Cover Story
Swiss researchers pioneer 3D-printed robotic hand
Researchers from the Swiss Federal Institute of Technology (ETH) Zurich, in collaboration with Inkbit, have successfully printed a robotic hand with bones, ligaments and tendons made of different polymers using a new 3D laser technique. By Bernard Banga.
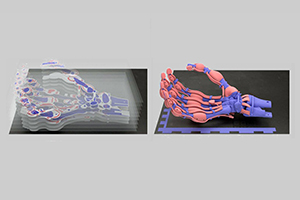
3D printing, robotics, robotic hand. Credit: Swiss Federal Institute of Technology
Researchers have long dreamed of producing synthetic systems that are able to operate like natural organisms. To achieve this, they need to be able to create actuated systems with high spatial resolution and complex material structures that involve both elastic and rigid components. Conventional engineering systems typically use precision machining techniques, mainly using metals or rigid composite materials.
“These systems are usually stiff (greater than 1 GPa) for ease of control; therefore, they contain only a few soft elements or flexible joints”, explains Robert Katzschmann, Assistant Professor of Robotics at the Swiss Federal Institute of Technology (ETH) Zurich.
While hybrid soft-rigid systems are able to include polymers of varying stiffness, from soft (around 3 kPa) to rigid (around 3 GPa), manufacturing them involves casting or printing at a coarse resolution and with restricted material options.
Overcoming limitations in printing technology
Direct ink write (DIW) methods have emerged to address this need, enabling structures to be made from multiple resins with elastic moduli ranging from 0.02 to 1,600 MPa. While DIW-produced structures have a resolution greater than 50 μm, they are limited in their scalability, which is restricted by the number of nozzles, and are not agile enough to quickly switch between materials on a voxel level.
In traditional 3D inkjet printing, thousands of individually addressable nozzles are used to deposit low-viscosity resins, which are then mechanically planarised and cured using ultraviolet (UV) light. This approach facilitates significantly faster layer-by-layer printing compared to line-by-line methods such as DIW or fused filament fabrication, including at a similar resolution. Traditional 3D inkjet printing can also be used to make multi-material bellows for suction grippers, alter material stiffness by interspersing inks, produce thin layers of shape memory polymers from soft and rigid acrylates, and incorporate non-curing inks to manufacture hydraulic systems.
“Despite these advancements, both traditional and hybrid systems encounter limitations”, notes Katzschmann. With traditional methods, the issues concern material diversity and resolution, while hybrid systems require intricate additive manufacturing techniques to consistently produce finely detailed structures on a large scale. “It remains an open challenge to fabricate functional systems automatically and quickly with a wide range of elastic properties, resolutions, and integrated actuation and sensing channels”, adds Katzschmann.
Vision-controlled jetting: a new inkjet deposition process
To overcome these limitations, ETH researchers have developed a new 3D printing method specifically designed for slow-curing polymers. This new technology integrates a 3D laser scanner that rapidly examines each printed layer for surface irregularities, eliminating the need for scraping. Katzschmann’s team collaborated with the US-based startup, Inkbit Inc., which is headquartered in Medford and is a spin-off from the Massachusetts Institute of Technology (MIT). Their research project received funding from Swiss institutions such as the bank Credit Suisse and the Swiss National Science Foundation, and US organisations including the Defense Advanced Research Projects Agency (DARPA), the Naval Air Warfare Center (NAWC) and MassVentures, headquartered in Waltham, Massachusetts.
“We propose an inkjet deposition process . . . that can create complex systems and robots”, explains Wojciech Matusik, a Professor of Electrical Engineering and Computer Science at MIT and a co-founder of Inkbit.
Vision-controlled jetting (VCJ) uses a high-speed 3D laser profilometry system comprising four cameras and two laser sources to capture a depth map of the entire surface as it is being printed and compensates for deviations from an ideal planar surface by locally adapting the amount of resin to be jetted in the following layer. This feedback loop does not slow down the print process.
“Our method is 660 times faster than previous work by achieving a throughput of up to 33 ml min−1,” states Katzschmann in an article published in Nature, and further explains that the contactless procedure enables them to print chemistries that cure slowly, such as thiolenes, which polymerize via a step-growth process.
Material characterization for bones, ligaments, and tendons
Since the structure of the polymer is built with more precision using this slow cure mechanism, it gives researchers greater control over both the backbone of the polymer and the degree and structure of crosslinking. By using VCJ on slow-curing chemistries, it is possible to manufacture parts with a wide range of material properties, including chemical and outdoor (UV and moisture) compatibility. ‘Our printer can create hybrid structures at a high resolution (32 μm × 64 μm × 20 μm voxel size) and with a high throughput (24 × 109 voxels h−1) for build speeds of up to 16 mm h−1 in the z direction for a total of 6.15 × 1011 individually assigned discrete 3D volume elements’, explains Thomas Buchner, a PhD student in Mechanical and Process Engineering at ETH Zurich, and the first author of the study published in Nature. The build volume of the printer is 500 mm × 245 mm × 200 mm.
The adaptability of VCJ allows for the seamless integration of flexible, elastic and rigid materials, facilitating the production of complex structures and components, including those with cavities. The Swiss-American researchers have used this new method to accomplish a significant milestone: printing a robotic hand – which incorporates bones, ligaments and tendons made from a variety of slow-polymerising thiolene polymers – in a single job.
Advancing contactless printing: performance and range of materials
Since continuously curing chemistries can be used in this new contactless process, it expands the range of printable materials and elastic moduli. The study published in Nature showcases significant advances in the properties of these new printable material ranges. Under the specific conditions and physical parameters assessed in the study, flexible thiolene appeared to outperform conventional materials in various aspects, demonstrating a higher elastic modulus and elongation at break after exposure to weathering, along with a higher modulus of resilience. It is, however, important to note that these findings are specific to the study and may be different under real-world conditions and with additional evaluation criteria.
VCJ technology provides an automated, high-throughput approach to manufacturing high-resolution, durable, multi-material functional systems, enabling the creation of intricate robots with integrated sensing and actuation channels. While VCJ expands the range of usable materials and can be used to construct complex geometries with internal structures, challenges include the low viscosity of the UV-induced curing materials and issues with material interface adherence. The Swiss-American research team is, however, pursuing work that aims to address these limitations through specific material adjustments and enhancements in printer resolution.
Caption: The US Pentagon is seeking to reduce carbon emissions through a range of programmes, but will it go far enough? Credit: US DoD
Australia could be one of the main beneficiaries of this dramatic increase in demand, where private companies and local governments alike are eager to expand the country’s nascent rare earths production. In 2021, Australia produced the fourth-most rare earths in the world. It’s total annual production of 19,958 tonnes remains significantly less than the mammoth 152,407 tonnes produced by China, but a dramatic improvement over the 1,995 tonnes produced domestically in 2011.
The dominance of China in the rare earths space has also encouraged other countries, notably the US, to look further afield for rare earth deposits to diversify their supply of the increasingly vital minerals. With the US eager to ringfence rare earth production within its allies as part of the Inflation Reduction Act, including potentially allowing the Department of Defense to invest in Australian rare earths, there could be an unexpected windfall for Australian rare earths producers.
The mine’s concentrator can produce around 240,000 tonnes of ore, including around 26,500 tonnes of rare earth oxides.
Gavin John Lockyer, CEO of Arafura Resources
Total annual production
$345m: Lynas Rare Earth's planned investment into Mount Weld.
Caption. Credit:
Phillip Day. Credit: Scotgold Resources