COMPANY INSIGHT
Sponsored by Formacoat
Formacoat llc: Medical Coating
So, here you are, holding the latest revision of your new device and it isn’t working quite right; yet.
Perhaps a coating, the right coating, will make the difference!Issues with medical device design, materials and uses can vary considerably. Coatings vary considerably also.
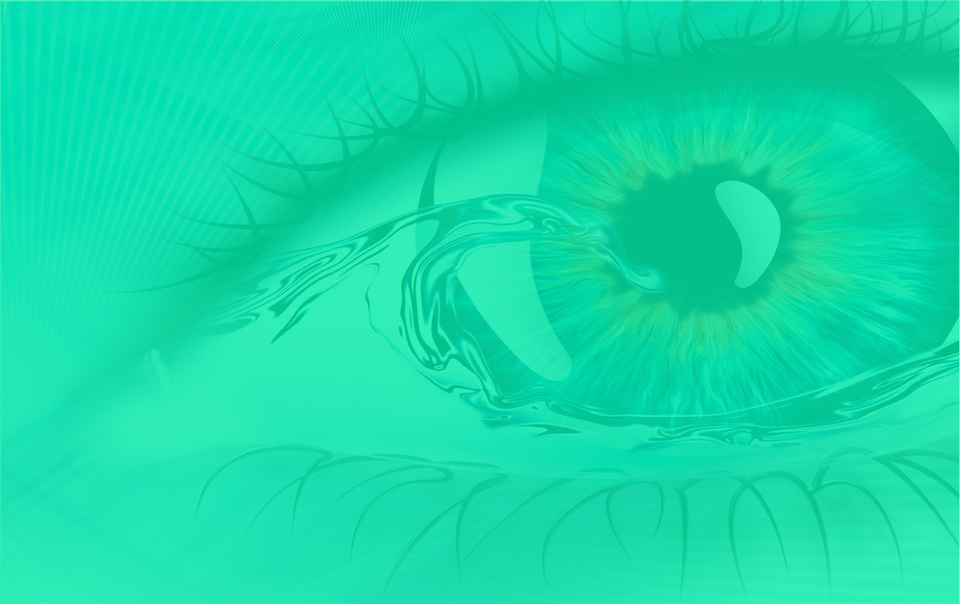
In between medical device issues and coatings lay the foundations of Formacoat® LLC, a contract manufacturer that specializes in commercial-production application of liquid applied coatings to our customers’ medical devices as a custom service. We don’t make or sell coatings, but we know and work with many different coating suppliers. Part of our service is to be able to parse the diverse field of coatings to help find the right coating for you and your medical device challenge.
Welcome to the world of Formacoat® LLC, an ISO 13485 certified company.
Our customers range from individual doctors and small start-ups, all the way to large international medical device firms. Formacoat® has the experience and depth of knowledge to be beneficial to customers across the entire spectrum. But no matter the size of your company, Formacoat® will be there for you to solve all of your coating needs.
Formacoat® has the equipment, facilities, coatings, knowhow and expertise to solve any coating challenges. If we have not done it yet, our experience and creativity is always up to the challenge. We coat all manner of OD, ID’s, stents, balloons, flat films, foils and mesh, and complex shaped medical devices with a wide array of biomedical materials.
Our premise is that there are no bad coatings; it is just that one type of coating chemistry may work better for you than another. Say you happen to be lucky (or skilled) enough in life to own both a Ferrari® and a pickup truck. Would you use your Ferrari to go to the lumber yard to pick up plywood? Of course not! While the Ferrari is an exquisite automobile, it would not be the right vehicle for that particular transportation need. Coatings are like this.
We use our 18 years of knowledge, experience and testing to find the best coating for your needs. So if it occurs that a particular coating does not work to your satisfaction, we can easily apply what we’ve learned in the first experiments to different types of coatings from one of our many other vendors. That means that you don’t need to teach someone about your device multiple times, as you would if you were going directly to several coating vendors. Not to mention these vendors are beholden to their own coatings and chemistries, meaning what they have might work ok, but the question remains: Is it truly the best solution for you? Does it functionally meet your needs? Does it match the needs of your substrate and device correctly? Does it financially match your needs? Our approach allows us to streamline the entire process, making it a fast and efficient use of your time and money for your project.
