COMPANY
INSIGHT
Applying Cold Spray Additive Machining for Medical Applications
Entrepreneurs, engineering companies and OEMs historically reduce the overall cost of prototyping by simply conducting more design iterations in the CAD workspace. This cost savings was realized by analyzing several design iterations prior to the creation of an actual prototype. More recently, and to some extent in the future, we see CAD packages creating very complex designs that initialize a series of design constraints. Utilizing these design constraints such as strength, weight, material properties, and functionality, a method of Artificial Intelligence (AI) and Computer Aided Design (CAD) creates many design iterations meeting the design constraints.
The Design Engineers (with help from others, such as Marketing) review these designs and sort though the various design proposals identifying the non-tangible constraints such as ‘feel, look, image, message’ for the product. AI based CAD designs typically create very complex shapes. These shapes are sometimes more difficult to manufacture with conventional manufacturing methods, necessitating other methods. Moving forward we need to consider alternate manufacturing ideas. The following is a basic outline of how Cold Spray Additive Machining works along with the features and benefits.
Background on Cold Spray
The manufacturing industry is always looking at new and innovative ways to improve products. In recent years metal-based 3D printing has been at the forefront. Advancements in the 3D printing technology, equipment, and materials have resulted in costs being driven down, making it a more feasible option when manufacturing.
In the past prototypes were used sparingly in medical design work due to cost and time considerations, however new innovations in 3D Printing can provide a faster, more streamlined process that allows medical product manufacturers to develop clinical trial-ready devices in-house checking everything from form, fit and function, manufacturability, and even appeal.
3D Printing in Healthcare is a technology that uses 3D digital files to create physical, solid objects. Computer data builds an object with many thin layers. These printers can produce wearable device, prosthetics, internal organs and medical devices. They reduce the chance of human error, as objects printed using 3D printers provides low to medium accuracy parts. Post machining is common place for higher accuracy requirements. Medical products can be customized like surgery tools, fixtures, implants and many more, making it a leading growth in the market of 3D printing in healthcare
This new technology is quickly becoming a major player in the medical manufacturing industry. Kinetic Research Corporation of Ann Arbor, MI USA, a non-profit scientific research corporation, is engaged in efforts to advance the use and development of the technology in the United States for public benefit. It has acquired a new CNC cold spray metal additive 3D metal printing machine which is located at Protomatic. The machine is the first of its type in the United States and manufactured by the Australian 3D metal printing company SPEE3D of Melbourne, Victoria, Australia (http://www.speed3d.com). Kinetic is developing benchmarks through tests designed to determine the cost efficiency and quality of product produced by the machine in various applications.
