COMPANY INSIGHT
Sponsored by Sandvik
A century of stainless steel manufacturing with Sandvik
The Sandvik name has become synonymous with industry-leading stainless steel, and for good reason. This year marks a century since the first melting in April 1921, which began the journey for Sandvik to expand its capabilities across multiple industries and become the Sandvik Group we know today.
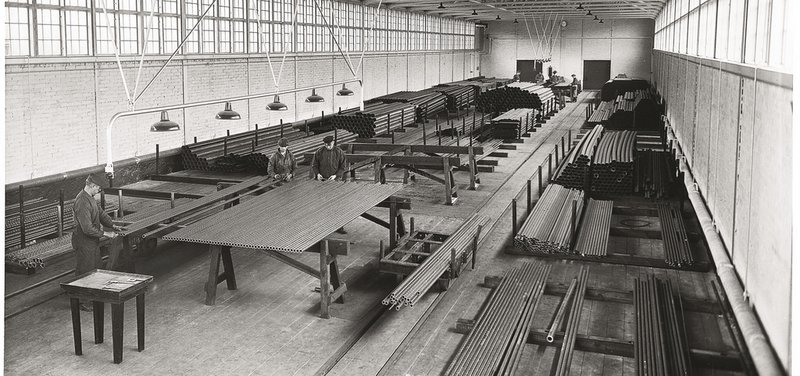
A
s far back as the 1860s, the Sandvik product range has included drill steel for rock-drilling, so stainless steel was a natural introduction. The company’s steel laboratory was expanded to prepare for the new steel grades, as well as other production investments, with numerous company acquisitions and expansions to follow.
Stainless steel manufacturing increased exponentially in the 1930s following the rebuild of the steel mill’s cold-rolling operations, which included setting up a sintering plant and new electrical arc furnaces. By this point, Sandvik had 30 grades of stainless steel in production as its metallurgists worked hard to push innovation, including developing the pilgering method for cold rolling of steel tubes to make it possible to reduce both the outer diameter and the thickness of the tube material in a single rolling operation.
According to Tom Eriksson, vice president and head of strategic research at Sandvik: “Even though we have modernised the equipment from those days, and added processes like continuous casting and extrusion, some of the fundamental processes like pilgering, ingot rolling and forging are the same.”
These modernisations and new capabilities have allowed Sandvik to not only continuously improve on its product ranges within rock drilling, but to expand into entirely new industries, including the production of fine-wire components. This was marked by the acquisition of Kanthal in 1997, a company that had been carrying out wire drawing for resistance and conductive wire for decades. Combining expertise in stainless steel and experience with wire drawing, Sandvik manufactured fine wire for electronic disks, which are data storage units that were used for products such as portable music and game devices. Despite the decline in demand for electronic disks with the advent of smartphones, the development of its high-quality fine wire took off when the company was approached by a pacemaker lead manufacturer.
In 2003, the Sandvik Specialty Steels business area was renamed Sandvik Materials Technology and incorporated five product areas: tube, strip, wire, Kanthal and process systems. The EXERA brand was introduced in 2016 to focus on the production of custom-made medical device wire components.
Today, Sandvik Materials Technology is known globally for its advanced duplex stainless steels. The EXERA® brand includes a range of stainless steel medical wires, such as EXERA® 12R10, EXERA® 11R51/11R51 HV/SH, EXERA® 5R10/2R25, EXERA® High-N medical wire, EXERA® SAF 2205, and EXERA® 4C27A. The brand also offers carbon steels, precious metals, cobalt-chromium-molybdenum alloys, sensor alloys, and Kanthal resistance alloys. This extensive range of materials, in addition to configurations such as wire coatings, now also including extruded coating capabilities, allows Sandvik to work with medical device manufacturers to design and produce medical wire components that are perfectly calibrated for the application, from cochlear implants and pacemaker leads, to catheters and guidewires.
For more information about EXERA® fine medical wire, including a full list of materials, or to contact Sandvik about developing a medical field device, visit their website or download the whitepaper here.
Contact information
Sandvik Palm Coast
1 Commerce Blvd.,
Palm Coast, FL, 32164,
United States
Telephone: +1 386 445-2000
Fax: +1 386 447-5113
Website:exera.sandvik
E-mail:ms.spc@sandvik.com
Sandvik Tucson
2424 East Aragon Rd
Tucson, AZ 85756
United States
Telephone: +1 520 495 5927
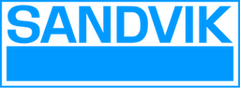