Company Insight
Sponsored by Alleima
Transforming medical technology with nitinol
Nitinol is a smart material with a shape‑memory effect, one of the most fascinating phenomena in material science, making it highly attractive for medical applications. However, as unique as nitinol’s properties are, processing the material is equally challenging. This smart material requires careful manufacturing, and Alleima is a company with more than 20 years of experience in processing nitinol.
Main image: Nitinol components require careful manufacturing and are often handcrafted with a low degree of automation. Credit: Alleima
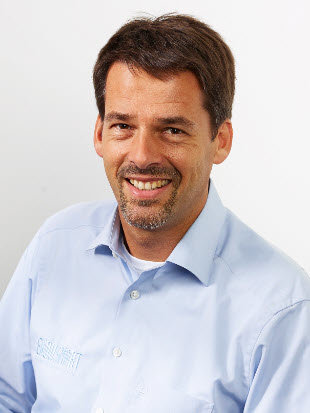
Dr. Bernd Vogel
We asked Dr. Bernd, a recognized nitinol expert who has dealt with nitinol processing since starting his university studies 30 years ago, about the possibilities of overcoming obstacles and automating the processing to achieve smart manufacturing for a smart material.
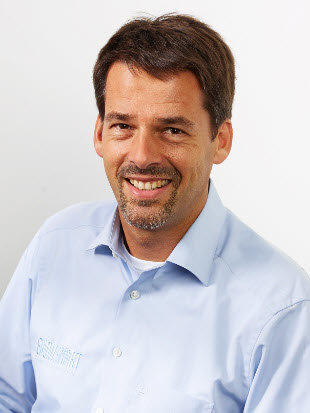
Dr. Bernd Vogel
When asked to simply describe the shape-memory effect, Dr. Bernd Vogel takes out a wire shaped like a heart, straightens it completely, and then slowly dips it into a cup of hot coffe. Immidately the wire returns to its perfect heart shape.
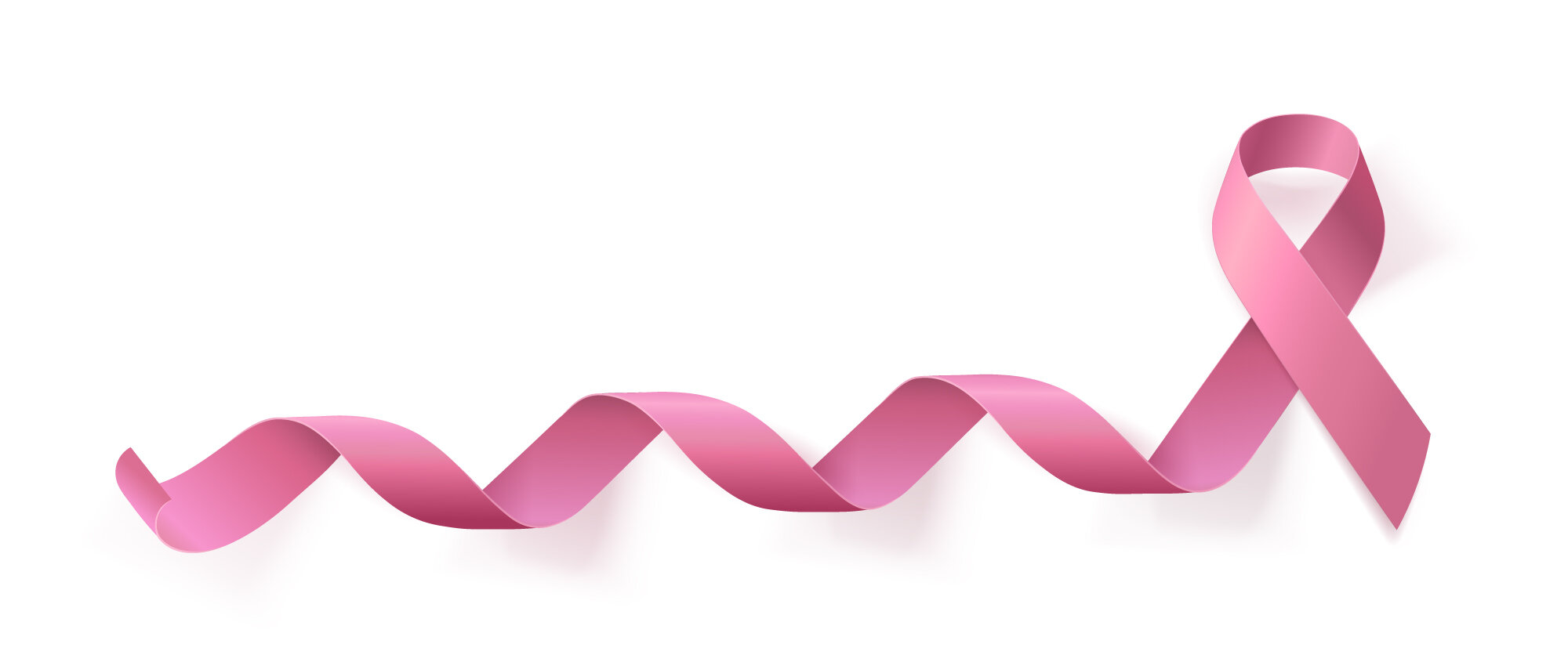
Braiding and Twisting detail center. Credit: Alleima
Lumpectomy surgeries are less invasive, removing less breast tissue and leaving minimum scarring. The U.S. National Institutes of Health released a statement back in 1990 stating that a lumpectomy followed by radiation was preferred over mastectomy to treat early-stage breast cancer, and current studies indicate that this is still the case.
Why did nitinol revolutionize medicine?
