Company Insight
Sponsored by Alleima
Elevating MedTech: The Growing Value of Electroplating in Medical Device Manufacturing
As MedTech embraces miniaturization and minimally invasive surgeries, electroplating enhances device durability, conductivity, and biocompatibility. Alleima's expertise ensures patient safety and drives innovation in advanced medical tools and implants.
Main image: Reel-to-reel plating of wire. Electroplating allows manufacturers to add a thin layer of metal to a component built from another material.
Advanced devices are now giving hope to greater numbers of patients living with Parkinson’s disease. Millions of people worldwide are affected by the chronic and progressive neurological disorder.
The disease predominantly affects the motor system, leading to symptoms such as tremors, rigidity, and bradykinesia, and originates from the degeneration of neurons in the substantia nigra, a part of the brain that is crucial for regulating movement.
Traditional treatments have largely revolved around medications and physical therapy, but recent advancements in neurotechnology, specifically brain implants, are starting to significantly alter the treatment landscape.
According to GlobalData’s Parkinson’s disease global drug forecast and market analysis [1], treatment rates vary depending on the severity of the disease and the region. Early-stage patients receive drug therapy in 74%-88% of cases, and this rises to 82%-95% in advanced-stage patients. Approximately 5%-10% of patients are referred for a deep brain stimulation (DBS) procedure, representing more advanced and severe cases.
Electroplating plays a more crucial role and rises in value for MedTech manufacturers
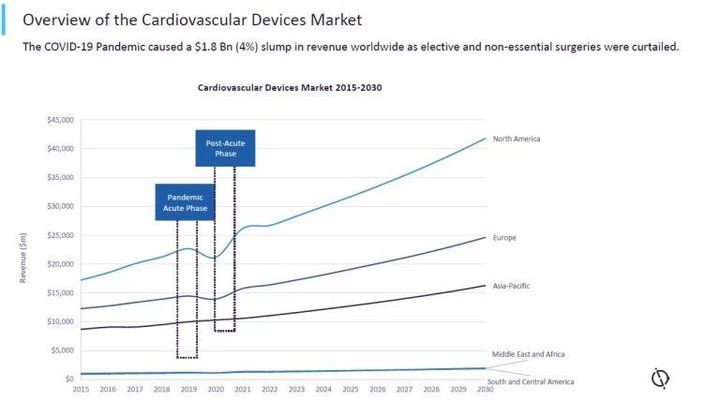
The Covid-19 pandemic caused a global shock to the medical services market. In some areas, this entailed a sharp surge in demand, leading to lowered inventories and a scramble to fulfil orders. In many areas, disruption was in the form of a sudden drop in demand, with elective and non-essential surgeries curtailed. According to GlobalData analysis, some of the market segments that saw the biggest fall were interventional cardiology, cardiac rhythm management, surgical heart valves, clot management devices, and atherectomy devices. As the pandemic progressed, some restrictions were relaxed to enable hospital procedures to resume.
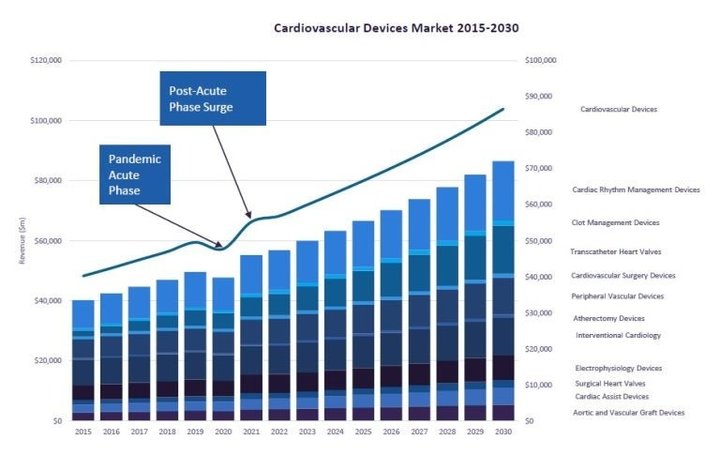
Electroplating is a versatile and essential technique for the production of many medical devices, but as the trend towards miniaturization gains momentum, there is a growing need for specialist expertise in the creation of electroplated wires and micro-components. Alleima not only draws on vast experience in the field of component manufacture but is consistently growing its portfolio of expertise. As the medical sector increasingly relies on smaller devices and minimally invasive surgery, and as the coating of implants and other devices comes to play a more crucial role in their longevity and performance, expertise in key techniques such as electroplating will only rise in value.
Electroplating is a process familiar to many industries and, more than 200 years after the process was invented, it still plays a key role in innovation as new manufacturing processes evolve. Simple in its s concept, electroplating allows manufacturers to add a thin layer of metal to a component built from another material, enabling it to have improved electrical properties, or barrier capability. Electroplating lets device manufacturers combine the strength, electrical conductivity, abrasion and corrosion resistance, and appearance of certain metals with different materials that boast their own benefits, notably affordable and/or lightweight metals or plastics.