We regularly coat catheters, micro-catheters, tubing, guidewires and film. Yet with our in-house tooling capabilities and seasoned staff of R&D engineers and chemists we have tackled a variety of odd geometric shapes, configurations and applications. We have the experience to coat anything you can dream!
Our most common request is for devices to be coated with hydrophilic coatings as a way to reduce friction. Hydrophilic coatings require water to activate the lubricity, which in a typical surgical situation is very easy to do. In terms of friction, one may consider that Hydrophilic coatings are in general 1 to 2 orders of magnitude less friction than many common medical device materials, even the typical Teflon® (or other types of fluorinated surfaces). Formacoat® has multiple vendors of hydrophilic coating technologies and chemistries.
Since Formacoat® was founded in 2002, we have expanded the number of vendors and currently offers a variety of different types of coatings, which include hydrophilic, hydrophobic, Surface-blocking/Anti-fouling, Anti-Microbial, Heparin, Collagen and PSA/Adhesive coatings. We are also increasing the number and types of PTFE and other fluorinated coatings we offer, including several lower temperature types for some alternate needs. These coatings are typically cured either thermally or through the introduction of ultra violet light. With a catalog of over 80 different coatings from more than 40 different vendors, Formacoat® offers a multitude of coating solutions with coating methods including dip, spray, graft and roll for regular medical devices like catheters, micro-catheters, tubing, guidewires, and film. Additionally our new facility has dedicated a 700 square foot cleanroom entirely to drug coatings on stents and balloons.
The increasing range of coatings and coated products means we had outgrown our previous facility and equipment. Our new facility allows expansion in its core catheter processes four fold, including a new coating system that work well for both small volume R&D runs at less cost, and for some products, “unlimited” lot sizes (larger than our batch production lines can do); film / mesh coating by two fold; six fold increase in square footage of ISO Class 7 cleanrooms; and space for other work by increasing by three times the square feet of our previous facility.
Newest developments: With the expansion of our production floor, we have invested a large amount for the equipment, added experienced staff and dedicated a separate ISO Class 7 cleanroom to supply the drug coating market, specifically Stents and balloon catheters. Our coating expertise, equipment and facility now includes drug coatings for drug eluting stents and balloons for coronary, peripheral and neuro devices. New customer work is also ongoing in the realm to bio-absorbable materials and drug containing coatings, which is further expanding our range of capabilities and services for the diverse medical device industry. We are getting increasing interest and work in our range of non-thrombogenic coatings from different vendors, which include different heparin, silk, and phosphorylcholine coatings.
Our company has also introduced a new grafting technology that’s hydrophilic in nature and is customizable by each customer’s specific substrate material. Think of this coating like a field of grass; we can dial the parameters is such a fashion that we can have the grass sprout up wherever we’d like but also as thick or thin as possible and as long or short as desired. Not only does this allow us to tune the lubricity and durability, but this application is excellent for the smallest of IDs where traditional hydrophilic coatings are unable to be functionally applied. In the past year we have been working to find ways to use this grafting technology on metals that were previously only working on some polymers. And this technology is only available one place in the world: Formacoat®!
Formacoat®’s objective has always been to provide an effective one-stop shop for small to large-scale commercial coating applications for a range of uses, including vascular, cardiovascular and implant delivery, and devices like catheters, guide wires, stents and film roll-to-roll and tubing and wire/tubing reel to reel applications. We accomplish this through our “SOLUTION” approach to coating needs. It revolves around one simple idea: “What do you want and why?” We call this the “Formacoat®Formula”. While this may seem like a basic concept, it is one that often times can be overly complicated and even missed altogether. We are continually amazed at how important the answers are to this seemingly simple question. Before we offer answers to your coating challenges utilizing our 18 years of experience and variety of coating options, we want to know what you care about; what the customers who use your device care about. By digging deeper and listening to our customer’s needs, we gain a better understanding that leads to improved results, sooner. This saves our customers not only financially, but also in our customer’s most valuable commodity: TIME.
And our experience doesn’t just relate to coatings and application techniques. We have the experience to take you from concept to production all under one roof! That along with our full scale R&D Lab and seasoned staff of engineers and chemists means we are poised and eager to help our customer get to the finish line with their devices and start generating revenue!
Formacoat®’s work in these kinds of areas is emblematic of a much larger commitment to innovation that will serve you well.