In 1962 the researcher William J. Buehler discovered the unique shape-memory properties in a family of nickel-titanium alloys at the Naval Ordnance Laboratory (NOL), naming the alloy family nitinol.
In the medical device industry, many procedures involve the implantation of various metallic constructions. Traditional materials like stainless steel and titanium lack the flexibility and elasticity inherent in living tissues. This biomechanical incompatibility negatively affects adjacent tissue, leading to issues such as the loosening of bone implants. However, nitinol’s properties are much closer to living tissue than any other material. Consequently, nitinol has been continuously used as an implant material for bone fractures. Access to super-elastic nitinol tubes paved the way for vascular implants such as self-expanding stents, filters, and grafts. You can say that the discovery of nitinol revolutionized medicine.
Do standards exist for designers who lack in-depth knowledge of nitinol?
An American Standard of Testing Material (ASTM) committee has developed standards for nitinol-wrought material used as medical devices and implants. These standards define testing methods and specifications for nitinol in the form of wire, tube, and sheet. However, without deeper knowledge, these standards are too broad to source readily available material off the shelf. The lack of standardization allows the industry to develop its standards, resulting in material variation from one supplier to another. It’s important to remember that nitinol’s properties are so sensitive that even slight changes in nickel content or cold work can significantly affect the material’s behavior.
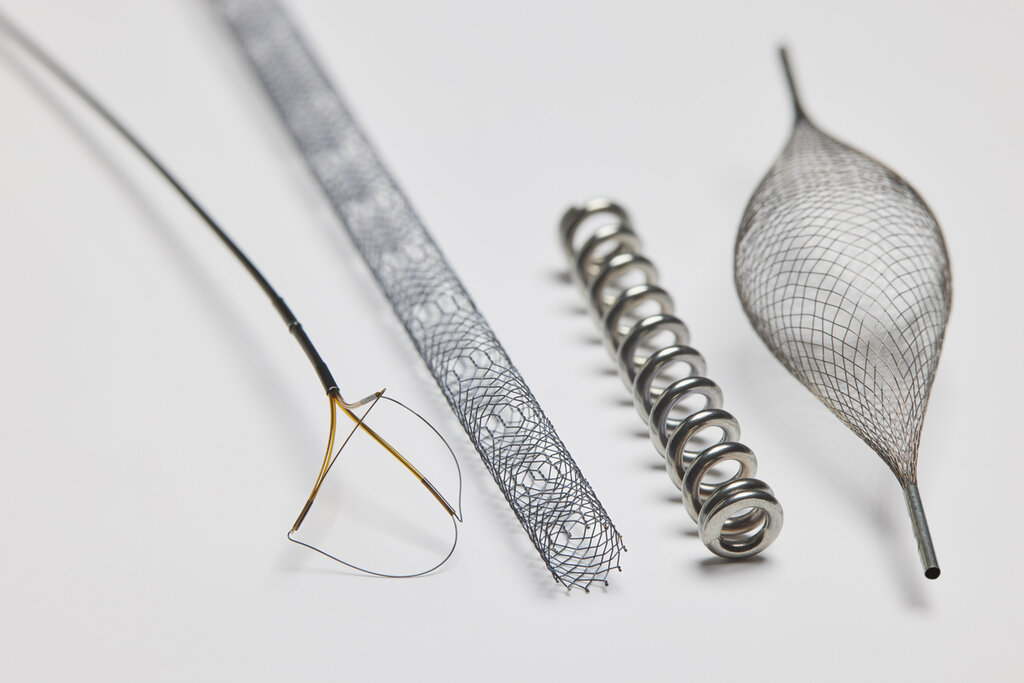
Alleima offers a broad range of nitinol processing capabilities and products. Credit: Alleima
Which processing methods can be applied to nitinol?
