earths, there could be an unexpected windfall for Australian rare earths producers.
The mine’s concentrator can produce around 240,000 tonnes of ore, including around 26,500 tonnes of rare earth oxides.
Gavin John Lockyer, CEO of Arafura Resources
Total annual production
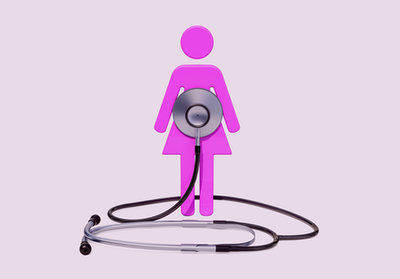
$345m: Lynas Rare Earth's planned investment into Mount Weld.

Caption. Credit:

Phillip Day. Credit: Scotgold Resources