COMPANY
INSIGHT
MPS supplies to a Blue Chip Medtech company in the US the dosing system for a programmable implantable infusion pump. The pump’s main requirement is to deliver a specific amount of medication using the energy stored in an embedded battery. To guarantee this requirement over the entire lifetime of the product (7 years), MPS has optimised a very precise implantable microsystem which performs the function with nearly no friction and therefore minimal energy consumption.
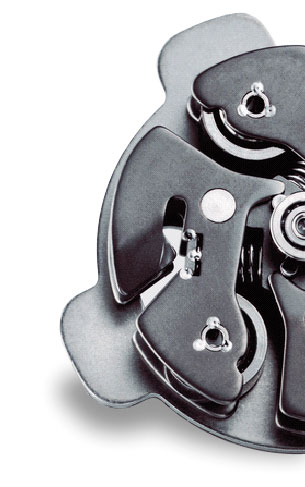

Spine surgery is a very delicate operation, with success depending on the individual performance of the surgeon. MPS manufactures a small and very precisely adjustable spine surgery assist robot (positioning precision = 1µm), which makes the accuracy of the surgical procedure less dependent on the surgeon’s daily performance.
Biocompatible actuators
MPS’ biocompatible actuator technology consists of an encapsulated motor, electronics and power element, as well as a gearbox and leadscrew made of biocompatible materials. The actuators and electronics are designed for long term implantation and for wireless data and energy transfer. This technology has a wide range of applications in the orthopaedic, spine, CMF, urology and other markets.
Miniaturisation
Integrating as much functionality as possible into the smallest available space is a key competence of MPS and a requirement of the market for active implants. MPS engineers are combining their know-how in micro bearing technologies, the know-how of their parent company Faulhaber in micro motors and gear boxes and the competences of their electronic partner in order to develop and manufacture implantable, intelligent microsystems featuring low energy consumption.
Very high precision component manufacturing and system assembly in clean environment
Very precise components are at the heart of MPS’ microsystems. These components are manufactured at MPS own workshops in Biel/Bienne: Swiss turning, flat, round and centerless grinding as well as polishing yield components with tolerances lower than 1µm and to a surface roughness of less than 0.1 Ra. MPS is also well equipped for heat treatment and component cleaning.
Very impressive are MPS’s microsystems assembly capabilities: in order to reach the required repeatable precision and the lowest possible friction by keeping system stiffness, MPS has developed its own assembly processes and capabilities. Using MPS made assembly benches and jigs, the operators pair components to a precision of less than 0.2 µm in series production. Depending on the requirements, system assembly is taking place either in a dust free room or in a clean room ISO class 7.
Technical files
MPS project / product documentation conform to CE standards, 510k and PMA requirements. MPS customers may use this documentation to complete their submission dossier.
Orthopaedic instruments
Since December 2012 MPS has a new subsidiary named “MPS Precimed” located at Corgémont in the Bern Jura. With its 90 employees MPS Precimed develops and manufactures innovative orthopaedics instruments for the main Blue Chip orthopaedic companies. Reamers, impactors and drills are part of MPS Precimed’s product portfolio.