The fabrication of stand-alone nitinol components can be categorized into the following three groups:
- Structuring the wrought material:
If the product is fabricated from tubes or sheets, the following methods are suitable: laser cutting, wire Electrical Discharge Machining (EDM), waterjet cutting, and chemical etching. On the other hand, if a wire, strip, or ribbon is needed, profiling would most likely involve abrasive techniques such as grinding. In some cases, eroding or chemical etching to be successful. - Shape setting:
The process required to set the shape is similar whether starting with wire, sheet, or tube material. The structured component from step one must be constrained on a fixture, followed by heat treatment. The heat treatment may involve a salt bath, sand bath, air or vacuum furnace, or various heating methods such as inductive heating.
- Surface finish:
Depending on the heat treatment, the material will have a different surface condition (oxide layer). The resulting surface finish will affect the performance of the instrument. For implants, it will impact durability, corrosion resistance, and other properties.
Which joining methods do you need to consider for nitinol?
If the nitinol component is only one part of the assembly, designers must carefully consider the joining methods. Nitinol can be easily welded to itself using a laser or e-beam. However, one must consider that welds do not have super-elastic properties and should be placed in a section of the assembly where only slight deformation occurs. When joining nitinol to other materials like titanium or stainless steel, the process can be quite difficult. Research has shown successful joining using soft soldering with aggressive fluxes, while resistance or diffusion welding can also be applied. Generally, alternative mechanical options like crimping or shrink-fitting are preferred.
Why is it difficult to convert nitinol fabrication into industrial automation?
A) Deformation resistant applications
Within every process step in processing components in the category of deformation-resistant applications, one must be aware of the effect it has on the properties of the material. The amount of cold work, the heat treatment, the rate of strain, and the number of cycles all impact material properties and therefore change the stress-strain behavior.
Therefore, the industry is having a hard time converting nitinol fabrication steps into industrial automation. Today, medical products made from nitinol are mainly processed through manual operations, handcrafted with a very low degree of automation. This makes the outcome dependent on the worker, and the process is very difficult to validate. That is also why there has been little demand for serial production from the industry. In the last few decades, the alloy became popular in the treatment of peripheral vascular diseases. Stents were the first medical products with high demand. Unfortunately, the variety of needed versions of these implants is so high that the profitability of installing automated processes is questionable. Therefore, these implants are mainly processed with a low level of automation.
There has however been mass production of nitinol articles. The first article in this field was the super-elastic, kink-resistant, nitinol guide wire used in surgical procedures. Using these methods the surgeon can reach a point of interest in the body in a minimally or non-invasive way. Due to its elasticity, the ability of the wire to follow a tortuous path in the body and still rotate smoothly led to improved performance.
B) Shape-restoring applications
Moreover, the largest family in medical instruments is the group of shape-restoring applications. These products are temporarily deformed to be introduced into the body, and when removed, spring back to their original shape without the need to increase the temperature. They are used for various functions such as loops, snares, retractors, and baskets, as well as for removing foreign bodies and blood clots.
