Molding the World One Seal at a Time
Over the last 50 years, Apple Rubber has designed and manufactured millions of critical sealing solutions across 50 countries. With extensive sealing expertise, Apple Rubber is the trusted source for high-quality medical seals that help save lives. Our engineers utilize state-of-the-art 3D CAD and CAM technology, in-house molding and our Class 10000 ISO 7 Certified Cleanroom to ensure every medical seal meets exact specifications.
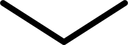
Small and Large Quantity Prototyping for Medical Solutions
In addition to providing expert engineering, Apple Rubber’s in-house manufacturing capabilities also include custom small and large quantity prototyping, which sets us ahead of competitors. Our design engineers work closely with every customer and provide immediate feedback to improve medical seal design, function and future production—saving big on extra costs and lead time.
Through custom prototyping, our engineers will bring your seal designs to life before moving to production. This allows us to reduce design risks, map out the preliminary design process, make customizations where necessary and manage time effectively.
Learn more
Quality Control You Can Count On
The medical industry requires precise quality control to ensure the safety of patients in life-saving applications. With strict regulations in mind, Apple Rubber takes the time to thoroughly test every material, part and seal to ensure it meets necessary standards.
From raw materials to finished products, Apple Rubber performs rigorous quality testing every step of the way, including production process analyzer, tensile, density and FTIR testing. Additionally, Apple Rubber can provide quality documentation from First Article to full IQOQPQ.
Learn more
Expert Engineering, Every Step of the Way
To meet the needs of every customer, Apple Rubber engineers will work with you one-on-one from early design and prototyping stages to production and beyond. With tailored help at every stage, our engineers are able to provide quality, reliable medical seals and devices that can withstand critical environments.
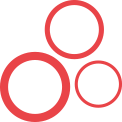
In addition to AS568 standard sizes and ISO 3601 metric sizes, Apple Rubber also carries over 8,000 non-standard sizes in stock at all times. If we don’t have it, we can make it; our in-house tooling capabilities allow for expedited delivery of any size in large or small quantities. While we provide an extensive list of materials to choose from, our standard rubber materials include Viton™, Nitrile, Ethylene-Propylene, Fluorosilicone, Silicone and Neoprene®.

From the most exotic seals to microminiature shapes, Apple Rubber can custom design and mold any rubber seal to meet exact requirements. Some of the most popular custom molded shapes include molded inserts, diaphragms, lip seals, piston seals, bushings, poppets and connector seals. While Apple Rubber can seamlessly produce customized shapes, material selection is also customizable.

The strict regulations of the medical industry require precise sealing solutions that meet high standards. Apple Rubber medical seals offer tighter tolerances and ultra-low defect rates, making them a trusted solution for critical applications. Our fully automated inspection machines ensure all parts are thoroughly tested for both fine defects and size.
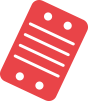
Injection molding produces parts with quicker cycle times than compression or transfer molding. In addition, this type of molding gives manufacturers the ability to produce custom shapes with little flash or rubber waste, as well as an improved versatility in durometer shores, which typically run anywhere from 40 Shore A to 80 Shore A.
Apple Rubber design engineers have expertise through years of solving rubber sealing challenges for a wide range of industries.
For further questions about rubber parts and seals, design, or assistance, contact one of our engineers through our Engineer Request form.
Contact an Engineer