COMPANY INSIGHT
Sponsored by Sandvik
How a team of R&D engineers for custom small melts support global medical wire production
Sandvik Materials Technology develops partnerships with OEMs all over the world to develop customised and optimised wire components specifically calibrated for their application. The company is divided into small and specialised units, including Business Unit Medical, which designs and manufactures fine medical-grade wire for use in medical devices.
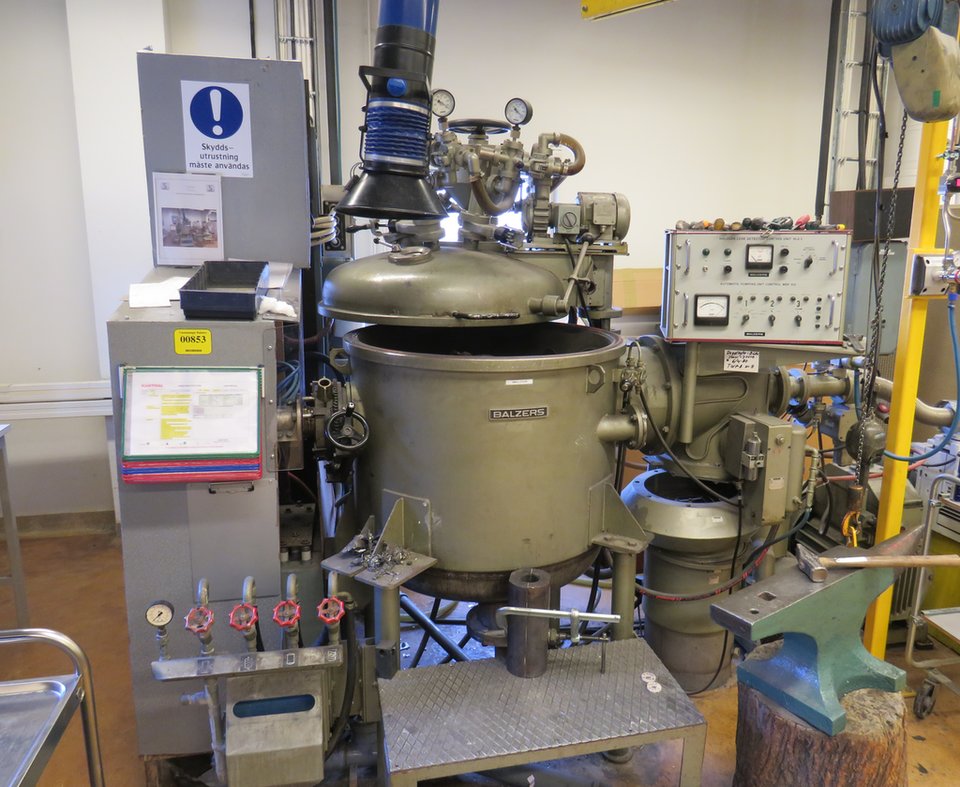
F
rom its manufacturing facilities in Palm Coast, Florida and Tucson, Arizona Sandvik creates customised precise medical wire backed by an experienced team of expert research and development engineers based in Hallstahammar, Sweden.
The R&D Centre in Hallstahammar, Sweden is an essential part of the Sandvik family, carrying out research and development in various areas of metallurgy and process development, including custom small melts, to expand upon and innovate the alloy materials available to the medical device sector. They also develop products and services in the area of industrial heating technology and resistance materials under the world-famous Kanthal brand.
Medical-device technology spoke with Thomas Helander, an R&D Engineer with 18 years of experience at the Hallstahammar R&D Centre, about what his role entails and how this small unit enables Sandvik to help its customers.
Thomas Helander holds a PhD in Materials Science and Engineering and works in the Sandvik R&D department in Sweden.
Thomas Helander holds a PhD in Materials Science and Engineering and works in the Sandvik R&D department in Sweden.
“There are approximately 30 people here to support the business. A lot of our time goes into doing research and development, and then we work together with external partners. We do projects together with universities and institutes in order to learn more and try to improve our knowledge and products.
“Over the years, we’ve done quite a bit on the medical side, so we’ve accumulated a lot of knowledge on medical applications for medical customers. Our production units for ultra-fine wire are located in sunny Palm Coast in Florida and Tucson, Arizona, that are where they make the actual wire-based products, but the engineers and people there sometimes need support when it comes to making, for instance, new alloys, or they have different kinds of technical questions they need help with. That’s when they would come to us and we work together with them in order to support them.
“Over the last couple of years, this activity has increased. With business increasing, there are more questions coming in from our colleagues in Florida, and there are different types of questions. They could be trying to find the correct alloy for a certain application, it could be trying to develop a special alloy or product for some customer or application, or it could also be trying to support their production issues etc. From what I can see, there’s a lot of innovation going on in the medical field and that is also driving these kinds of questions.
“Sometimes customers need very special mechanical properties or electrical or magnetic properties. Most of the time I would say it is something that comes close to existing material, so a lot of the time we can start out from something that we know and then we can try to adjust or fine-tune or adapt the composition or a process in order to give them what they want, which is it something improved for their application.”
An important unique selling point that Sandvik offers is its ability to produce small batches of melts to for example prototypes, meaning that components can be tested and fine-tuned without waste.
“We have the ability to make small scale experiments, normally when you make a new metallic alloy, the production system is designed for large scale production, which is very time consuming and very expensive. We have an experimental facility in which we can make one kilogram melts so we can conduct many small experiments and try things out, and that allows us to deliver samples or very small orders of custom made alloys.
“For us, it’s also something which is quite fun because you’ll learn a lot, when talking to customers you get insights into new fields and you get to see that what you’re developing is going towards something useful. You get some feedback on if it works or if it doesn’t work, and so on. So it’s something we quite enjoy.”
Get your free seat at the webinar!
Check out and register for the coming webinar that Thomas will participate in on the 26th of April. He and his two colleagues Dilip Chandrasekaran and Gary Davis will talk about designing and manufacturing custom small melts. The medical industry has shown a need for more advanced materials for new, smart and high-tech applications. Read more here.
Contact information
Sandvik Palm Coast
1 Commerce Blvd.,
Palm Coast, FL, 32164,
United States
Website:exera.sandvik
E-mail:ms.spc@sandvik.com
Telephone: +1 386 445-2000
Fax: +1 386 447-5113
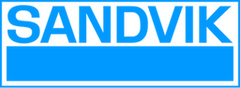