Cold Spraying is the most recent method to emerge in the field of thermal spraying. It offers special advantages to conventional spraying because the material is not melted in the process.
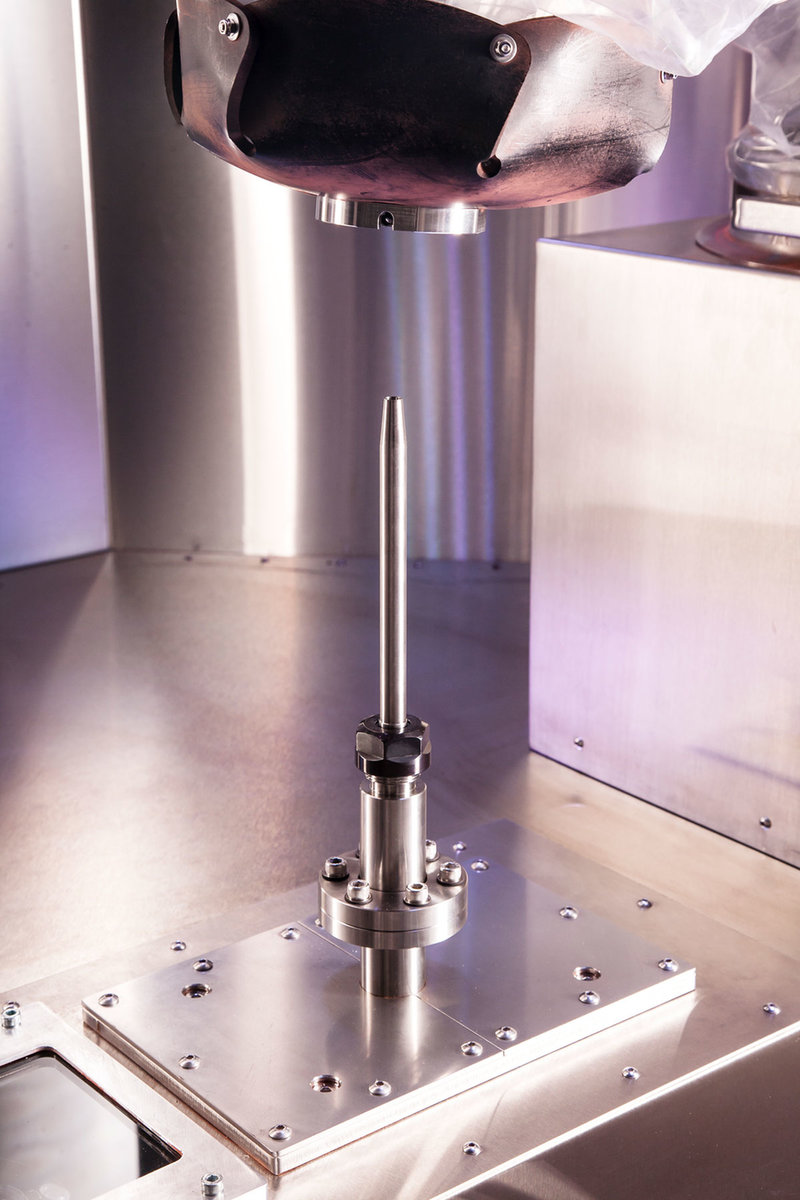
Spray Nozzle directing spray upward to Robot Arm Target Plate
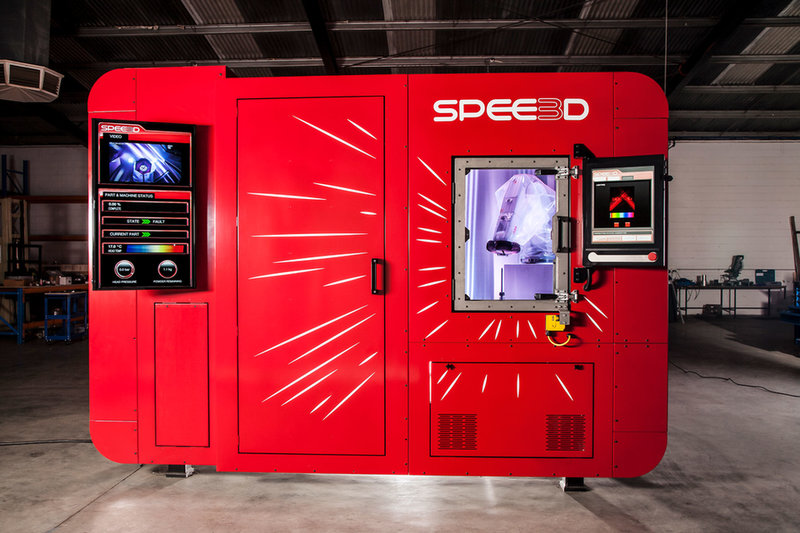
Additive Cold Spray CNC Machine by Spee3D
The Cold Spray CNC Machine
The machine is set up in four basic system components,
- High Pressure Air Compressor and dryer designed for continuous 500 PSI.
- Nozzle Particle Delivery System. Within the nozzle assembly, metal particles are injected into the high pressure air stream and accelerated to “supersonic speed” through a small orifice. This creates an output velocity between 600 and 1000 meters a second (Mach 1.7-9). When the particles impact the target location, the high kinetic energy causes them to instantaneously bond, forming a part through successive layers of 30 micron particles. If the metal particles are too slow the metal bounces off the target; too fast the metal smears, erodes, or splits in to smaller particles. When conditions are right, a part is formed, at near 100% density and has properties very similar to billet material.
- The Targeting System is typically a plate connected to a robot arm or other CNC positioner. The robot arm moves the plate in front of the spray nozzle to build a shape, layer by layer. The particles fuse while hitting the target substrate plate and then begin to build on top of one another. Successive robot motion creates the desired shape of the complete part. As a comparison this method of printing is significantly faster than existing than powered layered fusion process and is similar in speed to robotic welding, but without the unpredictability that results from melting a metal.
- Powder Recycling; simplistically it is a Dust Recovery Collector, designed to control
residue particle material for recycling savings and environmental control.
Benefits & Applications
Cold spray works with many alloys, most easily non-ferrous metals such as Aluminum and Copper. This provides common and inexpensive alloys, that are perfect for replacing many casting, manifolds, braces and brackets, pulleys and heatsinks.
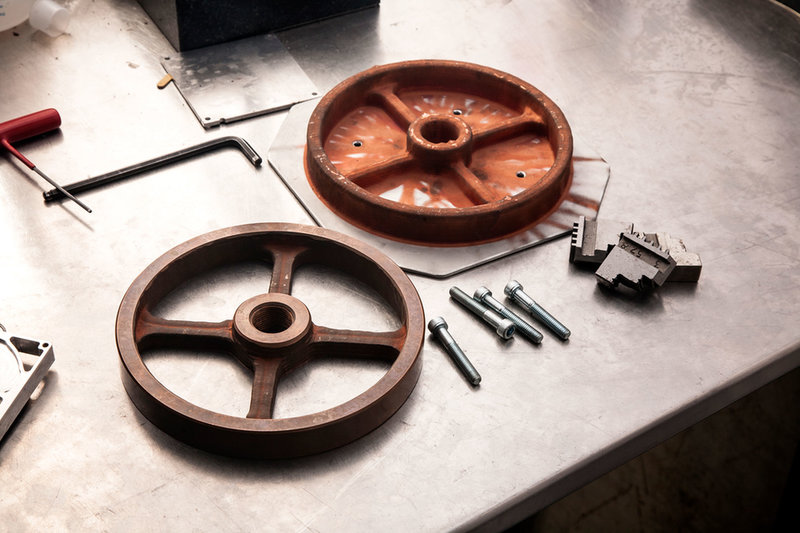
Caption: Adapter Plate and Heat Sink printed in alumium and copper.
As we add more sophistication of design in our products, we look for new manufacturing methods that can produce economically and accommodate multiple design constraints. Sometimes thinking outside the box allows exploration of materials and shapes that will accommodate innovative improvements in products, such as improved cooling in heat sinks, to the use of copper for medical applications for its natural antibacterial properties.
Applied Harmonics:
If you are interested in a visit to see the machine or get a quote on a part, contact Protomatic, Doug Wetzel.