Company Insight
Sponsored by Alleima
Why are Alleima products perfectly suited for the surgery robots of the future?
As elderly and surgical patient populations grow and medical technology continues to improve, the surgical robotics market is seeing a major boost.
The da Vinci Surgical System (developed by Intuitive Surgical), was the first robotic surgical system approved by the US Food and Drug Administration in 2000 over 20 years ago, spurring significant investment in medical robotics. Robot-assisted surgery opens the door to more minimally invasive surgical options, the benefits of which include shorter hospital stays, lower risks of complications, less pain, and smaller scars.
Robotic surgery systems allow surgeons to operate with greater precision, reduce complications, and result in faster recovery periods. Because robotic surgery is less invasive, patients typically require shorter hospital stays than they would with traditional open surgery. Advances in technologies such as AI and cloud computing are also making way for innovation in surgical robotics, which will see better clinical outcomes and reduce the workload for healthcare providers. Furthermore, manufacturers continue to improve robot design so that they are more efficient through innovations in engineering and metallurgy.
Nitinol instruments add flexibility to surgical robotics
“Today, the setup time for a surgical robot in the operating room is still rather long. In addition, the applications are limited due to their rigidity and numerous hinges. These obstacles will be overcome by the next generation of surgical robotics, the soft robotics. These flexible, hingeless robotics will be able to be inserted even deeper in the body and therefore address todays unmet needs. In combination with this new generation of robotic devices, there will be a high demand of extreme flexible instruments which are applied through the working channels. This is exactly where the material nitinol comes into place and enables innovative endoscopic possibilities,” explains Dr.Bernd Vogel, Global Technology and Innovation manager at Alleima Business Unit (BU) Medical and expertise in processing nitinol.
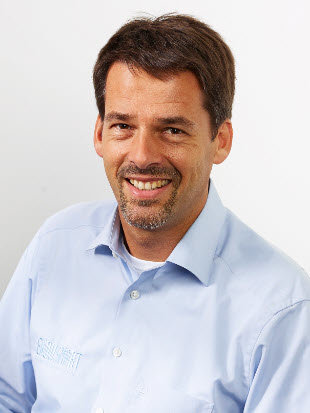
Dr.Bernd Vogel, Global Technology and Innovation manager at Alleima Business Unit (BU) Medical
Nitinol is an alloy with unique super elastic properties that offers major opportunities to the world of soft robotics, especially compared to the limitations of commonly used materials such as rigid stainless steel. Alleima designs and develops customised sensory medical wire since years, which plays a significant role in the manufacture of smart medical devices. This will be key as surgical robotics continue to evolve and further utilise technologies such as cloud computing and AI.
Cutting edge
More operations mean robust demand for the tools required for successful patient outcomes, but surgical blade and scalpel manufacturers looking to carve out a slice of this market must appreciate the delicate balance between protecting the quality of the product while also offering it at a price point that will be in the range of cash-strapped healthcare systems.
Government-funded healthcare systems are under increasing amounts of pressure to deliver cost-effective solutions, but compromises can’t be made when it comes to patient safety
Rajiv Kehr, Managing Director, Aditya Dispomed
Aditya Dispomed, a family business that has manufactured disposable surgical blades and scalpels from its factory on the outskirts of New Delhi since 1970, has seen many of its competitors struggle to achieve this but they only see opportunities over the coming years.
“When it comes to surgical blades, reliability and consistent high performance are crucial. The blade must have a tremendous amount of sharpness to achieve the precision necessary for successful surgery. This comes down to the quality of the material.”
Quality steel combined with robust manufacturing process
Aditya Dispomed products have been at the forefront of some of the critical medical interventions in European hospitals, aiding doctors to perform surgical procedures more effectively.
Upon partnering with Alleima over 2 decades ago, the company sought a strip steel provider willing to engage in close collaboration to create a bespoke and stringent specification.
“A key performance parameter for a surgical blade is consistent sharpness and edge durability. For this to take place, you need a robust manufacturing process, which we have, and the right steel input. Together, that’s the perfect marriage,” says Kehr.
The prudent thing to have done would have been to have a backup. But we never did. We are confident that Alleima will always be there for us for all our needs and that shows the strength of our belief in them.
Rajiv Kehr, Managing Director, Aditya Dispomed
“There are local companies in India that offer quality steel grades, but Alleima’s long history and exemplary credentials in metallurgical innovation and research puts it in a different league – and it was important for us to work with a company of such heritage to build trust quickly in a global market. Apart from that, we needed a partner whom we could rely on. Ultimately, without the steel input, our production stops. We can’t make anything.
Alleima will support Aditya Dispomed launch a number of specialist products in 2024, for different types of blades and as well as a range of microblades. “The core competency of edge, facilitated by Alleima, facilitates our ability to expand into new areas.”
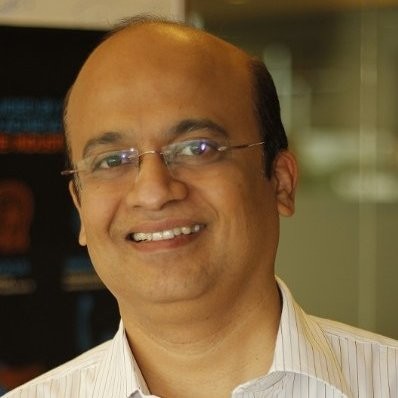
Shailesh Sardesai, Regional Sales Director, Alleima
Shailesh Sardesai, Regional Sales Director from Alleima says: “We have been producing strip steel in Sandviken, Sweden for more than 100 years. Our strip steel provides optimal toughness, edge retention, corrosion resistance, a fine-grain microstructure and precision well suited for the challenging, intricate, and delicate requirements of medical procedures, like bone cutting, ocular and cardiovascular incisions. “With a fully integrated supply chain from melt to final strip product, the company has an excellent system for controlling process parameters and material properties from coil to coil.”
For more information about Alleima and it’s medical products go to www.alleima.com/medical
Contact information
Alleima Advance Materials
1 Commerce Blvd.,
Palm Coast, FL, 32164,
United States
Tel: +1 386 445-2000
Fax: +1 386 447-5113
Email: ms.spc@alleima.com
Alleima Tucson
2424 East Aragon Rd
Tucson, AZ 85756
United States
Tel: +1 520 495 5927
Alleima Zug
Oberallmendstrasse 20a
CH-6300 Zug
Tel: +41 41 761 63 55
Email: sales@alleima.com
Alleima St Imier
Rue de Beau Site 8
CH-2610 Saint-Imier
Tel: +41 32 942 39 20
Email: info@alleima.com
Alleima GmbH
Hansaallee 101
DE-40549 Düsseldorf
Germany
Phone +41 79 69 96 121
Email: strip.emea@alleima.com
Web: www.alleima.com/medical