In the medical device field, where coatings play a key role in delivering biocompatibility and increased strengths besides the features mentioned above, it is a process fundamental to the performance of many implants, surgical tools, sensors, and other equipment. Implants such as screws, plates, and replacement joints are frequently electroplated to enhance corrosion-resistant properties and, crucially, biocompatibility. The ability to achieve very thin coating – in some cases as thin as 0,10 micrometer (0,000003 inches) – makes the process highly cost-efficient.
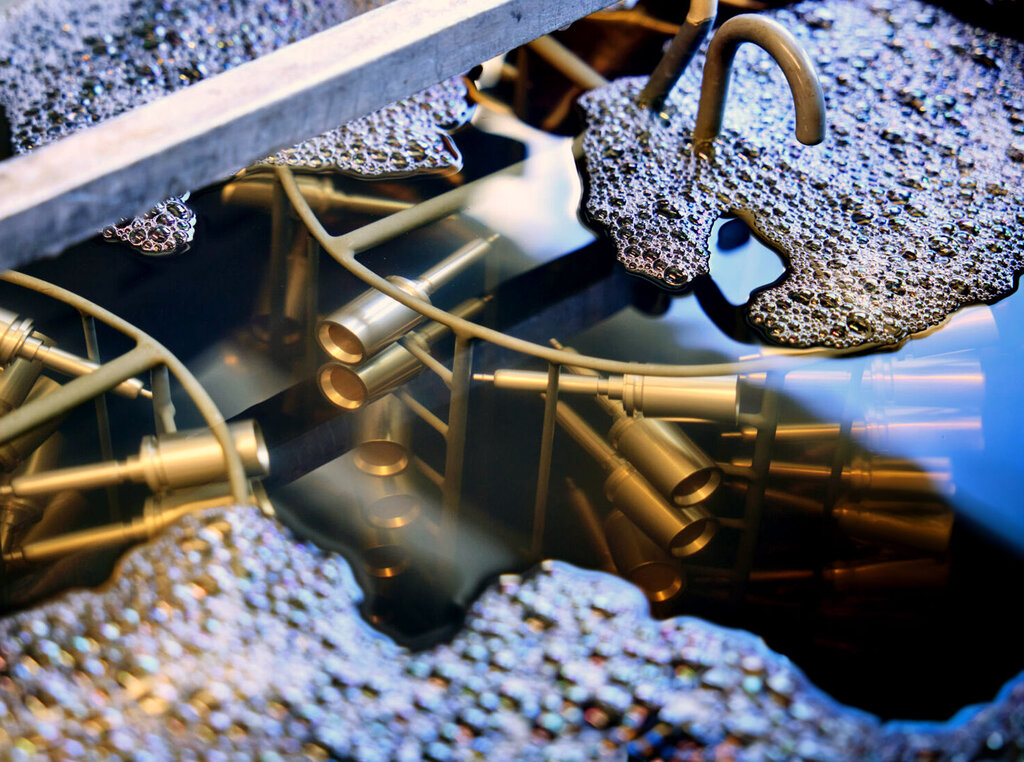
One of the main reasons why electroplating has become an essential part of medical device manufacturing is to improve patient safety by allowing the more durable materials used in implants to be rendered biocompatible.
Applications in MedTech
The applications for electroplating in medical device manufacturing are diverse. One of the most common uses of the process is the creation of electrical contacts, where gold plating often is preferred as it delivers high conductivity as well as corrosion resistance.
In imaging devices, electroplating is often used to coat the metallic components in devices such as arthroscopic and endoscopic tools. These, as well as scanning devices, often need the kind of corrosion protection that electroplating delivers, particularly to cater for long periods of use.
One of the most common uses of the process is in the manufacture of implants, which must survive and function for long periods inside the human body. Implants either support or replace biological structures, as with orthopedic implants that take the place of tissues that have been damaged, or cosmetic implants that supplement existing structures for aesthetic purposes.
Orthopedic implants that replace joints such as hips and knees are frequently made of metal to provide the necessary strength and durability, but some kinds of metal score low for biocompatibility or may even be toxic to the body, so electroplating with gold or titanium, for example, may be essential to their function.
“Electroplating is used to change the characteristic or to combine different characteristics that do not exist in one alloy or one metal,” says Arnaud Bochdanowicz, Sales and Development Manager EMEA at Alleima in Switzerland. “For example, you may need some strong material like stainless steel, but you are not allowed to use it in a certain application, or you have difficulty making the electrical connection. If you put gold plating on the stainless steel, you have the specific mechanical characteristics of the stainless steel and you can connect this product. The main benefit is to be able to combine specifications that are not otherwise compatible together.”
