COMPANY
INSIGHT
how one Swedish firm is leading the charge in precision medical wire research
The creation of precision medical wire for complex and delicate procedures is a niche, specialist field and those who are at the forefront of it are there because they devote incredible amounts of time to research and development, to rigorous testing methods and data collection. But in a market as precise as this, to be on the cutting edge of product development, it takes a dedication to R&D that’s worthy of the scientific community.
Swedish-based steel manufacturer Sandvik and its trademark for precision medical wire components, Exera® is one of the companies leading the way in this R&D. But what does a steel products company have to do with something as precise as medical-grade wire? Quite a lot, says Sandvik’s production unit manager at Palm Coast, Florida, Gary Davies.
“Steel is the most recyclable materials there is,” he explains. “It can be re-used over and over again without losing its good features. Sandvik already had the experience of testing steel wires in high-stress or precise arenas – for example, our duplex and super duplex steel with exceptional corrosion resistance, or where we developed a steel cord that’s both finer and stronger for use in cars that increase’s the vehicle’s life and is more sustainable by producing less CO2.
“All of these things are directly transferable to the production of precision medical wire, where, let’s say, the material must last a lifetime, so it must be tested over and over again to ensure it will never fail – things like cochlear implants and pacemakers. So when the idea of expanding into medical wire development came up, we knew we could bring something to this that the medical community needed.”
Davies continues, “Back then our core business was micro-electronics. However, the word was out there that we were very good at making high quality precision wire, so a manufacturer of pacemaker leads contacted us and we succeeded in supporting them with pacemaker leads. The rest is medical history!”
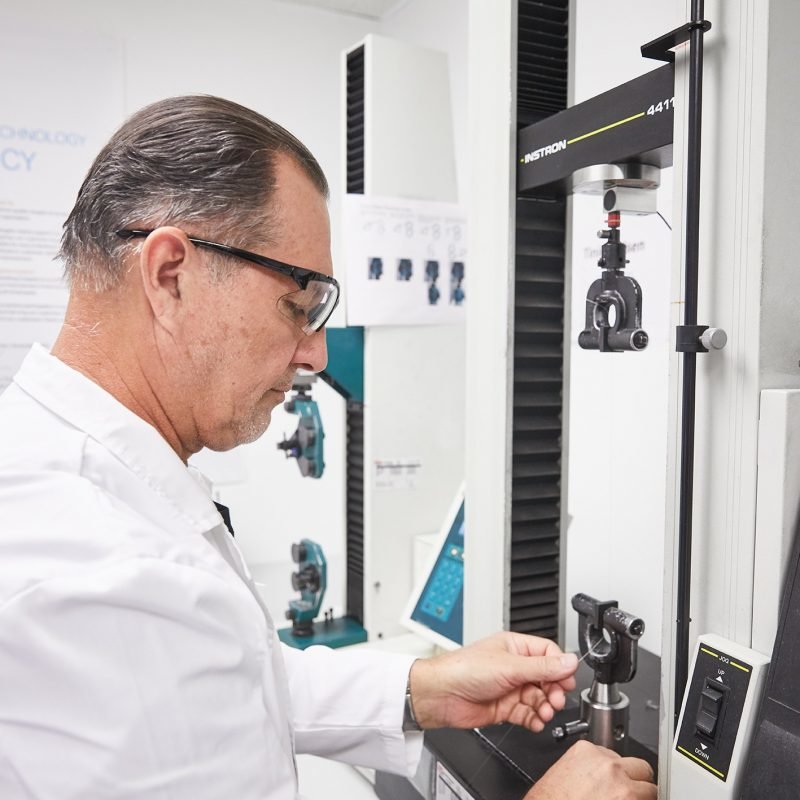
Cyclical Fatigue occurs due to three factors in general, where Sandvik is outstanding: cleanliness of the melt, specialized surface treatment and darwing die quality.
Sarah Williams, commercial features editor at Medical Technology’s sister magazine Medical Device Network sat down with Davies and Sandvik’s senior medical product manager, Gene Kleinschmit, to discuss the future of precision medical wire and how seriously the company takes research and development.
Talk us through some of the most recent and upcoming technology and products you’re bringing to market. In what ways are these cutting edge?
A recent innovation involved developing a manufacturing technique to join a multi-strand cable made from ultrafine wires to a single ended wire in such a way that the joint strength was greater than the individual wire strength. The previous manufactured assembly included the use of a mechanical crimp connection between the different elements. The reliability of the mechanical crimp connector was not sufficient for the long term implant, was difficult to perform, had a larger than carbon footprint and came with considerable cost. The new manufacturing solution that Sandvik developed solved each of these challenges and the technology has now been extended to a number of different customer applications.
What keeps Sandvik on the cutting edge of product development and how can other companies learn from your approach?
In our commitment to the needs of our customers, we systematically collect data about new and growing challenges facing them. Our engineers and specialists work closely with customers to jointly discover ways of addressing these challenges with new or modified products. Sandvik engineers have the right combination of academic qualifications and hands-on experience, and enjoy an active international exchange program with leading research centres and universities worldwide.
What has Sandvik done differently in the wires created for cochlear implants and pacemaker leads that makes them so long-lasting? How do you make sure they will last a lifetime?
To produce these items, we first select alloys and coating materials that are highly stable in the body and also processed in a way to limit problems from known and well-understood failure points, such as cyclical fatigue.
Cyclical fatigue occurs due to three factors in general, and these are areas where Sandvik is outstanding: cleanliness of the melt, specialised surface treatment and drawing die quality – when testing these out of our final product, our in-house capabilities and research experience is so important. Our in-house die craftsmen and women have a combined experience of more than 100 years to put the precise art of die making at our customers’ service. We then perform rigorous validation and acceptance testing on the material and device design to simulate extended life conditions.
What are some of the biggest innovations the industry has seen in recent years and how has Sandvik responded to them?
I think that bringing digitalisation into the medical industry is one of the biggest innovations. For example, having an app to control your diabetes gives you a freedom you never had before, that is life-changing. I think in general that will continue and make more and more people into “health self-service”, for example controlling your blood pressure at home.
Also making the medical devices small and smaller are big innovations. You want to make the invasive operations as small as possible in order to get people better and out of hospitals as fast as possible to save costs. Sandvik’s precision wire-based components are very, very small, which is why we are in the right place to the lead the way for the future.
And how exactly are you leading the charge on cutting edge technology in the medical wires industry?
By continuously have a lot of focus on research and development of new and existing materials and by really focusing on the value chain. We offer the processes and abilities to achieve the goals our customers have – whether that’s a new procedure or application for the wire, or a new design that will help them in an existing procedure. We develop new products and tech based on our customers’ development needs. Because of our agile approach, we offer rapid prototyping which means customers get their devices on the market – and ahead of the competition.