Company Insight
Sponsored by Repsol
Repsol Healthcare® offers a comprehensive range of polyolefins for pharmaceutical packaging and medical devices
These are 30 grades comprising high and low density polyethylene (HDPE, LDPE), ethylene vinyl acetate copolymers (EVA), and polypropylene (PP), that comply with the strictest medical and pharmaceutical industry standards.
Repsol is a global multi-energy company that is leading the energy transition with its ambition of achieving zero net emissions by 2050. Present throughout the energy value chain, the company employs 24,000 people worldwide and distributes its products in nearly 90 countries. Its customer-focused product and services portfolio meets all consumer needs to around 24 million customers, whether at home or on the move.
To achieve its goal of zero net emissions by 2050, Repsol is deploying an integrated model of decarbonization technologies based on improving efficiency, increasing low-emissions power generation capacity, producing low-carbon fuels, developing new customer solutions, the circular economy, and driving innovative projects to reduce the industry's carbon footprint.
Advances in technologies such as AI and cloud computing are making way for innovation in surgical robotics, which will see better clinical outcomes and reduce the workload for healthcare providers. Furthermore, manufacturers continue to improve robot design so that they are more efficient through innovations in engineering and metallurgy.
According to Tina Deng, medical device principal analyst at GlobalData: “Surgical robots are designed to solve the limitations currently present in minimally invasive surgeries, as well as to improve outcomes in open surgical procedures. These systems are utilised in a variety of surgical procedures, including cardiovascular, general surgery, orthopaedic, neurosurgery, obstetrics, gynaecology, and more. According to GlobalData forecasts, the total surgical robotics market was worth $4.6B in 2020 globally. By 2030, it will have grown at a strong compound annual growth rate (CAGR) of 8.5% to $10.3B, bolstered with the coming marriage of artificial intelligence (AI) and robotics within medical devices.”
“Economic downturns can also create a demand for more cost-effective solutions in healthcare. This could lead to increased interest in surgical robotics systems, as they offer greater efficiency and cost savings compared to traditional surgical methods. Robotic surgery systems allow surgeons to operate with greater precision, reduce complications, and result in faster recovery periods. Because robotic surgery is less invasive, patients typically require shorter hospital stays than they would with traditional open surgery.”
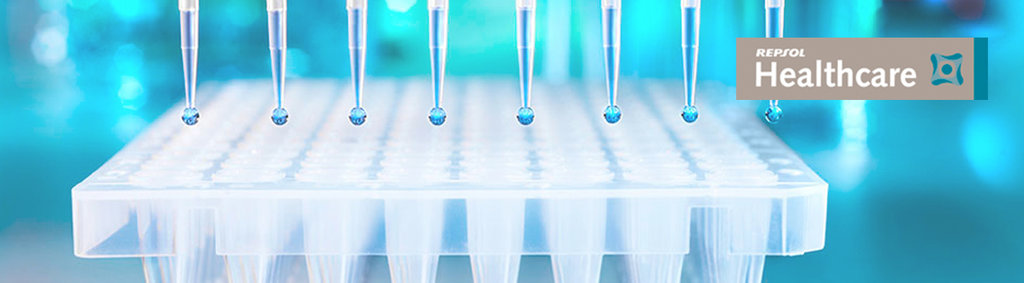
One of the main reasons why electroplating has become an essential part of medical device manufacturing is to improve patient safety by allowing the more durable materials used in implants to be rendered biocompatible.
Repsol Healthcare®
The company's Repsol Healthcare® range offers 30 different polyolefin grades for pharmaceutical packaging, medical devices, and diagnostics.
Repsol is the only producer to provide all four family of products for healthcare applications, and has developed a product portfolio specifically targeted to the pharma and medical industries, adapting its manufacturing facilities, establishing strict production and quality control protocols to meet the strictest requirements according to the industry's Good Manufacturing Practices (GMP).
Repsol Healthcare® product portfolio includes a complete range of polypropylene (PP), high- and low-density polyethylene (HDPE & LDPE) and ethylene-vinyl acetate copolymers (EVA) that cover different melt flow rates and product characteristics. Thus, offering high quality solutions for blow molding, injection molding and film applications for pharmaceutical packaging, medical devices, and diagnostics. Specific grades designed for radiation sterilization have also been designed to maintain product properties intact.
Additionally this product line is available in its chemical recycling or biobased version. These are sustainable alternatives in full compliance with pharmacopeias and biocompatibility testing, providing brand owners and OEMs sustainable solutions to become more carbon neutral and ecofriendly.
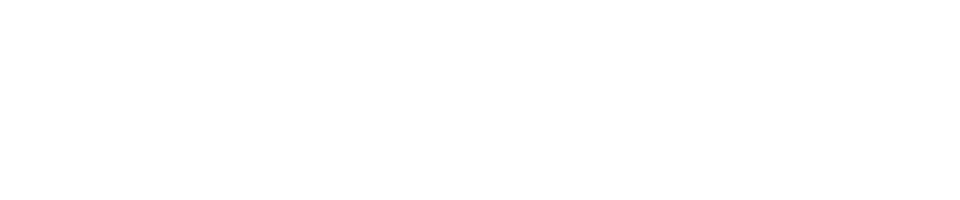
One of the main reasons why electroplating has become an essential part of medical device manufacturing is to improve patient safety by allowing the more durable materials used in implants to be rendered biocompatible.
Repsol and the Circular Economy
In its commitment to sustainability, all Repsol polyolefins are 100% recyclable, and the company already offers its clients a complete portfolio of Circular Polyolefins. Furthermore, their goal is to recycle the equivalent of 20% of their polyolefins’ production by 2030. Furthermore, the company has three extensive petrochemical facilities, two of them located in Spain, Puertollano, and Tarragona, and another in Portugal, Sines. They focus their strategy on the constant generation of value through differentiated products and services.
Repsol has also obtained the ISCC Plus certification for all their petrochemical complexes. They are the first to certify all their complexes to produce circular polyolefins that use oil as a raw material obtained from plastic waste not suitable for mechanical recycling. Also, the certification allows them to market other products such as styrene, polyols, and glycols as circulars.
By being able to guarantee the traceability of the waste used, the company can offer to its customers a product with recycled material for applications that demand high cleanliness and safety requirements such as medical and food packaging or cables.
Repsol has lately unveiled a new advanced ISCC Plus certified bio-based range for pharmaceutical applications that offers a negative carbon footprint, removing more CO2 from the atmosphere than it emits. This range includes first-generation bio-based polyolefins (1G) from sustainably sourced crops, following the ISCC EU 202 best environmental, social, and economic practices and second-generation bio-based circular polyolefins (2G) from bio and organic waste.
The new advanced bio-based range from Repsol offers a negative carbon footprint on a cradle-to-gate methodology under the ISO 14067 standard, removing more CO2 from the atmosphere than the emissions in the supply chain processes. Replacing the traditional feedstock used at their industrial sites with this new bio-based feedstock, which has previously removed CO2 from the atmosphere by photosynthesis during its plantation life cycle, improves carbon footprint to -1 tCO2/t for our first-generation polyolefins and -2,5 tCO2/t for our second-generation polyolefins. Furthermore, this bio-based range is ISCC Plus certified for traceability through mass balance. In addition, the new bio-based polyolefins meet these applications' strict cleanliness and safety requirements.
Contact information
REPSOL
Mendez Álvaro, 44
28045 Madrid (Spain)
Tel: +34 91 75 31 803
Email: sacrq@repsol.com
Web: chemicalsonline.repsol.com