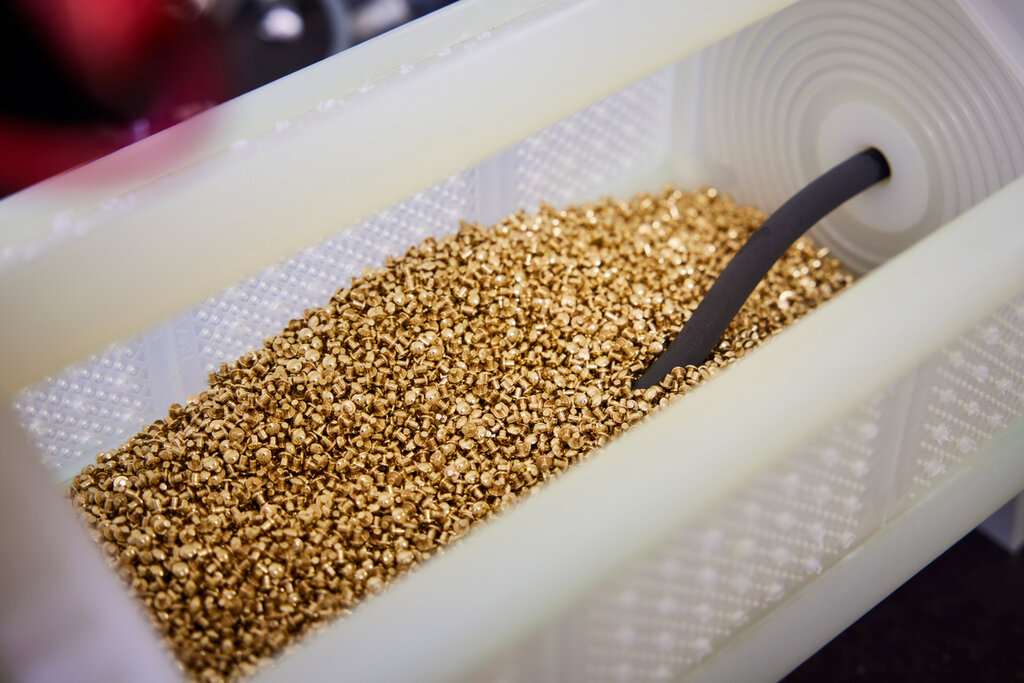
Barrel plating of small parts. Implants and instruments are frequently electroplated to enhance corrosion-resistant properties and, crucially, biocompatcost-effectivey cost effective process.
The key benefits of electroplating
There are many reasons why electroplating has become an essential part of medical device manufacturing, but the most obvious is its potential to improve patient safety by allowing the more durable materials used in implants to be rendered biocompatible. Certain metals that deliver the durability required for a major implant, such as a knee or hip replacement, can release ions or cause allergic reactions when implanted into the human body. The electroplating of these metals is essential to enable their use in implants, as it can prevent such reactions from occurring when there is contact with human tissue or internal organs. Equally important, however, is the ability to coat a component with a highly conductive metal, as many medical devices require electricity to operate, and others generate heat and, therefore, need a conductive coating to draw heat away from the body.
For medical devices that are used repeatedly - such as scopes or surgical clamps - it is important to reduce wear and tear to extend their functional lifespan. Here, electroplating can greatly increase corrosion resistance. Both use and repeated sterilization with highly alkaline cleaning products can accelerate corrosion, which can be mitigated by electroplating these instruments with the appropriate metal coating.
A related benefit of electroplated coatings is that they can, depending on the choice of metal, improve antimicrobial properties. This is important in the medical environment, where hygiene standards are high and reusable devices are frequently sanitized after they have come into contact with human tissue.
Other common uses include the coating of medical devices in high-density metals, notably gold, to block radiation. Gold is radiopaque and can prevent radiation from reaching a specific area during an X-ray procedure. Also, in the device manufacturing phase, welds may be required between different metals, which may not be easy to bond. Coating stainless steel and nickel titanium, for instance, with a common material such as nickel or gold provides a low-cost way to lower the use of more expensive alloys.
In short, electroplating can greatly enhance the functionality of many medical devices and tools by enabling them to better conduct heat and electricity, resist wear and corrosion, and create antimicrobial and biocompatible surfaces. This benefits patients, as well as device manufacturers, in many ways. With the growing prevalence of minimally invasive surgical procedures, there is a growing need for smaller surgical tools. Electroplating can play a key role in the manufacture of these tools for minimally invasive surgery. An electroplated catheter, for example, could be vital in quickly and accurately placing an implant such as a stent or a valve.
Contact information
Alleima Advance Materials
1 Commerce Blvd.,
Palm Coast, FL, 32164,
United States
Tel: +1 386 445-2000
Fax: +1 386 447-5113
Email: sales.pc@alleima.com
Alleima Tucson
2424 East Aragon Rd
Tucson, AZ 85756
United States
Tel: +1 520 495 5927
Alleima Zug
Oberallmendstrasse 20a
CH-6300 Zug
Switzerland
Tel: +41 41 761 63 55
Email:sales.sb@alleima.com
Alleima St Imier
Rue de Beau Site 8
CH-2610 Saint-Imier
Switzerland
Tel: +41 32 942 39 20
Email: sales.sb@alleima.com
Alleima Karlsruhe GmbH
Wilhelm-Schickard-Str. 9c,
76131 Karlsruhe
Germany
Tel: +49 |0| 721 957 967 000
Email: sales.ka@alleima.com