In the urological field, there is already a worldwide yearly need for stone retrieval baskets. The same instrument can also be used to catch various stones that are anywhere from 1-12 millimeters in size. Therefore, the diversity of versions needed in this field is very low. This enables the possibility of installing a certain degree of automation in the manufacturing process. The most common version of stone retrieval baskets is manufactured from wires, which form a basket-like structure.
Which recommendations do you give if you want to use nitinol in your medical applications?
When looking into a factory of medical device manufacturers, the quality of the product is certainly the first thing we have to think about. Following this comes the productivity and thereafter, the profitability. These parameters do not have to depend on whether you have an all-hands-on operation or an automated process. You simply have to team up with a partner who is experienced in processing nitinol and knows every process step and what effect it has on the properties of the material. The amount of cold work, the heat treatment, the rate of strain, and the number of cycles, all have an impact on material properties and therefore change the stress-strain behavior.
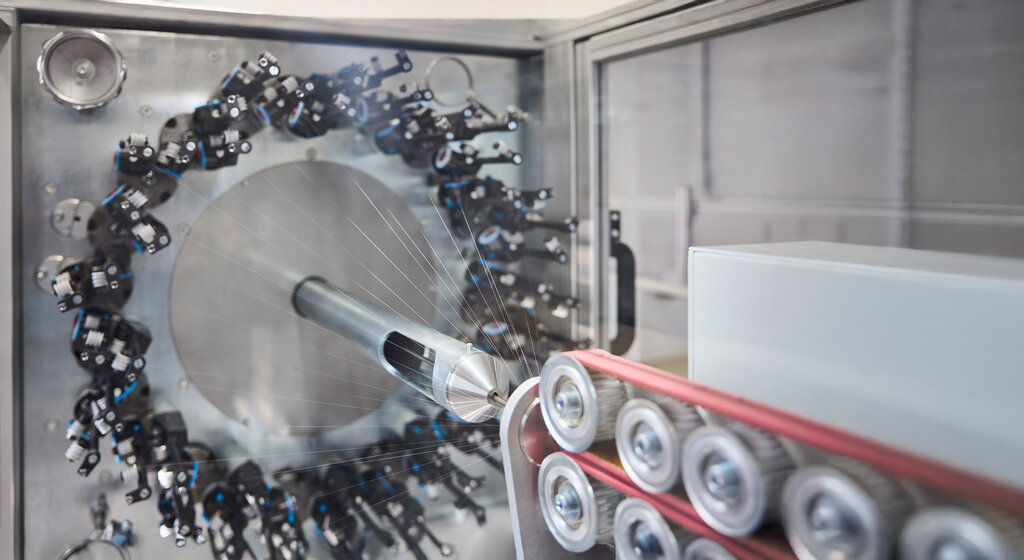
Due to the sensitivity of processing nitinol you need to team up with a partner who is experienced and knows every step and what effect it has on the properties of the material. Credit: Alleima
Alleima is one of those partners with the necessary experience and processing capabilities to bring life-changing medical solutions to life. In my role as Global Technology and Innovation manager I am working with a team of experienced materials specialists, development and mechatronics engineers, quality managers and skilled operators to support our customers realize their ideas and lead them through each stage of the challenging development process, all the way to the market approval. This really sets us apart from the competition.
Contact information
Alleima Advanced Materials
1 Commerce Blvd.,
Palm Coast, FL, 32164,
United States
Tel: +1 386 445-2000
Fax: +1 386 447-5113
Email: sales.pc@alleima.com
Alleima Tucson
2424 East Aragon Rd
Tucson, AZ 85756
United States
Tel: +1 520 495 5927
Alleima Karlsruhe
Wilhelm-Schickard Str. 9c
761 31 Karlsruhe
Germany
Tel: +41 41 761 63 55
Email:sales.ka@alleima.com
Alleima St Imier
Rue de Beau Site 8
CH-2610 Saint-Imier
Switzerland
Tel: +41 32 942 39 20
Email: sales.sb@alleima.com